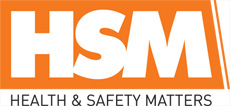
![]() |
Mark Sennett
Managing Editor |
![]() |
Kelly Rose
Editor |
Home> | Plant & Machinery | >General Plant & Machinery | >Identifying preventive maintenance that works |
Identifying preventive maintenance that works
03 September 2024
TORK, FROM hygiene and health company, Essity, explores a tailored approach to optimising hygiene and efficiency.

Preventative maintenance is vital to making sure that all machinery is in good working order as well as to avoiding accidents and costly damage to equipment. Carrying out preventative tasks like cleaning machinery and facilities is already frequent practice in workplaces where equipment failure can lead to a significant loss of income. It is important, however, to recognise that different workplaces require different solutions. To make sure that your maintenance is as efficient and as effective as it can be, it is paramount to consider your facility’s set up and your employees’ needs. A key element of this is making sure that you are using the right products to allow yourself to complete cleaning duties quickly and efficiently.
In manufacturing environments, 9 out of 10 employees believe quality solutions for wiping and cleaning boost productivity and even happiness1 at work. Aside from the actual products themselves, it is important to consider the practicalities of dispenser placement and storage. Poor placement can disrupt operational efficiency and lead to time-consuming movement, wasted inventory, and over-consumption.
A helpful step for any facility is to establish clear operational zones explicitly distinguished by markings to help identify the best place for dispenser installation. This will allow for cleaning supplies to be placed in areas where they are most needed, preventing employees taking more than necessary to avoid extra trips to the dispenser, thus reducing waste. Additionally, by demarcating zones for specific functions and tasks, employees not only have easy access to cleaning and hygiene products but can also reduce the risk of cross-contamination across areas caused by material sharing.
Wherever permanent zoning is not possible or perhaps impractical, mobile dispensers such as the Tork Floor Stand provide an easy solution to ensuring cleaning materials remain easily accessible. These ergonomic Floor Stands save both time and effort with their capacity and ease of movement which allows them to be moved and parked easily where they are needed. Reliably reinforced glass-fibre teeth help to further reduce consumption and waste by allowing workers to take only what they need at the time. When paired with the Tork Heavy-Duty Cleaning Cloth, which works with most solvents and removes oil, grease and dirt whilst protecting hands from heat and metal scraps, the easily accessible floor stands keep downtime to a minimum.
Data and analytics can unlock insights into your operational processes that will help determine the best use of cleaning resources. Tork Vision Cleaning leverages real-time data to pinpoint the timing and locations of service needs within your facility, reducing the need for in-person dispenser checks by 91%2 and saving time on cleaning. This helps you to meet expectations by maximising efficiency allowing your employees to focus on critical tasks affecting the quality of your output and enables an effective, data-driven management of inventory.
Optimising preventive maintenance is a big task, but it is highly beneficial. Tork Workflow simplifies this process by addressing hidden and undiscovered efficiency issues in your facilities. It involves deploying Tork field experts to audit your maintenance and workstation effectiveness. The complimentary 60-minute service, available either virtually or in-person, offers a thorough examination of your facility’s operations and provides recommendations based on the 5S principles (Sort, Set in Order, Shine, Standardise, and Sustain). These insights aim to help you meet your goals, enhance workplace efficiency, and reduce costs. Additionally, the Workflow report includes complimentary recommendations of Tork products tailored to your specific needs.
Products designed to support workers' movements and routines through strategic placement and design can enhance existing processes whilst enhancing hygiene. Tork data-driven tools and expertise assist businesses in developing customised solutions that boost productivity while ensuring employee safety.
References
1 021 Survey conducted by PRS Invivo in March 2021. The survey covered in the US and Germany, with 100 respondents in each market.
2 Based on customer feedback for dispenser checks over 6 months before vs after installing Tork Vision Cleaning (between June-December 2019). Measured across 16 sites connected to Tork Vision Cleaning, with each dispenser check taking approx. 20 seconds.
For more information visit www.tork.co.uk