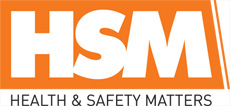
![]() |
Mark Sennett
Managing Editor |
![]() |
Kelly Rose
Editor |
Home> | Slips, Trips & Falls | >Fall Prevention | >Don’t fall short |
Home> | Slips, Trips & Falls | >Fall Protection | >Don’t fall short |
Home> | PPE | >Safety Footwear | >Don’t fall short |
Don’t fall short
17 December 2024
Slips, trips and falls remain the biggest cause of non-fatal injuries at work – Emma Willison explains how to mitigate the risk.

SLIPS, TRIPS and falls are still the most common cause of non-fatal injuries in the workplace, according to the latest annual Health and Safety Executive (HSE)1 statistics.
Accounting for 31 per cent of all non-fatal injuries at work in Britain in 2023/24, slips, trips and falls have now topped the list for more than a decade. This figure does not include falls from height, making the prominence of this type of injury even more concerning.
According to self-reports to the annual Labour Force Survey (LFS), 21 per cent (127,000) of all non-fatal slips, trips and falls resulted in workers requiring over seven days to recuperate from injuries. This absence from the workplace is a costly result of accidents, most of which can be avoided by ensuring the working environment is clear of hazards, and employees are provided with appropriate footwear.
The most common types of injury from this type of accident are musculoskeletal injuries, often caused by the impact of landing on the floor or colliding with objects in the vicinity. These can range in severity, from bruising and soreness to broken bones and spinal injuries.
The most dangerous type of injury is often head trauma, which can result in anything from minor head injuries to serious and potentially life-threatening brain injuries.
Types of hazards
Different industries are exposed to different hazards and often there will be a combination of hazards that employees must be aware of.
The most common types of hazards in the workplace are:
- Spillages of liquids, oils and other slippery substances
- Using incorrect substances when cleaning floors
- Unsuitable, uneven or damaged flooring
- Inappropriate footwear
- Trailing cables and boxes left in open areas
- Adverse weather conditions, such as rain, snow or ice
In an industrial setting such as a manufacturing plant, spills from oils and lubricants used in the machinery can make surfaces slick and hazardous if not cleaned up appropriately. Equally, wires from these machines, if not tidied away properly, can present a tripping hazard where employees may fall to the floor or worse, into the machinery itself. If the flooring in the factory is uneven or slippery when wet and employees have inappropriate footwear without the correct certification, the lack of grip may cause slips to occur.
Adverse weather conditions apply mainly to outdoor workers. For example, construction workers on a site with smooth surfaces, such as temporary plastic flooring or walkways, are at a higher risk of slips when these areas are wet from rain or snow. In these instances, the best way to protect workers is through appropriate footwear that is certified to be slip resistant under relevant BS or EN standards.
Legislation
While there are no specific regulations for safeguarding employees against slips, trips and falls, the general duty of employers to protect employees from harm is directed by the Health and Safety at Work Act 1974 (HSWA). Under the Act, employers must control risks, as far as is reasonably practicable, to prevent harm to workers and anyone affected by their work.
Last year, an update to footwear standard EN ISO 20345 came into effect in the UK, reflecting current working practices within industry and better simulating real-life scenarios. It also allows end users to better select products suited to specific environments. Products in the UK tested under the previous version of the standard will remain compliant until the expiry date of their existing certificate and therefore employers are not required to change footwear that has been already issued with this standard.
The updated standards introduced two new categories of footwear, S6 and S7.
Footwear
When selecting appropriate footwear for employees, companies should perform risk assessments to identify potential slip and trip hazards in the workplace to meet legal requirements. These risk assessments should be reviewed on a regular basis and amended as necessary. In the assessment, hazards are identified, the risks of which are evaluated, and then control measures must be put in place, such as providing appropriate footwear to anyone subject to these hazards.
Slip-resistant shoes are annotated by an SR marking when the footwear passes a slip resistance test conducted on a ceramic tile covered with glycerine. The test ‘SR’ is intended as a generic test for assessing performance on more viscous contaminants, such as oil, meaning this type of footwear will be appropriate for most industrial settings.
On uneven surfaces, trips are a more likely occurrence than slips, so selecting the correct footwear is only the beginning.
Controls
Besides footwear, there are a number of measures that employees can take to minimise the risks associated with slips, trips and falls. These can be as simple as displaying a wet floor sign in an area that has recently been cleaned or appropriate signage to clarify that sections of the floor may be uneven, which is especially prevalent in older buildings.
Cleaning activities are one of the most common causes of slip hazards across industry, as most workplaces require regular cleaning. Robust health and safety procedures around cleaning practices should be implemented to ensure flooring remains as slip-proof as possible. When areas are being cleaned, they should be cordoned off if possible.
The working environment is also often subject to objects and debris in the way of worker activity. Clearing these areas and ensuring any breakages to tiling or carpets are remedied as soon as possible will help prevent trips.
Preparing for adverse weather conditions is best practice for outdoor worksites. Gritting slippery walkways in cold weather will prevent slips and falls on ice and, if possible, covering areas with temporary canopies will stop them from getting wet.
Education
Employees who understand the risks they are likely to be exposed to are at a reduced risk of injury. Being able to identify potential hazards and report them correctly to management will result in employees staying safe and reduces the likelihood of financial penalties incurred by the company. Trained employees are more likely to follow safety practices, report hazards, and keep work areas clear of obstacles.
Additionally, training employees on the types of footwear available to them for the workplace will allow for independent but correct purchasing decisions, leading to fewer injuries from slips. When employees know they’re equipped with the right footwear and training to navigate their environment safely, they experience less concern and are more focused on their tasks.
In response to the concerningly high rate of slips, trips, and falls, which consistently top non-fatal workplace injury statistics, employers have a duty to mitigate these risks by creating safe environments and equipping employees with the necessary tools, such as certified slip-resistant footwear.
Through thorough risk assessments, proactive safety measures, and targeted training, companies can significantly reduce injury rates, minimise productivity losses, and avoid costly penalties. Ensuring that employees understand workplace hazards and have access to the appropriate footwear for specific conditions is essential in promoting a safer, more productive, and legally compliant workplace.
Reference
1 https://www.hse.gov.uk/statistics/assets/docs/hssh2324.pdf
Emma Willison is product and procurement manager at Arco. For more information, visit arco.co.uk/expert-advice