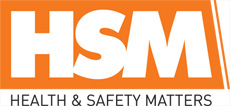
![]() |
Mark Sennett
Managing Editor |
![]() |
Kelly Rose
Editor |
ARTICLE
Getting the most out of your RPE
30 May 2013
Mark Andrews, Scott Safety's product manager - air purified, offers a guide to setting up a successful respiratory protection programme

Mark Andrews, Scott Safety's product manager - air purified, offers a
guide to setting up a successful respiratory protection programme
There are a number of reasons why users choose to wear respiratory protection equipment (RPE) including the law, procedures, personal judgement and health reasons. However, there are just as many reasons why some choose not to wear RPE such as limited access to RPE, user discomfort, compatibility with other personal protective equipment (PPE), a lack of awareness of health risks and how RPE works, and inadequate guidance. Developing a successful RPE programme can help educate workers in the need for RPE and allows employers to track RPE effectiveness.
Globally, both hazard communication and PPE standards are undergoing review to bring about a new set of Global Harmonised Standards (GHS). In the UK, the REACH directive is already defining a new way of classifying and communicating hazards that places responsibilities with both the producer and end user of hazardous chemical containing substances. The improved classification and reporting of hazards will only add to the responsibility of the employer to ensure that proper implementation and documentation of control strategies are in place.
Specific to respiratory, efforts are being made by international industry regulators to harmonise respiratory standards under a common standard, EN 17420, initially intended for publication around 2015. Its intention is to overcome differences in regional standards, for example in the protection ratings allocated to types of respirator - filtering facepieces, halfmasks, fullface and powered air units, providing clarity for manufacturers and users alike on performance characteristics of these kinds of equipment.
An effective workplace risk assessment will identify all factors potentially hazardous to health. In terms of respiratory hazards, it will recognise potential threats arising from environments Immediately Dangerous to Life or Health (IDLH) such as oxygendeficiency/ acute respiratory toxins and will also consider the threat from combinations of respiratory hazards such as mixtures of dusts, fibres and gases. To quantify risk in relation to respiratory hazards, 'hazard ratio' - the ratio between the allowable concentration limit and that which is found in the workplace environment - will be used. RPE type with sufficient protection factor will then be selected to mitigate risk as quantified by the hazard ratio.
Selection procedures Selecting appropriate RPE for protection in a hazardous environment requires a thorough assessment of hazards present. A clear set of selection steps must be followed to determine the type of RPE to be used for the task including consideration of breathing apparatus, filtering masks, powered air or use of compressed airline systems. The HSE's HSG53 document details protection factors offered by various types of RPEfiltering facepieces, halfmasks, full masks and powered-air. With many kinds of filter types available on the market e.g. PSL, ABE, ABEK, ABEKHg selection of the right filter can be confusing. Reputable equipment manufacturers such as Scott Safety offer a website filter selection tool (SureLife) which provides easy selection of a filter for particular respiratory hazard(s).
Even though RPE is designed and certified to accommodate a wide range of the population based on anthropomorphic databases, facial morphology is not the sole determination of fit. Regular fit testing verifies the ability of the end user to don the RPE and obtain a satisfactory fit factor.When fit testing users, alternative sizes and models should be provided to ensure the most appropriate and best performing choice can be made, tailored for the individual.
Employers implementing fit testing should ensure that their employees carrying out the programme are suitably trained or that they contract a qualified specialist provider, as a substantial level of competency is needed to fit test an RPE wearer effectively. Employers are also expected to provide training for their end users in general RPE use and specific use instructions for their RPE.
Maintenance and storage RPE must be inspected and maintained on a regular schedule and stored properly to prevent damage and contamination.
Manufacturer guidelines will provide details on how this should be done. An effective RPE programme needs to provide a suitable area for cleaning, maintaining and storing RPE between uses. It should be a clean area away from the workplace hazard, ideally enclosed lockers or boxes and a suitable hanging facility, if appropriate. If filters are to be re-used they will usually be removed from the RPE and stored in a plastic bag. Other parts of RPE that are either washed or wiped clean need an area to dry naturally before being stored. In some instances, depending on the type of chemical hazard, filters must be changed out after each shift.
New threats such as CBRN, a global influenza pandemic and major industrial incidents, along with common workplace studies by the HSE, NIOSH and other national bodies, have forced manufacturers to further improve respirator effectiveness, for example anthropometric based faceseal and suspension systems, and enhanced communications. As respirators improve, it is important to reflect this in your respiratory protection programme.
There are a number of reasons why users choose to wear respiratory protection equipment (RPE) including the law, procedures, personal judgement and health reasons. However, there are just as many reasons why some choose not to wear RPE such as limited access to RPE, user discomfort, compatibility with other personal protective equipment (PPE), a lack of awareness of health risks and how RPE works, and inadequate guidance. Developing a successful RPE programme can help educate workers in the need for RPE and allows employers to track RPE effectiveness.
Globally, both hazard communication and PPE standards are undergoing review to bring about a new set of Global Harmonised Standards (GHS). In the UK, the REACH directive is already defining a new way of classifying and communicating hazards that places responsibilities with both the producer and end user of hazardous chemical containing substances. The improved classification and reporting of hazards will only add to the responsibility of the employer to ensure that proper implementation and documentation of control strategies are in place.
Specific to respiratory, efforts are being made by international industry regulators to harmonise respiratory standards under a common standard, EN 17420, initially intended for publication around 2015. Its intention is to overcome differences in regional standards, for example in the protection ratings allocated to types of respirator - filtering facepieces, halfmasks, fullface and powered air units, providing clarity for manufacturers and users alike on performance characteristics of these kinds of equipment.
An effective workplace risk assessment will identify all factors potentially hazardous to health. In terms of respiratory hazards, it will recognise potential threats arising from environments Immediately Dangerous to Life or Health (IDLH) such as oxygendeficiency/ acute respiratory toxins and will also consider the threat from combinations of respiratory hazards such as mixtures of dusts, fibres and gases. To quantify risk in relation to respiratory hazards, 'hazard ratio' - the ratio between the allowable concentration limit and that which is found in the workplace environment - will be used. RPE type with sufficient protection factor will then be selected to mitigate risk as quantified by the hazard ratio.
Selection procedures Selecting appropriate RPE for protection in a hazardous environment requires a thorough assessment of hazards present. A clear set of selection steps must be followed to determine the type of RPE to be used for the task including consideration of breathing apparatus, filtering masks, powered air or use of compressed airline systems. The HSE's HSG53 document details protection factors offered by various types of RPEfiltering facepieces, halfmasks, full masks and powered-air. With many kinds of filter types available on the market e.g. PSL, ABE, ABEK, ABEKHg selection of the right filter can be confusing. Reputable equipment manufacturers such as Scott Safety offer a website filter selection tool (SureLife) which provides easy selection of a filter for particular respiratory hazard(s).
Even though RPE is designed and certified to accommodate a wide range of the population based on anthropomorphic databases, facial morphology is not the sole determination of fit. Regular fit testing verifies the ability of the end user to don the RPE and obtain a satisfactory fit factor.When fit testing users, alternative sizes and models should be provided to ensure the most appropriate and best performing choice can be made, tailored for the individual.
Employers implementing fit testing should ensure that their employees carrying out the programme are suitably trained or that they contract a qualified specialist provider, as a substantial level of competency is needed to fit test an RPE wearer effectively. Employers are also expected to provide training for their end users in general RPE use and specific use instructions for their RPE.
Maintenance and storage RPE must be inspected and maintained on a regular schedule and stored properly to prevent damage and contamination.
Manufacturer guidelines will provide details on how this should be done. An effective RPE programme needs to provide a suitable area for cleaning, maintaining and storing RPE between uses. It should be a clean area away from the workplace hazard, ideally enclosed lockers or boxes and a suitable hanging facility, if appropriate. If filters are to be re-used they will usually be removed from the RPE and stored in a plastic bag. Other parts of RPE that are either washed or wiped clean need an area to dry naturally before being stored. In some instances, depending on the type of chemical hazard, filters must be changed out after each shift.
New threats such as CBRN, a global influenza pandemic and major industrial incidents, along with common workplace studies by the HSE, NIOSH and other national bodies, have forced manufacturers to further improve respirator effectiveness, for example anthropometric based faceseal and suspension systems, and enhanced communications. As respirators improve, it is important to reflect this in your respiratory protection programme.
MORE FROM THIS COMPANY
- Chris Ellerby,Scott Safety's Product Manager for PPE,talks about sensory protection products
- Graffiti project goes ahead
- Design award
- Channel of resources
- The importance of low breathing resistance in respirator design
- Changing faces
- PPEshowcase
- Actively tackling hearing loss
- Hearing selector tool
- Advanced protection coverall
OTHER ARTICLES IN THIS SECTION