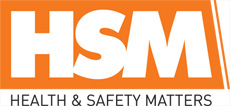
![]() |
Mark Sennett
Managing Editor |
![]() |
Kelly Rose
Editor |
Home> | Plant & Machinery | >Electrical Safety | >Test for danger |
Test for danger
22 July 2024
Businesses have a duty to keep workers and the buildings they work in safe. Steve Dunning looks at the test equipment that can be used to ensure compliance with safety regulations and improve workplace conditions.

KEEPING EMPLOYEES safety at the forefront is essential for any business, and one effective way to ensure this is through the regular use of electrical test equipment. By consistently using electrical test equipment, businesses can proactively detect and address potential risks, greatly reducing the likelihood of accidents and fostering a safer, more productive workplace. This proactive approach not only meets health and safety regulations but also demonstrates a company’s commitment to its employees' wellbeing.
Tools can be roughly split into two categories, Firstly, tools used to check the safety of the working environment such as portable appliance testers, vital for assessing the condition and safety of electrical appliances, and other devices such as sound and light meters for monitoring critical environmental factors. Secondly tools used to keep qualified employees or contractors safe when working with electricity, which is also the responsibility of the employer.
Portable appliance testers
Portable appliance testing (PAT) refers to the process of checking electrical appliances and equipment to confirm they are safe to use. Although not mandatory (the Electricity at Work Regulations 1989 simply state that electrical equipment with the potential to cause injury must be kept in a safe condition), PAT is critical given that almost a quarter of all reportable electrical accidents involve portable appliances. Ensuring these appliances are fault-free is vital, as oversight, especially by inadequately trained individuals, can result in severe consequences.
Portable appliances include any items that connect to power through a flexible cable, plug and socket. This means any appliance that can be plugged into a wall socket or generator should undergo PAT and encompasses not just appliances that are easily moved but also those secured for safety purposes, such as kettles, hairdryers and hand dryers found, for example, in hotels.
When selecting testing equipment, it is advisable to choose units that are compact and lightweight to ensure they are easy to transport. Devices with a backlit display are usually preferable as they can be easily used in a variety of different environments. Additionally, features such as one-button operation and clear on-screen guides make the testing process more simple while devices that provide straightforward pass or fail results directly on the screen make record-keeping more efficient.
Socket testers
A socket tester serves as a good initial tool for potentially highlighting unsafe electrical sockets and wiring faults and when used correctly, provides a quick and efficient means of assessing safety.
There are a wide variety of socket testers to choose from which can make it challenging to select the most appropriate one. While all socket testers will confirm that fundamental connections like earth, live and neutral are correctly established, those classified as advanced or professional also help verify the quality of the earth. The results from these tests are typically shown through LEDs that light up in different patterns to alert the user to the current state of the socket in terms of alternating current (AC) and voltage. In some models, an audible buzzer might also be used to indicate the status.
While invaluable for initial checks, testers should not be seen as a substitute for thorough wiring inspections. However, as a first-line tool, they offer a speedy and effective method for spotting potential hazards in electrical installations and wiring systems.
Environmental testing
Businesses also have a responsibility to ensure workplaces comply with environmental regulations. The Control of Noise at Work Regulations specifically mandates monitoring and minimising noise exposure. According to these regulations, employers must keep noise levels below specific thresholds – when noise levels reach certain limits, businesses are required to assess potential health risks and provide relevant training and information to their employees. Lighting is a further consideration. Although lighting guidelines may seem complex, they emphasise the need for different light intensities based on the task at hand. Minimum temperatures are also required in the workplace, so monitoring temperatures, particularly on winter mornings is essential.
Specialised environmental testers are essential for ensuring workplace safety and compliance. A digital sound level meter, for instance, plays a crucial role in preventing long-term hearing damage by keeping noise levels within safe parameters and ensuring that alarms can be clearly heard throughout a facility. Some meters are capable of measuring a broad spectrum of decibels, enabling effective noise compliance monitoring in areas with heavy machinery or significant industrial activity. This is vital for maintaining not only the health and safety of workers but also the operational standards required in noisy work environments.
Light meters are crucial for ensuring both emergency and standard lighting conditions are adequate for various environments. The best light meters are designed for efficiency, operating up to 80 hours on a single set of AA batteries, can cope with LED lighting and will have intuitive designs with for example, Min/Max, Hold and auto power-off functions and. Additionally, those with sensors that can be rotated to measure oblique angles or detached for easy access allow for precise and reliable measurements across diverse applications.
Safe isolation
For workers dealing directly with electrical installation and maintenance, safe isolation procedures are of paramount importance due to the high risks associated with working on or near live electrical systems. These procedures are not only vital for the direct protection of electricians but also for the safety of all individuals on a job site and choosing and using the appropriate tools is crucial.
Initially, safe isolation involves selecting a reliable voltage indicator, which must comply with BS EN61243-3, that can be tested for functionality, typically with a dedicated proving unit. The next step is to employ suitable lockout devices and warning signs for the specific circuit being tested. A basic lock-off kit should include a selection of MCB Lock Off devices, a padlock with a unique key, a hasp if more than one person is working on a system as well as lock-out tags and warning labels. This will help to prevent anyone from accidentally turning the power back on while the circuit is being worked on.
When carrying out the lockout procedure, if a switch on a distribution board or any other disconnection device is used, it must be secured in the 'off' position with an appropriate lock, complemented by clear signage to inform others about the ongoing work. The key or the code for the combination lock should then remain with the individual performing the task or with an appointed representative to ensure safety and responsibility.
Ensuring workplace safety and comfort is essential and using electrical test equipment regularly is key. Tools that assess electrical systems and monitor environmental factors like temperature and lighting, allow businesses to proactively address potential risks. For employees maintaining or repairing electrical systems, use of the correct safety rated tools and following safe isolation procedures is key. This approach not only meets safety regulations but also demonstrates a company’s commitment to its employees, ensuring that businesses can operate efficiently while safeguarding employee well-being.
Steve Dunning is managing director at Martindale. For more information visit www.martindale-electric.co.uk