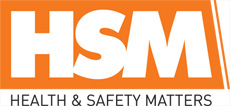
![]() |
Mark Sennett
Managing Editor |
![]() |
Kelly Rose
Editor |
ARTICLE
Five mistakes of HAVS risk management
14 February 2014
Around 300,000 UK employees are estimated to have advanced symptoms of debilitating Hand Arm Vibration Syndrome (HAVS), and over one million users of hand-held or hand-guided power tools face increased risk of the syndrome because they are exposed to HAV above the level set by the HSE.
Stewart McNaughton identifies five of the most common myths and mistakes of Hand Arm Vibration Syndrome (HAVS) risk management.
1. Continuous monitoring of employees’ vibration exposure levels will protect them from HAVS
This is obviously a great starting point, and monitoring does need to be consistent, but monitoring alone – no matter what system you use – won’t protect your employees from the risk of HAVS. It’s only when HAVS risk is managed – when the data generated by robust and accurate monitoring processes is analysed and the appropriate action taken in a timely manner - that an individual is shielded from the risk of HAVS.
2. As long as employees don’t exceed their daily exposure limit value (ELV), they will be fine
An exposure limit value (ELV) of 5 m/s2 A(8) per day is set by the Health and Safety Executive, and critically must not be breached. Encouraging your employees to reach this level each and every day, however, is often ineffective when those employees or individuals have already been noted as at risk of developing HAVS. In those circumstances a continuous exposure reduction plan should be implemented, and a tailored and individual ELV set.
3. Tools emitting high levels of vibration should be instantly replaced
Taking this approach certainly won’t hinder your HAVS risk protection policy, but before you make that costly decision to replace your tools, ensure that you can strike a balance between productivity and vibration emission. It is vibration exposure over a period of time that causes the most harm, not intense vibration over a short time span.
4. Paper based monitoring will suffice
According to current regulations, it’s not wrong to use a paper based monitoring system. Do be aware though, that relying on individuals to record their own vibration exposure times with old fashioned pen and paper can be highly inaccurate. Individuals will often round up or down their exposure times, or may even pluck a figure out of thin air. A digital monitoring system removes all the guess work, accurately recording vibration exposure levels for each individual, and producing effective and manageable data.
5. HAVS monitoring will negatively impact productivity
This doesn’t have to be the case. In fact, the opposite can be true; adopting a digital monitoring process will, in many cases, increase productivity. Your workforce won’t need to spend time manually recording trigger times at the end of each day and the digital support will measure accurate tool trigger time, as opposed to tool ownership time.
Avoiding these pitfalls will go a long way towards ensuring you have a reliable and robust procedure for HAVS risk management, and you’ll no doubt reap the benefits in terms of cost savings too, like other companies such as Carillion Rail, Skanska Utilities and William Hare have done.
Stewart McNaughton is health and safety consultant for Reactec.
MORE FROM THIS COMPANY
- HAV monitoring
- New workplace wearable offers multiple health risk protection
- HAV safety is the goal
- 10,000 safety device sales for Reactec
- Making the invisible, visible
- Track & report HAVS
- Protecting the workforce with technology
- Personalised noise monitoring technology
- What is proximity detection technology and why is it important?
- Health and safety at work statistics
RELATED ARTICLES
- No related articles listed
OTHER ARTICLES IN THIS SECTION