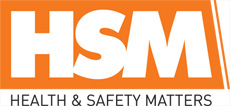
![]() |
Mark Sennett
Managing Editor |
![]() |
Kelly Rose
Editor |
Home> | Industry Update | >Company News | >Be on guard about guards |
ARTICLE
Be on guard about guards
23 January 2013
Changes relating to guarding that have been introduced
by the new Machinery Safety Directive,may mean many
machine manufacturers and users are breaking health &
safety laws without even realizing.Gary Trewhitt explains
Changes relating to guarding that have been introduced by the new Machinery Safety Directive,may mean many machine manufacturers and users are breaking health & safety laws without even realizing.Gary Trewhitt explains
While it is true that an objective of machine designers is always to eliminate hazards, there are very many cases where this is not possible. In such cases, measures have to be put in place to mitigate the hazards and, in the case of mechanical hazards in particular, those measures often take the form of guards.
Given their essential safety role, guards are often treated surprisingly casually, but anyone who is in doubt about their importance should visit the Health and Safety Executive website ww.hse.gov.uk where even the most cursory of searches will reveal a whole catalogue of injuries and accidents that could have been prevented had appropriate and fit-forpurpose guards been in use.
With this in mind, it's not surprising that current safety legislation, as we shall see later, gives a lot of attention to guards.
This has not always been the case, however. In fact, until comparatively recently, a common approach to guarding was simply to knock out a quick design that looked as though it was adequate for the job in hand, and then have it fabricated by a local engineering company or metal basher.
This approach was, in reality, never satisfactory and there can be no doubt that it would be virtually impossible to demonstrate that a guard produced in this way was compliant with current safety legislation. And, let's not beat about the bush, if a machine that is not properly guarded causes injury or death, then prosecutions and stiff penalties - even jail terms - are likely to follow.
While it might be easy for machine manufacturers and most machine users to feel comfortable that none of their equipment is fitted with such casually designed and fabricated guards, there will be many that find their comfort evaporates when they are reminded that the new Machinery Safety Directive, 2006/42/EC, which came into force at the end of 2009, introduced a whole range of new requirements for guards, not the least of which is that they must carry CE marking.
Let's just pause for a moment to consider what that means. CE marking can only legally be applied to a product if that product complies with all relevant EU Directives. These directives are implemented in the form of regulations in EU member states, and the regulations are supported by standards. In simple terms, applying the CE marking to a product confirms that the product complies with all applicable standards.
This is, to be fair, not quite the whole story, but alternative routes to CE marking without full standards compliance are even more complicated and costly than the standards-based route.
Now let's return to guards. There are a lot of standards that apply to guards. Just a few examples are EN 953, Safety of Machinery - Guards - General Requirements; EN ISO 13857 - Safety of Machinery - Safety distances to prevent hazard zones being reached by upper and lower limbs; and EN 349 - Safety of Machinery - Minimum gaps to avoid crushing of parts of the human body.
There are many others, including a whole raft of "Type C" standards that apply specifically to particular types of machine.
Clearly, achieving full standards compliance for a guard, which is necessary if it is to carry the CE marking, is no trivial task. And it's certainly not a task that can be readily tackled with an ad-hoc design and the services of the nearest local engineering company. CE marking, along with the design and manufacture of guards, now requires specialist expertise.
This need for expertise is further reinforced when the other changes to guarding requirements brought in by the new Machinery Safety Directive are considered. Section 1.4.1 of the Essential Health and Safety Requirements (ESHRs) that form part of this directive now requires that guards must protect against the ejection of falling materials and objects.
Section 1.4.2.1 has added requirements that for fixed guards, the fixing systems must remain attached to the guards when removed, and also that, where possible, guards must be incapable of remaining in position without their fixings.
In some cases these new requirements may be easy to satisfy, but in many they will not, and in every case a considerable level of expertise will be needed to ensure that guards satisfy all regulatory requirements.
There is, of course, no reason why companies should not develop and maintain the necessary expertise relating to guarding in house, but often limited resources and budgets make this impractical.
In these cases, specialist guarding design, assessment and manufacturing services, of the type offered by Safety Systems Technology, offer a convenient, affordable and dependable solution. The scope of the services offered varies from supplier to supplier, but the best suppliers can specify, design, manufacture and install a full range of machine guarding to suit all applications, as well as providing reliable advice on technical issues and assistance with meeting the relevant regulations.
In summary, it pays to be on guard about guards - they perform an indispensable life-protecting function and, from the point of view of minimising the risk of injury as well as meeting the multitude of regulatory requirements, only the best is good enough. Fortunately, with the aid of an expert guarding supplier, achieving the best need not be complicated or costly.
Gary Trewhitt works for Safety Systems Technology. Stand 184 (Part of Laidler Associates).
While it is true that an objective of machine designers is always to eliminate hazards, there are very many cases where this is not possible. In such cases, measures have to be put in place to mitigate the hazards and, in the case of mechanical hazards in particular, those measures often take the form of guards.
Given their essential safety role, guards are often treated surprisingly casually, but anyone who is in doubt about their importance should visit the Health and Safety Executive website ww.hse.gov.uk where even the most cursory of searches will reveal a whole catalogue of injuries and accidents that could have been prevented had appropriate and fit-forpurpose guards been in use.
With this in mind, it's not surprising that current safety legislation, as we shall see later, gives a lot of attention to guards.
This has not always been the case, however. In fact, until comparatively recently, a common approach to guarding was simply to knock out a quick design that looked as though it was adequate for the job in hand, and then have it fabricated by a local engineering company or metal basher.
This approach was, in reality, never satisfactory and there can be no doubt that it would be virtually impossible to demonstrate that a guard produced in this way was compliant with current safety legislation. And, let's not beat about the bush, if a machine that is not properly guarded causes injury or death, then prosecutions and stiff penalties - even jail terms - are likely to follow.
While it might be easy for machine manufacturers and most machine users to feel comfortable that none of their equipment is fitted with such casually designed and fabricated guards, there will be many that find their comfort evaporates when they are reminded that the new Machinery Safety Directive, 2006/42/EC, which came into force at the end of 2009, introduced a whole range of new requirements for guards, not the least of which is that they must carry CE marking.
Let's just pause for a moment to consider what that means. CE marking can only legally be applied to a product if that product complies with all relevant EU Directives. These directives are implemented in the form of regulations in EU member states, and the regulations are supported by standards. In simple terms, applying the CE marking to a product confirms that the product complies with all applicable standards.
This is, to be fair, not quite the whole story, but alternative routes to CE marking without full standards compliance are even more complicated and costly than the standards-based route.
Now let's return to guards. There are a lot of standards that apply to guards. Just a few examples are EN 953, Safety of Machinery - Guards - General Requirements; EN ISO 13857 - Safety of Machinery - Safety distances to prevent hazard zones being reached by upper and lower limbs; and EN 349 - Safety of Machinery - Minimum gaps to avoid crushing of parts of the human body.
There are many others, including a whole raft of "Type C" standards that apply specifically to particular types of machine.
Clearly, achieving full standards compliance for a guard, which is necessary if it is to carry the CE marking, is no trivial task. And it's certainly not a task that can be readily tackled with an ad-hoc design and the services of the nearest local engineering company. CE marking, along with the design and manufacture of guards, now requires specialist expertise.
This need for expertise is further reinforced when the other changes to guarding requirements brought in by the new Machinery Safety Directive are considered. Section 1.4.1 of the Essential Health and Safety Requirements (ESHRs) that form part of this directive now requires that guards must protect against the ejection of falling materials and objects.
Section 1.4.2.1 has added requirements that for fixed guards, the fixing systems must remain attached to the guards when removed, and also that, where possible, guards must be incapable of remaining in position without their fixings.
In some cases these new requirements may be easy to satisfy, but in many they will not, and in every case a considerable level of expertise will be needed to ensure that guards satisfy all regulatory requirements.
There is, of course, no reason why companies should not develop and maintain the necessary expertise relating to guarding in house, but often limited resources and budgets make this impractical.
In these cases, specialist guarding design, assessment and manufacturing services, of the type offered by Safety Systems Technology, offer a convenient, affordable and dependable solution. The scope of the services offered varies from supplier to supplier, but the best suppliers can specify, design, manufacture and install a full range of machine guarding to suit all applications, as well as providing reliable advice on technical issues and assistance with meeting the relevant regulations.
In summary, it pays to be on guard about guards - they perform an indispensable life-protecting function and, from the point of view of minimising the risk of injury as well as meeting the multitude of regulatory requirements, only the best is good enough. Fortunately, with the aid of an expert guarding supplier, achieving the best need not be complicated or costly.
Gary Trewhitt works for Safety Systems Technology. Stand 184 (Part of Laidler Associates).
MORE FROM THIS COMPANY
- Risk assessment software launch
- Machine safety mark
- Certification service
- Plant & Machinery Safety Zone debuts at Health & Safety '10 North
- Machinery safety training dates
- Extinguishing danger
- Introduction to Machinery Safety training course
- Machinery safety support
- Machinery safety guide
- Electromagnetic machinery safety service
OTHER ARTICLES IN THIS SECTION