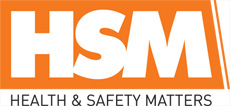
![]() |
Mark Sennett
Managing Editor |
![]() |
Kelly Rose
Editor |
Watch your head
29 July 2013
There are many reasons to wear a helmet, and an ever diminishing number of reasons not to. At the 2013 A+A, the world-wide leading trade fair for personal protective wear and health at work (5 - 8 November), many exhibitors will be demonstrating how helmets can be a comfortable and effective means of protection.
Latest statistics show that users are clearly becoming more willing to accept this. The number of head injuries in the workplace is declining. The Trade Association for the Construction Industry recorded around 11,000 accidents in this category in 2011. This amounts to 10 percent of all accidents.
"That is still too many for us”, said Dr. Claudia Waldinger, director of the departmental section for personal protection equipment (PPE) at the BG Bau (Trade Association for the Construction Industry) in Berlin.
"We will never give up and are going to keep at it," is the prevailing maxim. Therefore, the prevention service of the BG Bau examines construction sites regularly in order to assess if the protective helmets worn are truly satisfactory. We have a three-tiered model in mind as is the case concerning safety footwear - starting at helmets for mountaineers ranging to the industrial safety helmet all the way to the heavy-duty industry safety helmets," said Waldinger. Which helmet is necessary must be determined by means of a hazard assessment. Foundations for the selection and use of helmets are regulated by BGR 193 "Use of Head Protection” (BGR = Trade Association Regulation).
The requirements for heavy-duty industrial safety helmets have been defined since 2006 in DIN EN 14052. It should contribute to improved protection whilst carrying out industrial activities which pose an above-average risk of injury to the head. It does not replace DIN EN 397, in which the requirements for frequently used industry safety helmets are defined. DIN EN 14052 should rather take over where conventional helmets reach their limits of performance.
Popular "bump caps"
For many activities, a so-called "bump cap" is already considered to be sufficient. What seems to sound a bit conceptually stilted has been determined as light head protection with regards to the requirements in the European norm EN 812. Put more simply: In the field of helmets, "bump caps” practically fill the holes between the areas for which the legislative authority does not prescribe safety helmets, although a certain protection is indeed deemed sensible. For example, this applies to unloading luggage at airports or certain warehouse activities, as well as automotive body construction. "Bump caps actually derive from the felt caps that were once worn in earlier days whilst working in tight spaces," said Manfred Schuster, responsible for head protection at UVEX, a safety apparel specialist located in Fürth. "People like bump caps. They look like baseball caps, are light with an invisible shell made of plastic and are individually adjustable depending on head size." The cotton material used is regularly certified according to Ökotex 100 standards. Bump caps can be made in all colours and, if ordered in certain quantities, can be tailored to the corporate design of a company. The UVEX bump caps are, by the way, also closed in the back, which increases protection.
The most frequently used helmet
For most operating conditions on a building site, in the processing or production industries, industrial safety helmets are the right choice. This is the type of head protection that is most frequently used in the working world. They have to comply with basic requirements with regards to shock absorption, penetration resistance and flammability of the helmet shell material. But the hazard assessment is the basis for the applied use of a industrial safety helmet. Is especially high lateral stability more important or electrically isolating characteristics? Or will the helmet be used in especially hot environments?
For industrial activities with an above-average risk of injury to the head, heavy-duty industrial safety helmets are recommended. For these helmets, the DIN EN 14052 for heavy-duty industrial safety helmets exists, which places increased requirements on helmets with regards to shock absorption properties and penetration resistance. In it, an essential reform to DIN EN 397 has been made. Namely, if these characteristics were only measured in the crown area for DIN EN 397, DIN EN 14052 would also require their testing in the event of lateral impact. The DIN EN 14052 requirements on mechanical firmness in the presence of radiant heat are optional.
Go far with helmets for mountaineers
Despite all of the "multi-talent" characteristics, industrial safety helmets have their limits in certain situations as Christoph Krah from Krah GmbH reports. The company distributes Petzl helmets in Germany (A+A distributor). "If the wearer is working at great heights, these helmets can become a hazard - for those standing below. Think about the helmet falling off if it is not equipped with a chinstrap," explains Christoph Krah. Also, due to the danger of the wearer falling, a normal industrial safety helmet is not sufficient for working at great heights. Because here, optimal protection for head impact is required if worst comes to worst.
"Helmets for mountaineers" are available (norm for climbing helmets is DIN EN 12492). They are generally built very light, well ventilated and are also used (other than the name insinuates) in the working world. They protect from collision, falling objects and from impact. The helmet "Vertex Best" from Petzl is such a helmet. It is very compact, closed all around, protects from hits and collision according to EN 397 and DIN EN 12492 and suffices for electric insulation according to EN 391 and EN 50365. In addition, it provides protection from the spattering of molten metal, lateral deformation and usage in cold environments according to EN 397. The "Vertex Vent” is even lighter. Its 6-point mesh liner ensures an optimal fit and wear comfort. Collisions and hits are absorbed by the deformation of the inner shell. The so-called "CenterFit adjustment system" ensures that the Petzl helmet sits firmly on the middle of the head. The ventilation holes can be regulated by means of sliding shutters. While sport helmets have as many openings as possible for ventilation, the norm for industrial safety helmets provides for a ventilation area of 400 square millimetres.
The design - from the weatherstrip all the way to ventilation
In principle, the helmet shell of safety helmets for the working world are formed in various ways, for example with a wide circumferential edge with a weatherstrip, visor or adjustable neckpiece. Depending on the design, it has ventilation openings and pockets or adaptor systems to attach accessories such as hearing protection or visors. The "Airwing B” for example by UVEX with three variable ventilation openings in the forehead area and back of the head was designed for the construction industry. The openings enable a ventilation dependent upon the weather. This industrial safety helmet is also available with a shortened visor for expanded upward field of view. The "Airwing C” provides for constant ventilation at the area at the back of the head and is closed at the forehead area. This type of helmet is ideal for the pharmaceutical and chemical industry due to the splash guard. The "Airwing E” design offers a completely covered helmet shell and can therefore be used by electricians. In addition to the basic requirements, this helmet fulfils additional "electrical insulation” requirements according to DIN EN 397 and is suitable for very low temperatures down to -30 °C.
Various temperatures - various materials
If people are subjected to high levels of heat or special chemical influences at work, the shell material must be correspondingly durable and cannot be flammable. For this, so-called thermosetting plastic such as phenol formaldehyde resin are suitable. They are particularly dimensionally stable, heat resistant, chemical resistant and have good antistatic capabilities, as well as a high durability. Therefore, they are mainly used in the mining industry, in the chemical industry and for working in hot environments.
Helmets made of thermoplastics such as polyethylene or polycarbonate can be used at normal working conditions, although they deform very quickly when subjected to heat. Its tensile strength at cold temperatures is quite good. Polyethylene can endure temperatures as low as –40 °C. In comparison to helmets made of thermosetting plastics, the production costs for industrial safety helmets made of thermoplastics is quite low.
Inner values - outer appearance
For whatever activities a helmet is required for, it is worn with pleasure above all if the inner values and the appearance are in order. Therefore, the interior should provide for a perfect fit - both in regard to size as well as wearing height. This is achieved by means of an internal head liner which is made up of four or six bands. Ideally, the height of the helmet can be adjusted to various heights at the front and the back. The wearing height can in turn be regulated by making adjustments to the internal head liner. The head size can be adjusted by means of a rotary knob.
Helmets for working at great heights and rescue operations are preferred to be equipped with a 6-point internal liner for the chinstrap in order to achieve a good fit and a high level of wear comfort.
The weight of the helmet is especially relevant to the wear comfort of the helmet. Light helmets only weigh around 350 grammes and are therefore hardly noticeable on the head.
To ensure that the helmet is acceptable to the wearer, in addition to the aspects of comfort, the design and colour has key significance. "In earlier days, helmets were distinctive markers in the field of construction - white for the construction workers, yellow for the foreman and red for the site manager. Today, any company can have helmets produced with their own corporate design and desired colour,” Dr. Claudia Waldinger highlights in regards to the significance of "outer values".
Suitable accessories
As versatile safety helmets are in reference to their characteristics, the range of accessories is just as versatile. Each professional visitor making a round through the fair halls at the 2013 A+A will be assured of this.
For many work activities, a visor or a complete face protection is required for instance. It this way, pockets or systems are generally attachable by means of an adaptor. This also applies to hearing and eye protection. There are helmets like the "Protector Style 600" from the British company Scott that are specially designed to be compatible with other elements such as a hearing protecting earmuffs, eye protection, visors, respiratory protection or lamps. Other accessories include sweatbands and chinstraps furnished in various manners (leather, as a fork chinstrap, or with a chin pad). UVEX even offers a smart pen holder for helmets. In the winter, warm caps can be worn under the helmet. On the other hand, paper caps serve for hygiene.
Identification markings, durability, inspection
A+A visitors (2011 A+A had more than 60,000 visitors) are exclusively interested in quality goods as "professionals in the field" and know what to look for in terms of identification markings and durability of safety articles.
According to the norm, the helmet shell and the interior have to be marked in a permanent and visible manner. Next, the European norm has to be indicated. In the case of helmets belonging to category III according to EU guideline 89/686/EWG, also the testing institute must be specified (Basis of inspection for industrial safety helmets is DIN EN 397). The name of the manufacturer and the helmet type follow. The size of the helmet can be taken from the information moulded or embossed into the helmet. At the helmet specialist Voss from Hanover, there are helmets ranging from 51 - 64 cm, the caps from 50 to 63 cm. Furthermore, the production period must be indicated (quarter or year). Depending on the weather, the UV radiation and mechanical stress they are subjected to, helmets age quite differently. A helmet made of thermosetting plastics has a product life of eight years. A helmet made of thermoplastics must be replaced after four years. Ultimately, there is an instruction label and additional marking for temperature resistance, electrical insulation, lateral deformation, splash protection from molten metal, resistance against radiant heat for DIN EN 14052 as well as VDE approval.