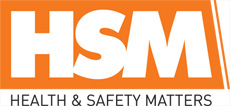
![]() |
Mark Sennett
Managing Editor |
![]() |
Kelly Rose
Editor |
ARTICLE
Blower-powered dryer helps accelerate manufacture of high performance transmissions
23 January 2013

High-performance transmission manufacturer, XTRAC, employs ACI blower-powered JetBlack as part of new enhanced manufacturing processes that ensure H&S compliance and helps boost manufacturing procedures. The new procedures are based upon the introduction of VCI bag technology and the adoption an aqueous-based detergent with a rust inhibitor additive to replace the use of a heavy oil-based corrosion preventative.
Previously, when machined components were progressing through manufacture they were coated in a heavy, oil-based corrosion preventative, which had to be removed and reapplied after each operation. This rust inhibitor was sticky, messy to handle, time consuming to remove and presented H&S concerns.
To eliminate these issues, XTRAC introduced VCI bag technology along with an aqueous-based detergent that has a rust inhibitor additive which replaces the original heavy coating substance. Once applied, this new rust inhibitor leaves only a thin protective film that permits the work piece to be worked without being removed.
The cleaning and application operations involved with the original heavy rust inhibitor took about 25 minutes to complete. With each component passing through an average of ten stages involving rust inhibitor application and removal some 200 minutes can be saved during the manufacturing process.
Helping to accelerate throughput is a drying system that removes all moisture from the washed components. This is a specially adapted blower-powered 'JetBlack' from ACI. It delivers a high volume of clean, filtered air at low pressure which provides rapid effective drying with no dangers to the operative, unlike compressed air.
Previously, when machined components were progressing through manufacture they were coated in a heavy, oil-based corrosion preventative, which had to be removed and reapplied after each operation. This rust inhibitor was sticky, messy to handle, time consuming to remove and presented H&S concerns.
To eliminate these issues, XTRAC introduced VCI bag technology along with an aqueous-based detergent that has a rust inhibitor additive which replaces the original heavy coating substance. Once applied, this new rust inhibitor leaves only a thin protective film that permits the work piece to be worked without being removed.
The cleaning and application operations involved with the original heavy rust inhibitor took about 25 minutes to complete. With each component passing through an average of ten stages involving rust inhibitor application and removal some 200 minutes can be saved during the manufacturing process.
Helping to accelerate throughput is a drying system that removes all moisture from the washed components. This is a specially adapted blower-powered 'JetBlack' from ACI. It delivers a high volume of clean, filtered air at low pressure which provides rapid effective drying with no dangers to the operative, unlike compressed air.
MORE FROM THIS COMPANY
- Personnel-cleaning booth
- Air Control Industries joins Made In Britain
- New website
- New personnel de-dusting booth "blows and sucks" for greater efficiency
- Online industrial fan selector
- Dust in the wind
- New personnel de-dusting booth 'blows and sucks' for greater efficiency
- Safe and efficient de-dusting of personnel and equipment
- Small but powerful
- Personnel cleaning booth
RELATED ARTICLES
- No related articles listed
OTHER ARTICLES IN THIS SECTION