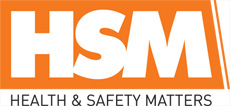
![]() |
Mark Sennett
Managing Editor |
![]() |
Kelly Rose
Editor |
Improving sustainability performance
06 October 2022
Andrzej Palka explores the means to improve PPE sustainability performance, including reducing waste and improving efficiencies in the supply chain, while maintaining the highest levels of PPE performance and worker protection.

ORGANISATIONS AROUND the world are driving towards lower carbon footprints and improved sustainability performance. Almost half of all companies require their suppliers and partners to meet sustainability criteria1, including the procurement of PPE.
The profile of PPE has risen significantly over the last few years due to the COVID-19 pandemic. Workplaces that never previously supplied PPE now had to provide facemasks and other safety equipment. Many of these applications used single-use or disposable safety equipment, resulting in a significant increase in PPE waste.
Several studies during the pandemic highlighted the impact of rising PPE use. The World Health Organization (WHO) estimated that PPE purchased over a 20-month period from March 2020 generated up to 87,000 tonnes of waste worldwide2. In Feb 2021 alone, 3.4 billion single-use facemasks/faceshields were discarded3. The impact is even more severe when this waste leaks into the environment. One university study found that 25,900 tonnes of plastic waste leaked into the ocean from single-use PPE4.
Besides waste, there is also the environmental impact of shipping PPE from manufacturing sites to end users worldwide. Carbon emissions from supply chain activities can be significant. The National Health Service (NHS) in the UK used an estimated 3 billion pieces of PPE over a 7-month period in 2020. An analysis of the supply chain showed that more than 106,000 tonnes of carbon dioxide was emitted during production and transport of these items. The study showed that emissions could have been reduced by 12% if all the production was confined to the UK5.
Fortunately, innovative solutions are helping organisations improve their PPE sustainability performance.
Lowering waste volumes
Instead of single-use PPE, customers could consider multi-use single contamination garments. A simple change in design makes this shift possible. Replacing the self-adhesive tape sealing zippers and chin flaps with Velcro instead allows garments to be reused rather than discarded after use, if there has been no contamination.
While contaminated PPE must be incinerated, non-contaminated single-use garments could be recycled if they are made with recyclable material. Choosing disposable protective garments made from recyclable materials can reduce the volume of PPE waste substantially.
Discarded PPE adds to waste sites, and some contaminated garments must be incinerated as hazardous waste. Materials used for disposable PPE should also be non-ecotoxic so that incineration does not produce hazardous substances.
PPE should be lightweight but durable. Heavier material generates more waste when discarded but some modern fabrics are 20 to 50% lighter than micro-pourous film (MPF) and spunbond –meltblown-spunbond (SMS)alternatives. However, durability must not be compromised. Garments need a high-level of abrasion and tear resistance as torn garments must be discarded immediately.
Packaging is another source of waste. Individually wrapping garments is no longer necessary in some applications. Several single-use garments can be packaged together without any detrimental effects. Providing each garment with its own Instructions for Use is unnecessary for bulk orders. These instructions can be supplied with each box instead.
Packaging also contributes to supply chain emissions due to the extra weight per shipment.
Lowering supply chain emissions
PPE manufacturing is an energy intensive activity. As such energy recovery and reuse can benefit manufacturers by saving costs and reducing emissions. As an example, a Tyvek manufacturing facility in Luxembourg uses waste heat from polyester production to power the plant. Heat recovery reduces the amount of fuel consumed by the plant and therefore reduces emissions from manufacturing.
Manufacturing processes for some materials produce by-products, like hydrochloric acid. These by-products are often treated as waste but could be useful raw materials for other industries. Partnering with nearby facilities may enable PPE manufacturers to eliminate a waste stream by selling the by-product instead. This is exactly what a DuPont manufacturing site in Spain has achieved. Hydrochloric acid produced during DuPont Nomex fibre production is no longer neutralized for disposal. This by-product is now sold as a raw material to a neighbouring metallurgy factory. Eliminating this waste stream saves the DuPont plant the equivalent electricity use of 1,500 homes and the equivalent water use of 350 people.
Long supply routes also contribute to high carbon emissions, but PPE manufacturing facilities are often located at some distance from their markets. This challenge can be overcome by establishing new production sites in strategic locations. For this reason, DuPont is constantly evaluating their manufacturing footprint in specific areas, like Europe. The reduction in PPE weight from using lighter materials and less packaging also has a positive impact on supply chain emissions.
Conclusion
The sustainability performance of PPE is a key concern for companies around the world, as organisations focus on their own emissions as well as those in their supply chain. Manufacturers like DuPont have taken innovative initiatives to reduce their own carbon footprint by smarter packaging of bulk orders, recovering energy during manufacturing, and shortening supply routes. Using recyclable materials and multi-use single contamination garments are also substantially reducing the waste generated from PPE.
Worker protection remains the primary purpose of PPE. New applications like those introduced by the pandemic will continue to demand innovation from manufacturers as they respond to new safety risks. DuPont is continuously developing PPE products that meet the new demands of the industry and reduce the environmental footprint of PPE throughout its lifecycle.
References
Andrzej Palka is Tyvek sustainability leader at DuPont Personal Protection. For more information, visitwww.dupont.com/personal-protection/dpp-sustainability.html
- Garment selector tool
- UK first
- Turning up the heat
- Expert solutions
- Coverall launch
- Next generation
- DuPont launches the new Tyvek Labo coverall at Health and Safety '11 - South, Sandown - to protect the wearer, products and processes
- DuPont leads innovation in the protective coverall market
- Fall protection covered
- Are we ready for a pandemic?