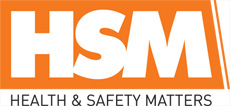
![]() |
Mark Sennett
Managing Editor |
![]() |
Kelly Rose
Editor |
Home> | Health & Wellbeing | >General Health & Wellbeing | >Changes to product standards |
ARTICLE
Changes to product standards
23 January 2013
David Lummis looks at the introduction of new ISO global standards and the implications for UK manufacturers and purchasers European Norm (EN) Standards formally enshrine how a product should perform against known haza

David Lummis looks at the introduction of new ISO global standards and the
implications for UK manufacturers and purchasers
European Norm (EN) Standards formally enshrine how a product should perform against known hazards and are a critical part of the operation of the safety industry throughout the European Union to ensure workers receive adequate and practical protection. These standards can be adopted by national bodies, for example in the UK as BS EN's and, by law, all Personal Protective Equipment (PPE) used in occupational safety within the UK must be approved to a relevant EN Standard and carry the correct CE marking.
EN Standards have been in force for many years and are regularly amended or revised to ensure they remain relevant. Standards are drafted and maintained by a wide ranging group including users, technical experts, manufacturers and distributors to ensure the products maximise protection whilst remaining practical to manufacture and affordable to purchase.
In recent years new 'Global' standards under the International Standards Organisation (ISO) have been introduced. Recent examples have been in clothing and the latest to be developed is for Respiratory Protective Equipment (RPE).
However, it is starting to look like this ideal of globally accepted standards may not be realised with some countries considering remaining on their old standard. With the new standards likely to impose more stringent test requirements leading to increased testing and approval costs, it puts the countries or regions that do adopt the new ISO's at a commercial disadvantage.
In some cases there is no real evidence that current EN standards are not protecting workers adequately, as long as the equipment is correctly used. The new ISO standards may introduce higher specification ideals but in the process they may remove some of the practicality of producing the PPE at cost levels acceptable to its market. If the ISO standards, with more stringent tests are adopted, the higher test costs will inevitably be passed on to the consumer, presenting the very real prospect that less PPE will be purchased and used because the price has risen.
Another potential outcome is that less knowledgeable purchasers will be driven towards the ever increasing range of counterfeit and illegal products purporting to be PPE, as they appear to offer an opportunity to save money.
To compound this situation, Europe through the Vienna agreement, has undertaken to immediately adopt any new ISO standards and replace the existing CE standard, which becomes obsolete. This means that European and therefore British companies may be forced to adopt the more stringent testing requirements of the new ISO standard, while other worldwide manufactures can avoid the additional costs. The situation is further complicated when the new PPE Directive comes into force in a couple of years' time. It is very likely that CE approval certificates will be time limited to 5 years, which will mean all products will need to be retested to the new standard within that time frame. A very expensive and time consuming project that will stretch test house facilities to the limit.
The BSIF understands the need to update standards to meet changing requirements and to ensure that the workforce is protected. We actively support and are leading contributors to revisions of this type. However, where the adoption of new standards cannot demonstrate a quantifiable improvement in safety but will result in increased testing costs, our belief is that the increase in costs will reduce the use of PPE in the workplace, compromising worker safety. Our recommendation is that any new standards should not be adopted without extensive consultation and potential revision.
Adding cost without adding benefit by satisfying a theoretical improvement in performance is not good safety practice, nor is it good business practice. We should focus on areas where improvements to safety will bring strong benefits and improve education and training, which means that correct usage of existing products, will quickly result in improvements to prevent long term harm.
European Norm (EN) Standards formally enshrine how a product should perform against known hazards and are a critical part of the operation of the safety industry throughout the European Union to ensure workers receive adequate and practical protection. These standards can be adopted by national bodies, for example in the UK as BS EN's and, by law, all Personal Protective Equipment (PPE) used in occupational safety within the UK must be approved to a relevant EN Standard and carry the correct CE marking.
EN Standards have been in force for many years and are regularly amended or revised to ensure they remain relevant. Standards are drafted and maintained by a wide ranging group including users, technical experts, manufacturers and distributors to ensure the products maximise protection whilst remaining practical to manufacture and affordable to purchase.
In recent years new 'Global' standards under the International Standards Organisation (ISO) have been introduced. Recent examples have been in clothing and the latest to be developed is for Respiratory Protective Equipment (RPE).
However, it is starting to look like this ideal of globally accepted standards may not be realised with some countries considering remaining on their old standard. With the new standards likely to impose more stringent test requirements leading to increased testing and approval costs, it puts the countries or regions that do adopt the new ISO's at a commercial disadvantage.
In some cases there is no real evidence that current EN standards are not protecting workers adequately, as long as the equipment is correctly used. The new ISO standards may introduce higher specification ideals but in the process they may remove some of the practicality of producing the PPE at cost levels acceptable to its market. If the ISO standards, with more stringent tests are adopted, the higher test costs will inevitably be passed on to the consumer, presenting the very real prospect that less PPE will be purchased and used because the price has risen.
Another potential outcome is that less knowledgeable purchasers will be driven towards the ever increasing range of counterfeit and illegal products purporting to be PPE, as they appear to offer an opportunity to save money.
To compound this situation, Europe through the Vienna agreement, has undertaken to immediately adopt any new ISO standards and replace the existing CE standard, which becomes obsolete. This means that European and therefore British companies may be forced to adopt the more stringent testing requirements of the new ISO standard, while other worldwide manufactures can avoid the additional costs. The situation is further complicated when the new PPE Directive comes into force in a couple of years' time. It is very likely that CE approval certificates will be time limited to 5 years, which will mean all products will need to be retested to the new standard within that time frame. A very expensive and time consuming project that will stretch test house facilities to the limit.
The BSIF understands the need to update standards to meet changing requirements and to ensure that the workforce is protected. We actively support and are leading contributors to revisions of this type. However, where the adoption of new standards cannot demonstrate a quantifiable improvement in safety but will result in increased testing costs, our belief is that the increase in costs will reduce the use of PPE in the workplace, compromising worker safety. Our recommendation is that any new standards should not be adopted without extensive consultation and potential revision.
Adding cost without adding benefit by satisfying a theoretical improvement in performance is not good safety practice, nor is it good business practice. We should focus on areas where improvements to safety will bring strong benefits and improve education and training, which means that correct usage of existing products, will quickly result in improvements to prevent long term harm.
MORE FROM THIS COMPANY
- BSIF Safety Awards 2020
- The winners take it all
- Health & Safety North
- Clean Air? Take Care! campaign kicks off
- Selling of KN95 face masks leads to jail sentence
- Launch of ACoP consultation
- Managing the risk of vibration
- Buying fake risks lives
- Fit2Fit: Accreditation of choice for fit testers
- The fight against fake and illegal PPE continues
RELATED ARTICLES
- BSIF: Covid-19 Update
- Dust tight
- SAFEContractor for 5th year
- BSC welcomes proposals to slash legal costs in personal injury claims
- Get some insight
- Asbestos remains number one killer
- Chemical exposure course goes more than skin deep
- Getting workers involved in safety
- Dual drug testing
- On-site health screening
OTHER ARTICLES IN THIS SECTION