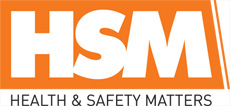
![]() |
Mark Sennett
Managing Editor |
![]() |
Kelly Rose
Editor |
Home> | Plant & Machinery | >Electrical Safety | >Suitably dressed for danger |
Home> | PPE | >General PPE | >Suitably dressed for danger |
Home> | PPE | >Workwear | >Suitably dressed for danger |
Suitably dressed for danger
25 July 2024
In the world of electrical engineering and safety, the term ‘arc flash’ is not just a technical jargon but a critical concept that can mean the difference between life and death. Andrew Dent provides an insight.

DESPITE ITS often unseen and misunderstood nature, an arc flash can unleash catastrophic consequences, from severe injuries to extensive property damage. As industries and workplaces become increasingly reliant on complex electrical systems, understanding the risks associated with arc flashes and implementing robust safety measures is paramount.
Firstly, what is an arc flash? An arc flash is a dangerous electrical event that occurs when an electric current passes through the air between conductors or from a conductor to ground. This event can happen for several reasons, including equipment failure, accidental contact, or a short circuit. The arc flash results in an intense release of energy in the form of light, heat, sound, and pressure.
During the arc flash there are several things that happen all at once, they are:
- The Arc flash can produce temperatures as high as 19,427 degrees Celsius, which is hotter than the surface of the sun. This extreme heat can cause severe burns and ignite clothing and other materials in the vicinity.
- There is a rapid expansion of air and vaporized materials which creates a pressure wave, which can be strong enough to knock people off their feet, damage structures, and cause significant injuries.
- Arc flashes produce a bright flash of light that can cause temporary or permanent vision damage. They also generate a loud noise, which can cause hearing loss.
- The explosion can propel molten metal and other materials at high speeds, leading to serious injuries or fatalities.
- The high temperatures can easily ignite nearby flammable materials, leading to secondary fires.
All these things combined can happen within a fraction of a second, but they have the potential to leave a worker with extensive serious injuries or potentially take their life. These arc flashes can happen for a few reasons from human error through to environmental effects. The most common causes being:
- Human Error: Accidental contact with energised parts during maintenance or testing.
- Equipment Failure: Malfunctioning or poorly maintained equipment.
- Corrosion: Deterioration of electrical connections and components.
- Improper Installation: Incorrect installation of electrical systems.
- Environmental Factors: Presence of conductive dust, moisture, or corrosive environments.
There are methods to support staff from generating an arc flash, the main one is to implement safety mechanisms to minimise the risk. Regular risk assessments should also be caried out to help implement the correct safety procedures. Finally, regular maintenance should be carried out to keep the electrical systems and equipment well maintained which will greatly reduce the risk of an arc flash.
If a solution cannot be engineered out and staff must be sent into an environment where an arc flash may occur, then as a last line of defence they must be outfitted with the correct personal protective equipment (PPE).
Arc flash PPE comes in a variety of products from Visors and balaclavas to protect the face through to gloves to protect the hands, often the closest part of the body to the arc flash. Arc flash protection is often scored based on the type of testing the product has undergone, the two forms of arc flash testing are the “box arc” method and the “open arc” method.
In the “box arc” method the product is exposed to an electric arc produced by a 4kA or 7kA short circuit. The heat transmitted through the product is measured during and after the test, using that data the length of time it would take to receive a second degree burn can be obtained. Using this and other data such as hole formation, melting, etc. the product will then be issued either Class 1 (4kA) or Class2 (7kA).
In the “open arc” method the product samples are exposed to multiple arc flashes where several samples need to withstand the arc flash, and several samples need to be destroyed after the arc flash. They carry out these tests with varying intensities of arc flash noting down whether the garment was destroyed or not. Once all this data is gathered the protective level of the product can be determined and scored with the 3 scores which are measured in calories per cm² (cal/cm²).
What is a calorie? The calorie was originally defined as the amount of heat required at a pressure of 1 standard atmosphere to raise the temperature of 1 gram of water 1° Celsius.
Arc thermal protection factor (ATPV): refers to the maximum incident energy (cal/cm²) that protective equipment can be exposed to and have a 50% chance to cause the onset of a second-degree burn. Ratings are based upon the total weight of the fabric. So, for example, if a jacket has an ATPV of 20cal/cm², this means that if the wearer is hit by an arc flash of 20cal/cm² then there is a 50% probability the worker will receive a second-degree burn.
Energy breakopen threshold (EBT50): refers to the maximum incident energy (cal/cm²) that protective equipment can be exposed to and have a 50% chance to have a breakopen occur. A breakopen is defined as any open area at least 1.6cm². So, in the same scenario, if a jacket has an EBT50 of 20cal/cm², and the wearer is hit by an arc flash of 20cal/cm² then there is a 50% probability that a hole greater than 1.6cm² will appear.
Energy limit value (ELIM): refers to the maximum incident energy (cal/cm²) that protective equipment can be exposed to and not have risk of second-degree burns or a breakopen occur. If a jacket has an ELIM of 20cal/cm², and the wearer is hit by an arc flash of 20cal/cm² then there is no chance of a breakopen or second-degree burns occurring. Simply, ELIM is the point at which all exposures up to that level will be within safe limits. It is a higher level of protection for the wearer.
The final element of Arc flash clothing protection is layering. Wearing multiple layers of arc flash protection clothing will give the wearer a higher level of protection. You would be mistaken to think that by adding the multiple ELIM scores of the garments together would give you the correct score. There are other factors such as the pockets of air between the layers which can act like additional insulation. Layering systems for arc garments can be requested from the manufacturer, who will be able to provide the ELIM value for the combinations of multiple garments. The manufacturer will only be able to provide this information if they have had the combinations tested.
When buying arc flash PPE always check that the product has the correct level of protection for the task required, never assume that just because it states “arc flash” that it will be correct for your task. Always engineer the problem out, if this is not possible, risk assess, and then choose the correct level of protection required for that task.
Andrew Dent Is technical manager at Beeswift. For more information, visit www.beeswift.com