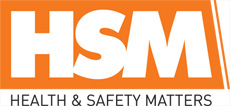
![]() |
Mark Sennett
Managing Editor |
![]() |
Kelly Rose
Editor |
Home> | PPE | >General PPE | >PPE essentials in construction |
PPE essentials in construction
09 September 2015
Personal Protection Equipment Essentials in Construction...George Elliott, technical service engineer at 3M and Amanda Bradley, global category manager – PPE at RS Components discuss available health and safety guidance and the importance of selecting the right personal protection equipment (PPE) for the construction industry.
Preventing injuries and occupational ill health is obviously a key priority for any business or organisation, but the broad variety of activities taking place on construction sites makes the sector one of the most hazardous. Certainly there has been a significant reduction in the numbers and rates of injury in the construction industry over the past 20 years, according to the latest available official health and safety statistics (2013/14). Nonetheless, construction inherently remains a high risk industry in terms of potential injuries: although accounting for approximately 5% of employees in Britain, the sector accounted for 31% of fatal injuries to employees and 10% of reported major or specified injuries.
Regulations
Earlier this year, the Health and Safety Executive (HSE) issued the latest regulations for managing health and safety in construction, the Construction (Design and Management) Regulations 2015, which came into force as of April 6, 2015. Those with duties under CDM 2015, including workers, contractors, designers and clients, all have a legal obligation to consider and plan for safety including identifying, coordinating, eliminating, reducing or controlling foreseeable risks that may arise during every aspect of the design and construction, as well as the maintenance and use of a building when built.One key factor for organisations to consider is the provision and use of PPE. In the construction industry there are many environments and situations where there are risks to health and safety that cannot be adequately controlled in other ways. Key requirements are to meet the PPE Regulations 2002 and the PPE at Work Regulations 1992, which are not industry specific but include duties concerning the provision and use of PPE and require that equipment is: fit-for-purpose, maintained and stored properly, provided with instructions on safe use, and used correctly by employees.
Options
As one might imagine, there are a multitude of PPE options specifically developed in many cases for use in the construction sector. Examples include safety harnesses for working at heights, high-visibility jackets and bibs, respiratory protective equipment, gloves, safety shoes and boots, industrial safety helmets, bump caps, safety goggles and spectacles, face shields, communications headsets, ear defenders, ear plugs, and kneeling and seating mats.
To ensure the appropriate kind of PPE is selected to provide adequate protection, one must consider the hazards of the environment. For example, ejected particles travelling at high speed from an angle grinder or debris from concrete breaking and falling objects are commonplace on construction sites. Along with other control measures, appropriate head, face and eye protection are often necessary in these circumstances.
Compatibility
A major consideration for employers is the demands of specific tasks, including the physical effort and the length of time PPE needs to be worn. Another is where the use of the specific PPE actually increases the level of risk or adds a new risk. For example, if a user is wearing more than one item of PPE such as respirator, then does this mean that the fit of their safety goggles will be compromised? Compatibility between products is therefore important.
Another risk can be communication difficulties: according to Control of Noise at Work Regulations 2005, audible warning signals such as speech or safety alarms need to be heard above the sounds reproduced at the ear. These regulations also dictate a noise level of 85 decibels – for a daily or weekly average exposure – at which employers must provide hearing protection such as ear defenders or earplugs.
Substances
One especially important area in the construction industry is the use of disposable and reusable respiratory protective equipment (RPE) in environments where users can be vulnerable to threats such as gases, vapours and particulates such as asbestos and silica dust.
The Control of Substances Hazardous to Health (COSHH) regulations guidance states that: where RPE is required, it must have the correct Assigned Protection Factor (APF), be suitable for the work in hand, compatible with other protective equipment, fit-tested where appropriate and worn correctly. As an example, many construction activities such as cutting, grinding and drilling stone and concrete will generate respirable crystalline silica dust, which can cause lung disease. The HSE suggests RPE should have a minimum APF of 20 in this environment. A practical guide from the HSE is also available on the subject and provides essential guidance and a list of the do’s and don’ts for the use and supervision of RPE.
Another issue covered by the COSHH regulations is hazards to skin: wet concrete, resins, hardeners and sealants are just a few of the substances that can cause health problems, meaning that protective coveralls will often be required.
Overall, and in addition to the hierarchy of control measures, selecting the correct PPE that offers adequate protection as well as being suitable for the activity is crucial in helping to minimise hazards on the construction site.
Further information and a wide range of personal protection equipment can be found at the 3M PPE site and at uk.rs-online.com
- RS charity spins out washing machines for Uganda communities
- Listen to the experts when it comes to hearing protection
- Safety harnesses selection
- RS now stocking Sundstrom’s respiratory range
- Experts for life
- Listen to the experts when it comes to hearing protection
- RS now stocking Sundstrom’s respiratory range
- Protect what matters - September 24
- Sustainability goals
- Safe space to share health and safety professionals’ knowledge