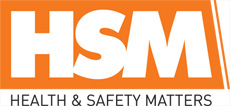
![]() |
Mark Sennett
Managing Editor |
![]() |
Kelly Rose
Editor |
Home> | Breathing Safely | >Gas Detection and Monitoring | >Invisible danger |
Invisible danger
10 September 2020
Businesses using gas within their process need to monitor the levels to ensure employee safety. To ensure the right fixed gas detection system is used for the right job there are many factors that need to be considered. Nathan Marks provides an insight into this important piece of kit.
IF A business or organisation is using any form of gas within a process, they will usually need to monitor the gas levels to ensure employees are protected against any adverse effects. An initial site investigation will most likely be completed using portable or handheld devices.
The environment, the processes being used within the area and which gases are likely to be present throughout the process will all determine whether a fixed gas detection system is the best solution to provide continuous and reliable monitoring and measurement. For example, an explosive atmosphere on a chemical plant would require a very different system compared to a process where a single employee must enter an environment infrequently for a short duration. The need for a gas detection system, the type and complexity of the system would be very different.
The types of environments where fixed gas detection systems are installed are almost endless. Apart from obvious settings such as oil, gas, petrochemical or other explosive atmospheres, applications can also include manufacturing and assembly lines, engineering works, spray booths and paint shops the automotive industry and enclosed garages, hospitals and medical laboratories, universities and schools, swimming pools, indoor karting tracks, farming and botanicals or bioenergy power plants.
Typically, a gas detection system is designed to measure one or more of the following, a toxic gas, an explosive gas, oxygen (depletion/enrichment) and/or VOCs – there could be many variants depends on the user requirements but as a general rule of thumb this is a good starting point.
A system can be one standalone gas sensor with a display, a single control panel with one sensor connected to it, a panel with one sensor and a sounder/beacon, right up to a panel with multiple sensors/sounders/beacons/ panic buttons all communicating with a building management system to control ventilation, door entry systems etc. The clear picture is that every gas detection system is different.
With multiple aspects to consider when looking to install a fixed gas detection system, the best place to start is with a site survey. Considering all the different requirements thoroughly at the outset will help to optimise the system performance whilst ensuring the logistics of the installation run smoothly.
While there are no specific standards to meet regarding the survey or the location of equipment, there are guidance documents available. BS EN 60079-29-2 2007, for example, provides a comprehensive overview of the selection, installation, use and service of fixed gas detection systems.
From a safety perspective, it is good practice to install the control panel in an adjacent room (or outdoors in some circumstances), away from the environment where the detectors will be located, whilst also being easily accessible for servicing.
A key consideration for sensor positioning is the weight of the gas/es being monitored. For some gases which are lighter than air (with a molecular weight of less than 29), access to allow the fitting of sensors at height can be a challenge and may require specialist equipment when working at height. Accessibility can also sometimes be an issue for the detection of heavier gases, when attempting to install a sensor closer to floor level. There may also be localised requirements for SIL approvals or ATEX rated products.
Aftercare
Gas detectors require ongoing aftercare servicing and re-calibration to ensure the system is operating correctly. Considering how they will be accessed safely before choosing a final location is key, particularly in controlling costs for installation but also on-going maintenance visits.
In extreme environments, extra measures are often necessary to ensure the system is as robust as possible and protected against the elements. As an example, here at Shawcity we recently carried out an installation on a marine jetty where the harsh conditions could potentially reduce the lifespan of the system. To combat the environmental impact, GRP (glass-fibre reinforced polyester) enclosures were fitted and modifications were made to the system to ensure that only the serviceable parts were open to the elements whilst still ensuring that accurate measurements are successfully logged via a cloud-based application.
Cabling routes are another consideration. Finding suitable cable routes can be challenging (especially in older buildings) and can have a major impact on the duration of an installation. Cable length for both power and signal strength requirements is also key as it’s easy to underestimate.
It is important to remember that cabling must be installed so it remains protected against mechanical or malicious damage. The smallest cuts or abrasions can affect the performance of a cable and lead to compromised system performance.
Typically, a non-switched fused spur should be made available to power any system. In some cases, the system will be critical to the client’s premises and any back-up batteries in the panel or power supply units may not suffice, so an uninterruptable power supply (UPS) may be required. The autonomy time (usually requested by the client) will often determine the size of the UPS and it should be located with adequate ventilation near the control panel for easy service access.
In terms of experience, personally I have been involved with complex service & site installations across various industries for over 20 years and have amassed qualifications from various areas. My early career was focused on electrical and electronic principals, then over a decade looking after large multiple sites for a singular, high security client’s electronic security requirement. Every site presents a different set of challenges and having a clear specification from a detailed survey at the outset is a huge factor, it makes all parties (clients, consultants and installers) take a step back to really examine the requirements, processes and needs of the application.
Safe installations
When our team is working on site either installing a new system or servicing an existing one, our own health and safety measures mean we ensure everyone on site is protected from process gases through the use of personal or portable units, so the environment is constantly monitored for any risk.
Our fixed gas service engineer, Matt Jordison, recently shared his thoughts on our day-to-day activities.
Matt said: “Although I’m qualified in Electronic Maintenance and Electrical Principles, every installation or service visit is unique and no two ever present the same challenges. This, along with the travel element, makes my role so diverse and interesting and I never stop learning through working with clients from different industries.
“The range of applications where gas detection is required is vast, but without doubt both my and Nathan’s greatest job satisfaction comes from the knowledge that the systems we are installing are protecting the health and lives of so many individuals.”
Ongoing servicing and maintenance of the system is required following installation. Service intervals will depend on the types of sensors installed, but typically a six-monthly check of the system with calibration gases is recommended. A service plan offers best value for money, including emergency call-outs and telephone support in case of emergencies.
Regular servicing also highlights any performance issues with any gas detection system to ensure serviceable parts are replaced at the correct time, meaning that there is minimal downtime to a system. This also enables the supplier to advise of any potential obsolescence of parts, enabling clients to plan financially for updates.
This level of planning and factoring in detailed surveys, site-specific environmental factors and servicing will help to ensure a safe and efficient installation process and maintenance programme for both the customer and the supplier.
Nathan Marks is fixed gas detection business development manager at Shawcity Limited. For more information, visit www.shawcity.co.uk
- Plan ahead for 2021 with Shawcity
- Simplify sound and noise monitoring
- Shawcity's new partnership with Aquaread
- Fit testing systems that are changing the industry
- More instruments…Better Value
- In the spotlight with Neil O’Regan
- Shawcity announces new partnership with Drager
- Fixed point gas detection solutions
- Monitoring VOCs in the workplace
- Shawcity announce new partnership with HAVi