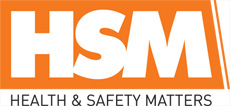
![]() |
Mark Sennett
Managing Editor |
![]() |
Kelly Rose
Editor |
It's in our hands
07 March 2023
Tackling the significant environmental impact of PPE should be top of the agenda in industry, says Nik Rilatt.

ENVIRONMENTAL, SOCIAL and Corporate Governance (ESG) is an issue growing in importance for many organisations and industries, not least in the industrial landscape where environmental impact can often be significant. With PPE being responsible for a large portion of this impact – and the growing use of it – tackling sustainability in PPE is not an issue to be sidelined.
From single-use PPE products like gloves and masks through to clothing, the need for more sustainable options is being recognised by industry and PPE providers and there are innovative products emerging as a result.
Whether it’s the material used to make products, processes executed to manufacture them or what options are for a product when it reaches end-of-life, there are some innovations in the PPE market that aim to address the growing issue of sustainability.
Sustainability in manufacturing processes
When it comes to sustainability best practice in PPE, it’s important to consider manufacturing processes and how the item can be disposed of as much as the end product itself. The carbon emissions resulting from the manufacture of PPE is a significant portion of its impact. Partnering with suppliers that work with manufacturers committed to net zero operations is crucial if the carbon emissions of the industry are ever to be addressed. Conversely, manufacturers should also be putting pressure on suppliers to only work with those who can demonstrate commitment to net zero processes.
The raw materials manufacturers use can play a key part in reducing carbon output. The oven curing process for a single-use glove is 115-150 degrees. One of the latest material innovations to come to market is a chemical, man-made product which can be cured at 90 degrees. When 20 per cent of the energy used to produce a mass-manufactured consumable like a single-use glove can be saved in this way, it can have a significant impact on the entire eco system of a product.
Even the use of innovative packaging solutions should be considered in the quest for sustainability. Those that omit single-use plastic, are made of biodegradable or recyclable materials, or are designed to be space-saving and lightweight – to reduce emissions in transportation – should be key factors when implementing sustainable processes.
At RS, we champion innovations like this and put ESG high on our agenda when choosing suppliers to work with. We physically audit their factories to ensure their ESG claims are bona fide, their practices are ethical and their staff are well looked after. This is particularly important for organisations as, when using firms where the supply chain cannot be verified, they could be at risk of procuring fake and non-compliant PPE.
Prioritising recycled and recyclable PPE options
During the pandemic, PPE became about mass supply and the world scrambled to access the sought-after global stocks. This meant innovation slowed down, but it is now ramping up again with new products coming to market. With a growing range of sustainable PPE solutions now available, there really is no excuse not to prioritise use of these options. As a PPE specialist solutions provider, we’re working with a number of suppliers that offer sustainable products, whether these be made from recycled materials, can be recycled after use or are biodegradable. Our aim is to ensure sustainability is the normal go-to, not an option.
When it comes to commodities like single-use gloves, which are used in a variety of industries in big volumes, opting for a biodegradable solution is a no-brainer. Unigloves BioTouch biodegradable nitrile gloves are the very first kind to offer 90 per cent biodegradation in 490 days which, when compared to traditional nitrile gloves that can take more than 100 years to decompose, is a remarkable development.
Even PPE clothing is undergoing a real sustainability revolution, from items designed to replace single-use through to workwear made with planetary preservation in mind. In industries like food processing where single-use aprons can be a real contributor to landfill, more durable and reusable aprons are available. Made to be washable at the temperatures required to maintain food safety and therefore regulation compliance, these offer an option that can be used to replace up to 260 disposable garments. This saves the equivalent of a football pitch-sized covering of plastic going to landfill, on every six employees. With high-performance workwear items from brands like EarthPro, which are made from fabric made up of recycled plastic, even less harmful disposable plastics are going into landfill and impacting the environment. Even consumables like hand towels are being subject to sustainable makeovers: the Kimberley Clark RightCycle programme has diverted more than 1,500 tonnes of hard-to-recycle non-hazardous PPE from landfill and incineration through its dispenser installation and recycling service, and PPE recycling service.
Not costing the Earth
It’s understandable, particularly in a challenging economic climate, that cost is a significant factor in PPE purchasing decisions, and when there is the perception that sustainable equals unaffordable, it can become a barrier to adoption. However, along with the growing pressure to prioritise ESG making it a key priority for many organisations, there can be cost benefits to choosing more sustainable products.
In food processing, which requires the highest levels of hygiene, over an eight-hour shift there is more risk of contamination with multi-use gloves – which may be the case if less durable ones mean more changes. Using a higher volume of lower quality gloves can be a false economy, as using thicker ones that might be marginally more expensive can still be the cheaper option as they will last longer. And of course, it will reduce the amount going into landfill.
By working with a specialist provider that can provide site surveys, ascertain requirements and suggest the best products for the job – all while maintaining regulatory compliance – savings can be achieved, while keeping sustainability goals at the heart of purchasing decisions.
There’s still a way to go with sustainability in PPE and a lot more work to be done, but the industry and providers are making steps in the right direction. There is a cultural step-change that needs to happen, where sustainability comes first and then commercials fit around that. However, as the innovations emerge along with a better understanding of the value of quality PPE solutions, the more accessible and commercially viable the options become. Working with a specialist can help organisations navigate the PPE products minefield and make decisions that are beneficial for both the business and the planet.
Nik Rilatt is product & procurement manager for RS Safety Solutions. For more information, visit https://uk.rs-online.com
- Retractable barriers and accessories
- Listen to the experts when it comes to hearing protection
- Experts for life
- Easy-to-use fume extraction
- Protect what matters - September 24
- RS now stocking Sundstrom’s respiratory range
- Listen to the experts when it comes to hearing protection
- RS charity spins out washing machines for Uganda communities
- PPE essentials in construction
- Safety harnesses selection