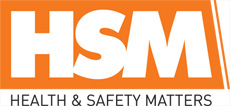
![]() |
Mark Sennett
Managing Editor |
![]() |
Kelly Rose
Editor |
Home> | PPE | >Safety Footwear | >At the sharp end of safety |
ARTICLE
At the sharp end of safety
23 January 2013
David Lummis looks at whether safety footwear with anti-perforation soles are as safe as you would expect Anti-perforation midsoles in safety footwear are designed to prevent entry of sharp objects into the wearer's

David Lummis looks at whether safety footwear with
anti-perforation soles are as safe as you would expect
Anti-perforation midsoles in safety footwear are designed to prevent entry of sharp objects into the wearer's foot when they inadvertently step upon a nail or similar object. The midsole is frequently made of steel and more recently tough puncture resistant material, such as Kevlar, which is embedded within the sole of the safety shoe or boot.
Industries such as construction have a high incidence of puncture injuries and wearing safety footwear that not only prevents crushing to the upper foot, but prevents those midsole penetration injuries that can be so debilitating is essential.
All safety footwear sold in the UK should be manufactured in compliance with standards EN 20344 and EN 20345, which clearly states the performance requirements of shoes or boots to resist crushing or puncture, along with a number of other performance criteria.
These standards, originally established in 2004, ensure the product will 'do what it says on the tin'.
However, the Ministry of Labour in France has reported a number of instances where sole penetration has occurred, despite the product being tested and passed as conforming to the required standard. These concerns were originally raised in 2008, and in 2010 the French authorities brought it to the attention of the European Standards authorities.
Analysis of the problem indicated that there were two major problems: On occasions, metallic anti-penetration inserts are oxidising as the safety footwear is in use and may no longer offer protection.
The existing test for penetration was not suitable to adequately test the new materials and in some cases the material inserts were so narrow they did not offer enough protection across the width of the shoe.
Immediate work started to update the standard and overcome these problems, and a new standard was published at the end of 2011. The new EN 20344 includes a corrosive test that will rule out the poor quality metallic inserts which caused the oxidising problem and an additional penetration test has been introduced for the new non-metallic midsoles to ensure their performance. The 2004 penetration test for metallic midsoles continues in the new standard.
Employer duty of care However, what of the existing products for sale in the marketplace or perhaps on your feet right now? Is there any easy way to determine if you are still protected? The simple answer is no. Without either destruction testing of the footwear or cutting into the sole itself to see the antipenetration inner sole, it is not possible to be sure how your safety footwear will perform against nails and such like. Before going any further though, it is important to state that the incidences of penetration are very small when compared to the volume sold.
In terms of the laws relating to PPE, the products continue to be in conformance with the required standards and in this respect can be legally worn. However, employers have a care of duty to ensure the products they supply will overcome the hazard faced and this may not be the case with older safety footwear that has an anti-penetration midsole.
It is very likely that safety footwear purchased recently will meet the new standard and offer full protection. Once the problem was highlighted and the cause understood, most of the reputable branded manufacturers converted their metallic midsoles to non-corrosive varieties which easily meet the standard's demands. (It would be fair to say that the majority were already supplying higher quality midsoles before this issue was raised).
As a rule of thumb, the cheaper metallic midsoles were used in the more basic and low cost products, to enable them to achieve attractive selling prices.
These midsoles are much more prone to oxidising. Therefore if you are wearing a higher quality, branded product it is significantly more likely you are adequately protected, but this cannot be guaranteed without destructive testing.
For the future, this problem will be completely overcome by adherence to the new EN 20344 2011 standard and all reputable suppliers and manufacturers will advise you.
David Lummis is chief executive of the British Safety Industry Federation
Anti-perforation midsoles in safety footwear are designed to prevent entry of sharp objects into the wearer's foot when they inadvertently step upon a nail or similar object. The midsole is frequently made of steel and more recently tough puncture resistant material, such as Kevlar, which is embedded within the sole of the safety shoe or boot.
Industries such as construction have a high incidence of puncture injuries and wearing safety footwear that not only prevents crushing to the upper foot, but prevents those midsole penetration injuries that can be so debilitating is essential.
All safety footwear sold in the UK should be manufactured in compliance with standards EN 20344 and EN 20345, which clearly states the performance requirements of shoes or boots to resist crushing or puncture, along with a number of other performance criteria.
These standards, originally established in 2004, ensure the product will 'do what it says on the tin'.
However, the Ministry of Labour in France has reported a number of instances where sole penetration has occurred, despite the product being tested and passed as conforming to the required standard. These concerns were originally raised in 2008, and in 2010 the French authorities brought it to the attention of the European Standards authorities.
Analysis of the problem indicated that there were two major problems: On occasions, metallic anti-penetration inserts are oxidising as the safety footwear is in use and may no longer offer protection.
The existing test for penetration was not suitable to adequately test the new materials and in some cases the material inserts were so narrow they did not offer enough protection across the width of the shoe.
Immediate work started to update the standard and overcome these problems, and a new standard was published at the end of 2011. The new EN 20344 includes a corrosive test that will rule out the poor quality metallic inserts which caused the oxidising problem and an additional penetration test has been introduced for the new non-metallic midsoles to ensure their performance. The 2004 penetration test for metallic midsoles continues in the new standard.
Employer duty of care However, what of the existing products for sale in the marketplace or perhaps on your feet right now? Is there any easy way to determine if you are still protected? The simple answer is no. Without either destruction testing of the footwear or cutting into the sole itself to see the antipenetration inner sole, it is not possible to be sure how your safety footwear will perform against nails and such like. Before going any further though, it is important to state that the incidences of penetration are very small when compared to the volume sold.
In terms of the laws relating to PPE, the products continue to be in conformance with the required standards and in this respect can be legally worn. However, employers have a care of duty to ensure the products they supply will overcome the hazard faced and this may not be the case with older safety footwear that has an anti-penetration midsole.
It is very likely that safety footwear purchased recently will meet the new standard and offer full protection. Once the problem was highlighted and the cause understood, most of the reputable branded manufacturers converted their metallic midsoles to non-corrosive varieties which easily meet the standard's demands. (It would be fair to say that the majority were already supplying higher quality midsoles before this issue was raised).
As a rule of thumb, the cheaper metallic midsoles were used in the more basic and low cost products, to enable them to achieve attractive selling prices.
These midsoles are much more prone to oxidising. Therefore if you are wearing a higher quality, branded product it is significantly more likely you are adequately protected, but this cannot be guaranteed without destructive testing.
For the future, this problem will be completely overcome by adherence to the new EN 20344 2011 standard and all reputable suppliers and manufacturers will advise you.
David Lummis is chief executive of the British Safety Industry Federation
MORE FROM THIS COMPANY
- BSIF urges companies to tackle MSD's
- Are you certain it's safe?
- Our Parliamentary update - the journey so far…
- PPE buyers urged to Check-Select-Protect
- A sensible approach to hearing protection
- Respiratory protection – Every breath you take
- PPE, Fit Testing & the RSSS
- Working towards standardisation of the Oil Storage Regulations
- From the CEO's desk: Brexit, the EU Commission and PPE Regulation (EU) 2016/425
- The BSIF comments on the Lofstedt Review
OTHER ARTICLES IN THIS SECTION