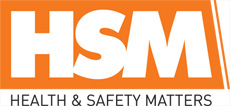
![]() |
Mark Sennett
Managing Editor |
![]() |
Kelly Rose
Editor |
Home> | Breathing Safely | >Dust and Fume Extraction | >Stone dust extraction |
Stone dust extraction
11 February 2019
Stone dust extraction is a challenging problem for dust extraction system designers

Masons tend to produce high volumes of dust; the dust is abrasive; and it’s potentially very harmful. Added to this, in a very traditional industry such as masonry it is still common to meet end users who “have been breathing this in all my life and it’s never hurt me”.
Water is commonly used as a solution to stone dust extraction. Water walls or wet filtered benches are commonly seen as standard solutions, but these can introduce more issues. Water-based filtration is only generally effective to 10 microns, so HEPA after filtration is usually required, and HEPA filters don’t like wet atmospheres. In addition, a wet filtration system means handling and disposing of sludge, and a system that can potentially freeze in cold weather.
Engineers sometimes recommend extraction arms but the abrasive nature of stone dust means arms (and ducting) have a short life span, and of course only have a very small effective area – meaning operators must continually move the arm while working.
However, there are some key factors in stone dust which conversely make it easier to handle than some dusts. Stone dust is non-explosive; this alone can make system design simpler, and enable us to consider systems that would not be suitable for many metallic dusts.
So what’s the answer? A well-designed high-volume dry filter system, configured to make cleaning and emptying easy for operators, can solve many problems.
AirBench offers pulse-cleaned downdraught benches; its AirBench RP range; and also pulse-cleaned cross-draught systems – VertEx VP.
In either case, AirBench moves large volumes of air, slowly, across a wide area. It designs AirBench RP models for operators to work on the bench surface, in place of a banker; whereas VertEx VP can be used to build an extracted wall or a full containment booth using its VB modular booth system.
In either case, operators do not need to interfere with the operation of the dust extraction system while working. Users simply switch on and work within the effective area of the dust extractor; cleaning is on-demand when required.