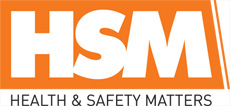
![]() |
Mark Sennett
Managing Editor |
![]() |
Kelly Rose
Editor |
Home> | Managing Health & Safety | >Safety Software & Documentation | >Lessons in safety - Feb 23 |
Lessons in safety - Feb 23
30 January 2023
Data – it’s what you do with it that counts, says Matt Powell-Howard.
AS HSE professionals, it’s our responsibility to monitor health and safety performance - the Management of Health and Safety at Work Regulations 1999 require employers to have arrangements for the effective planning, organisation, control, monitoring and review of preventive and protective measures. Measuring is also part of Plan-Do-Check-Act cycle that’s included in the ISO 45001 standard.
But it can be easy to get caught in producing a glut of data because we can and because, in some organisational cultures, the profession still has to prove it’s ‘worth’. The problem with measuring everything is that it can become a chore and a bore; colleagues and leadership turn off when faced with a raft numbers in amongst all the organisational KPIs.
What should we measure?
Every intervention and its associated measure(s) should be seen as a safeguard in building a multi-layered defence against a hazard(s). Incidents often happen when there are multiple failings in your safeguards – effective, accurate and timely reporting can help you to spot these failings before they ‘stack’ and an incident happens.
A combination of different measures – a balanced scorecard – can also help you to build an accurate picture of what’s going on and prevent your organisation from being lured into a false sense of security. For example, a low injury or ill-health rate, even over a period of years, is no guarantee that risks are being controlled and that safety systems and controls are working as you intended. This is particularly true in organisations where there is a low probability of accidents; the historical record can be a deceptive indicator of safety performance and can lead to complacency.
The Health & Safety Executive’s diagram from its Developing process safety indicators guide provides a useful illustration of the way in which different types of measures can work together – active/reactive, leading/lagging, inputs/outcomes. Although developed for the process industries, the guide also provides useful information and a six-step process which could be adapted or selected from, for many industries.
How we use data
Measuring and monitoring is one of those tasks that really puts our soft skills, such as analysis, communication and influencing, to the test.
Many health and safety measures are not of success, but negatives or the consequences of failure – injuries, death, company costs etc. These are often – not always – used to drive avoidance of certain behaviours, and there is a place for them. But there is also a place for performance data with positive connotations which can be effective in encouraging worker engagement in health and safety practices and to help identify good practices that are achieving positive results elsewhere in a business.
“Health and safety data is widely collected and reported. From accident rates and near miss statistics, to training course completion, there’s a wealth of data used to describe health and safety performance. However, the key to driving improvements is through comprehensive understanding of this data. A low accident frequency could be due to excellent safety performance, or due to under-reporting. For this reason, setting targets can sometimes be counterproductive, effective progress comes from thorough understanding of the data sources, trends, and forecasts.”
Dianne Mitchell, global safety governance & compliance manager at Jaguar Landrover
The NEBOSH Diploma for Occupational Health & Safety Management Professionals syllabus explores measuring and monitoring in further detail. For more information and to read the full syllabus, visit: www.nebosh.org.uk/nationaldip
Matt Powell-Howard is head of product development at NEBOSH. For more information, visit www.nebosh.org.uk
- Lessons in safety
- New qualification for process industries
- Lessons in safety - September 22
- Lack of environmental guidance at work
- ISO 45001 – Establishing a global standard
- NEBOSH develops global qualification for the process industries
- Lessons in safety - December 21
- Lessons in safety
- NEBOSH Diploma can lead to 16% salary boost
- Environmental qualifications in demand