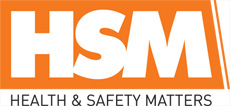
![]() |
Mark Sennett
Managing Editor |
![]() |
Kelly Rose
Editor |
Home> | Handling & Storing | >Lifting Equipment | >Thirsty work |
ARTICLE
Thirsty work
23 January 2013
Juice consumption has increased by 50% over the last 10 years which is why leading juice supplier Gerber called on automatic vehicle loading specialist Joloda to help it save costs, increase cross dock efficiencies, i

Juice consumption has
increased by 50% over the
last 10 years which is why
leading juice supplier Gerber
called on automatic vehicle
loading specialist Joloda to
help it save costs, increase
cross dock efficiencies,
improve health & safety and
reduce its carbon footprint
while moving large volumes
of palletised goods.
Jolada has helped Gerber safely expand capacity at its Bridgwater distribution site in several ways.
These included supplying Gerber with 2 loading docks at the factory warehouse and 2 unloading docks for the storage warehouse which supplies the supermarkets and wholesalers. Joloda also supplied 4 trailer systems to load and unload from these automatic docks systems, and to take the pallets of juice to the chilled storage.
When the juice is produced the production siteabd packaged on to pallets these pallets are loaded from the production area to the loading bay with Joloda loading docks, by Laser guided vehicles (LGV's).
When the pallet is received onto the dock the Joloda Hydraroll control system identifies which type of pallet it is, positions and accumulates automatically the pallets into two accurate rows and using a traffic light system indicates to the driver that the dock is full and ready for loading to the trailer. 4 slipchain trailer systems, are used to transport the pallets from the production site to the chilled warehouse.
The slipchain system enables 26 pallets to be loaded/unloaded from dock to trailer in 90 seconds while improving safety in the loading bay area.
Jolada has helped Gerber safely expand capacity at its Bridgwater distribution site in several ways.
These included supplying Gerber with 2 loading docks at the factory warehouse and 2 unloading docks for the storage warehouse which supplies the supermarkets and wholesalers. Joloda also supplied 4 trailer systems to load and unload from these automatic docks systems, and to take the pallets of juice to the chilled storage.
When the juice is produced the production siteabd packaged on to pallets these pallets are loaded from the production area to the loading bay with Joloda loading docks, by Laser guided vehicles (LGV's).
When the pallet is received onto the dock the Joloda Hydraroll control system identifies which type of pallet it is, positions and accumulates automatically the pallets into two accurate rows and using a traffic light system indicates to the driver that the dock is full and ready for loading to the trailer. 4 slipchain trailer systems, are used to transport the pallets from the production site to the chilled warehouse.
The slipchain system enables 26 pallets to be loaded/unloaded from dock to trailer in 90 seconds while improving safety in the loading bay area.
MORE FROM THIS COMPANY
OTHER ARTICLES IN THIS SECTION