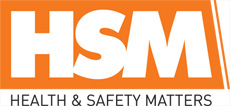
![]() |
Mark Sennett
Managing Editor |
![]() |
Kelly Rose
Editor |
Home> | Breathing Safely | >Dust and Fume Extraction | >Risk exposure |
Home> | Breathing Safely | >Gas Detection and Monitoring | >Risk exposure |
Risk exposure
09 September 2024
TIM TURNEY emphasises the importance of effective airborne hazard monitoring measures set in place and the importance this holds in protecting workers.

AIRBORNE HAZARDS refer to any potentially harmful substances or particles that are suspended in the air. These hazards can come from various sources, including industrial processes, construction activities, natural events like wildfires or volcanic eruptions.
Exposure to harmful substances like welding fumes, dust, and metalworking fluids poses significant risks to workers. These hazards can enter the body through inhalation or direct skin contact. They encompass a range of toxic elements, including metal oxides, volatile organic compounds (VOCs), and various gases, both organic and inorganic. Prolonged exposure to these materials can lead to severe health issues.
Workers exposed to these substances face an increased risk of developing respiratory problems such as silicosis, chronic obstructive pulmonary disease (COPD), and asthma. Additionally, they may experience irritation of the eyes, throat, and skin, along with potential neurological effects. Moreover, there's a heightened risk of developing certain types of cancers. Shockingly, an estimated 13,000 deaths per year in Great Britain alone1 are attributed to past workplace exposure to chemicals and dust.
Scientific research and evidence have significantly enhanced our understanding of the health impacts associated with industrial exposure to these hazardous substances. Leading bodies, including the International Agency for Research on Cancer (IARC), have acted in response. For instance, the IARC has classified mild steel welding fume as a human carcinogen due to its potential link to lung cancer. This classification also extends to Respiratory Crystalline Silica (RCS), a naturally occurring mineral found in materials like sand, stone, concrete, and mortar, which workers may inhale during various tasks such as cutting, drilling, grinding, and polishing.
Dust monitoring
The Health and Safety Executive (HSE)2 refers to Respirable Crystalline Silica (RCS) or silica dust as ‘the biggest risk after asbestos,’ with an estimated 600,000 workers exposed to silica in the UK each year. For the construction industry, RCS is of particular risk as it is found in, stones, bricks and quartz.
When materials are disturbed, broken or otherwise through cutting, drilling, grinding or crushing, minuscule dust particles are created. When inhaled, these particles travel deep into the lungs and can cause incurable and sometimes deadly respiratory diseases such as silicosis, chronic obstructive pulmonary disease and kidney disease. As a result, the UK Workplace Exposure Limit (WEL) for RCS is 0.1mg/m3 (milligrams per-metre cubed) is restricted to a period of eight hours.
Control measures
In controlling Airborne Hazards, the usual risk control hierarchy applies. Where the risk cannot be eliminated entirely, a safer form of the product should be used. As this is not always feasible, the process should be changed to emit less dust or enclose the process so that the dust does not escape or by extracting the dust near the source using local exhaust ventilation (LEV).
Employers should make the process efficient enough to have as few workers in harm’s way as possible. In the hierarchy of control, the last thing you apply is respiratory protection equipment (RPE), and often, because of a lack of understanding of toxicity and dust concentration, the wrong respiratory protection is used.
To better understand employee exposure, a correctly executed programme of air monitoring of individual employees using personal sampling pumps needs to be implemented. Air monitoring can quantify exposure levels and ensure workers are not significantly exposed. When control measures are in place, monitoring can ensure they are working, and if RPE is used it can check the correct type and measure residual risk. These pumps are essential in places where there is a significant risk of highly concentrated hazardous pollutants in the surrounding air, for example during demolitions.
To obtain an accurate picture, it is important that the pumps are used with the correct sampling head, and in the case of RCS, a cyclone and filter which collects the particulate should be used. Once the sample is analysed by a laboratory, the level of exposure can be calculated. If the result of this assessment shows significant exposure risk, then action should be taken immediately to improve control measures and ensure exposure is reduced. Note that it’s not good enough to just keep exposure to at or just below the exposure limit of 0.1mg/m3, exposure should be reduced to as low as possible.
Many improvements have been made to personal sampling pumps over time. Battery technology, back pressure capability, accurate flow control, minimised pulsation, data download and the ability to be intrinsically safe have all been improved, ensuring measurement of an individual’s exposure to harmful substances is as accurate as possible. Understanding these factors in which the personal sampling pump needs to operate effectively will allow employers to choose the most effective device suited to their working environment.
Correct implementation of personal sampling relies on a thorough understanding of practice, procedure, how sampling pumps function and the use of the correct sampling head and filters.
Correct equipment, calibrated properly
Personal sampling pumps must adhere to the standard ISO 13137:2022. The standard sets limits for required flow stability and maximum permissible pulsation levels, enabling users of personal air sampling pumps to adopt a consistent approach for flow rate assessment.
This standard provides a comprehensive framework that specifies test methods to determine the performance of air sampling pumps and ensures that environmental influences such as air pressure and temperature have a minimal impact on the accuracy of the sampled air for accurate results.
Correct equipment, calibrated properly and an awareness of the limitations and impact on data collection that the equipment itself can have, should be at the forefront of correct air monitoring procedures as well.
Pumps, including the Apex2, that operate with a pulsation value of less than 11 per cent and conform to all relevant ISO standards give occupational hygienists and site managers the peace of mind that data captured is reliable and unaffected by pump pulsation. Low pulsation is particularly important when sampling for RCS as the sampling head is a cyclone, and only at low pulsation levels will it get the correct ‘respirable’ sample.
References
1 Health & Safety at Work, Health & Safety Executive 2023
2 https://www.hse.gov.uk/pubns/indg463.pdf
Tim Turney is global marketing manager at Casella. For more information, visit www.casellasolutions.com
- Monitor and measure noise exposure
- Get connected at conference
- Sound level meter upgrade
- Measuring wood dust exposure
- Casella announces acquisition by TSI Instruments
- Dust sampling pump range from Casella
- New human vibration meter
- Expose the hidden danger
- Casella noise course on 6th February 2018 – improve your risk assessment skills
- Monitoring boundaries