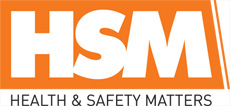
![]() |
Mark Sennett
Managing Editor |
![]() |
Kelly Rose
Editor |
Home> | Industry Update | >Company News | >A bone aching problem: Tackling MSDs in the workplace |
ARTICLE
A bone aching problem: Tackling MSDs in the workplace
23 January 2013
Last year an estimated 538,000 UK workers believe they suffered from a musculoskeletal disorder that was caused or made worse by their work; the BSIF highlights the importance of considering MSDs when carrying out a workplace

Last year an estimated 538,000 UK workers believe they suffered from a musculoskeletal disorder that was caused or made worse by their work; the BSIF highlights the importance of considering MSDs when carrying out a workplace risk assessment
In 2008/09, according to the Labour Force Survey, an estimated 538,000 people in Great Britain who had worked in the last year, believed they were suffering from a musculoskeletal disorder that was caused or made worse by their current or past work. This equates to 1.8 per cent of those who worked in the UK in the last 12 months and of these, over half were suffering from a new work-related musculoskeletal disorder. The figures alone show what a significant problem this is and one that every employer needs to be aware of to ensure they are protecting their staff to the best of their ability.
Musculoskeletal disorders (MSDs) vary greatly affecting muscles, joints, tendons and other parts of the body causing problems such as lower back pain, joint injuries and repetitive strain injuries. They are the most common occupational illness in the UK and risk factors causing MSDs can be found in virtually every workplace. Injury can happen while doing any activity that involves some movement of the body, from heavy lifting to typing; consequently workers in almost every sort of job are at some risk.
It is therefore essential to consider MSDs when carrying out a workplace risk assessment. A variety of tasks and factors can increase the risk of musculoskeletal injuries, including repetitive and heavy lifting, bending and twisting, repeating an action too frequently, an uncomfortable working position, adverse working environment (e.g. hot, cold) etc. An estimated 11.6 million working days a year are lost to work-related MSDs and the Labour Force Survey shows that an estimated 9.3 million working days (full-day equivalent) were lost in 2008/09 through MSDs caused or made worse by work. By ignoring these risks, not only will employers be disregarding their duty under the Health & Safety Offences Act 2008, but the possible consequence of lost working days will also potentially harm their business.
This is significant to all businesses but will have added impact on the SME market.
While in most cases, employers seek to eliminate risks identified through a comprehensive assessment, by changing working procedures and environment, this is not always possible as the cause of MSDs is so varied. There is, however, a variety of precautionary measures an employer can take to reduce the risk.
These can depend upon the sort of work employees carry out and what it is 'reasonably practical' for your company to do. The first step is to assess all the MSD risks the tasks generate. Then, try to eliminate as many of them as possible, by, for example, redesigning the tasks, providing mechanical aids or changing desk layout. This has now been made easier following the launch of a new online Assessment of Repetitive Tasks (ART) tool.
Developed by the Health and Safety Executive (HSE) and Health and Safety Laboratory (HSL), ART can help identify where significant risks lie and suggest where to focus risk reduction measures to reduce the likelihood of employees suffering from MSDs of the upper limbs associated with repetitive tasks.
Some jobs will have risks which will be unavoidable such as manual handling. However with practical advice, training and deployment of a handling aid e.g. a pallet truck, electric or hand powered hoist, or a conveyor, the risk will be minimised. Where a mechanical aid or safety equipment is needed it is important to ensure that it is suitable for the job and also conforms to standards if necessary. If uncertain, advice can be sought from the British Safety Industry Federation (BSIF) who, with its core purpose to support and represent suppliers, acts as a valuable information source, providing direction in all health and safety matters.
Most personal protective equipment (PPE) will need to conform to the requirements of the PPE Directive. However with other [non-personal] safety equipment the laws are different and vary. In some cases the products will need to comply with specific regulations and in other instances no regulations exist.
Whether they do or do not, the Health and Safety at Work Act will apply in the same way as it does regarding the selection, deployment and use of all safety equipment.
By working with a member of the BSIF, purchasers can be assured that they are using a reputable supplier who is committed to issuing genuine and suitable products and offering trustworthy advice.
Statistics gathered through the Labour Force Survey suggest that the overall incidence rate of self-reported work-related MSDs has fallen over the period 2001/02 to 2008/09.
However as the most common occupational injury, the BSIF would like to see the number of MSDs continue to fall and encourages employers to seek out advice and use the tools available to ensure risks leading to these are minimised.
For further advice on any of the issue contained within this article or to search for a Registered Safety Supplier, visit www.bsif.co.uk. The ART tool is available online at www.hse.gov.uk/msd/uld/art.
In 2008/09, according to the Labour Force Survey, an estimated 538,000 people in Great Britain who had worked in the last year, believed they were suffering from a musculoskeletal disorder that was caused or made worse by their current or past work. This equates to 1.8 per cent of those who worked in the UK in the last 12 months and of these, over half were suffering from a new work-related musculoskeletal disorder. The figures alone show what a significant problem this is and one that every employer needs to be aware of to ensure they are protecting their staff to the best of their ability.
Musculoskeletal disorders (MSDs) vary greatly affecting muscles, joints, tendons and other parts of the body causing problems such as lower back pain, joint injuries and repetitive strain injuries. They are the most common occupational illness in the UK and risk factors causing MSDs can be found in virtually every workplace. Injury can happen while doing any activity that involves some movement of the body, from heavy lifting to typing; consequently workers in almost every sort of job are at some risk.
It is therefore essential to consider MSDs when carrying out a workplace risk assessment. A variety of tasks and factors can increase the risk of musculoskeletal injuries, including repetitive and heavy lifting, bending and twisting, repeating an action too frequently, an uncomfortable working position, adverse working environment (e.g. hot, cold) etc. An estimated 11.6 million working days a year are lost to work-related MSDs and the Labour Force Survey shows that an estimated 9.3 million working days (full-day equivalent) were lost in 2008/09 through MSDs caused or made worse by work. By ignoring these risks, not only will employers be disregarding their duty under the Health & Safety Offences Act 2008, but the possible consequence of lost working days will also potentially harm their business.
This is significant to all businesses but will have added impact on the SME market.
While in most cases, employers seek to eliminate risks identified through a comprehensive assessment, by changing working procedures and environment, this is not always possible as the cause of MSDs is so varied. There is, however, a variety of precautionary measures an employer can take to reduce the risk.
These can depend upon the sort of work employees carry out and what it is 'reasonably practical' for your company to do. The first step is to assess all the MSD risks the tasks generate. Then, try to eliminate as many of them as possible, by, for example, redesigning the tasks, providing mechanical aids or changing desk layout. This has now been made easier following the launch of a new online Assessment of Repetitive Tasks (ART) tool.
Developed by the Health and Safety Executive (HSE) and Health and Safety Laboratory (HSL), ART can help identify where significant risks lie and suggest where to focus risk reduction measures to reduce the likelihood of employees suffering from MSDs of the upper limbs associated with repetitive tasks.
Some jobs will have risks which will be unavoidable such as manual handling. However with practical advice, training and deployment of a handling aid e.g. a pallet truck, electric or hand powered hoist, or a conveyor, the risk will be minimised. Where a mechanical aid or safety equipment is needed it is important to ensure that it is suitable for the job and also conforms to standards if necessary. If uncertain, advice can be sought from the British Safety Industry Federation (BSIF) who, with its core purpose to support and represent suppliers, acts as a valuable information source, providing direction in all health and safety matters.
Most personal protective equipment (PPE) will need to conform to the requirements of the PPE Directive. However with other [non-personal] safety equipment the laws are different and vary. In some cases the products will need to comply with specific regulations and in other instances no regulations exist.
Whether they do or do not, the Health and Safety at Work Act will apply in the same way as it does regarding the selection, deployment and use of all safety equipment.
By working with a member of the BSIF, purchasers can be assured that they are using a reputable supplier who is committed to issuing genuine and suitable products and offering trustworthy advice.
Statistics gathered through the Labour Force Survey suggest that the overall incidence rate of self-reported work-related MSDs has fallen over the period 2001/02 to 2008/09.
However as the most common occupational injury, the BSIF would like to see the number of MSDs continue to fall and encourages employers to seek out advice and use the tools available to ensure risks leading to these are minimised.
For further advice on any of the issue contained within this article or to search for a Registered Safety Supplier, visit www.bsif.co.uk. The ART tool is available online at www.hse.gov.uk/msd/uld/art.
MORE FROM THIS COMPANY
- In the spotlight with John Gill
- The difficulties of deciding which safety equipment is 'suitable' for you
- BSIF Awards 2020
- What's current
- Respiratory Protection - have you selected the right product?
- BSIF and sustainability
- We are the champions
- Awarding excellence
- Diversity in PPE
- And the winners are...
OTHER ARTICLES IN THIS SECTION