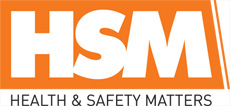
![]() |
Mark Sennett
Managing Editor |
![]() |
Kelly Rose
Editor |
Home> | Slips, Trips & Falls | >Fall Prevention | >Standing on your own two feet |
Home> | Slips, Trips & Falls | >Fall Protection | >Standing on your own two feet |
Home> | Slips, Trips & Falls | >Trip Protection | >Standing on your own two feet |
Standing on your own two feet
04 February 2020
ALTHOUGH A common perception of health and safety legislation is that it can be excessive and onerous, it is important to remember that it exists for a very important reason – to prevent injury and loss of life. Kate Breslin, product manager at SGS, looks at the processes and procedures that should be implemented to create a safer working environment and why, when it comes to slips, trips and falls, creating an active culture of reporting and prevention should be adopted.

It is with disturbing regularity that we hear or read about accidents in the workplace that could have been prevented. Anyone who thinks that the issue of health and safety at work is overplayed should consider the fact that in the 12 months to April 2018 there were 144 people killed at work, according to the Health and Safety Executive (HSE). Furthermore, there were 71,062 injuries to employees reported under the Reporting of Injuries Diseases and Dangerous Occurrence Regulations (RIDDOR), 555,000 other injuries at work and 30.7 million working days lost due to work related illness and injury.
Law and order
It is amazing to think that before 1974 approximately eight million employees had no legal safety protection at work. Although there was piecemeal legislation, which was often industry specific, The Health and Safety at Work etc Act 1974 was the first to provide the legal framework to promote, stimulate and encourage high standards in places of work.
Employers must now provide and maintain safety equipment and safe systems of work; provide information, training, instruction and supervision; and provide a written safety policy. In addition to this important piece of legislation, The Workplace (Health, Safety and Welfare) Regulations 1992 and The Management of Health and Safety at Work Regulations 1999 both contain a consistent set of requirements.
The Health and Safety at Work Act 1974 still forms the basis of workplace safety law in the UK and since 1974 there has been a massive reduction in both fatal and non-fatal injuries, with the HSE stating that the former has fallen by 85 per cent and the latter by 77 per cent. Changes in the types of work that people carry out – with the number of workers in manufacturing declining by over three million and the growth of the service sector – account for some of this improvement but certainly not all.
Cause and effect
Slips, trips and falls in the workplace represent far more than a trivial problem. In fact, they are the single most common cause of major injury in UK workplaces and, according to HSE figures, accounted for 31 per cent of non-fatal injuries reported under RIDDOR in 2017-18, with an average of two deaths per year for slips, trips or falls on same level.
These types of incidents can occur anywhere for a wide range of reasons and contributing factors. Put simply, an area seemingly risk free one day can be a real problem the next. The factors that can contribute to an incident include the floor surface, the environment, footwear, contamination, obstacles and obstructions, and the physical actions of the person involved.
The hazardous storage of tools and equipment, oil spillages, water caused by leaks, floor cleaning methods that increase the likelihood of slips occurring, a lack of warning signs when cleaning is in progress and floors and carpeting that are poorly maintained, are also factors. Likewise, a fall can occur when an individual unknowingly encounters a foreign object in his or her path, there is an unseen impediment or obstruction on the walking surface, or when a walking surface unexpectedly changes height.
There are some simple ways to help prevent slips, trips and falls. These include cleaning up spills immediately, displaying wet floor signs when appropriate and keeping walkways free of debris, clutter and obstacles. It is also important to cover cables, keep filing cabinets and desk drawers shut when not in use and encourage workers to have suitable footwear.
Case in point
The impact of a slip, trip or fall can be life changing. Take, for example, the 16-year-old girl who was employed at a fast food outlet to cook at a frying range. She slipped on water leaking from an ice-making machine and instinctively put out her hand to break her fall, which went into the deep fat fryer containing oil at a temperature of 360°F. She sustained severe burns to her left hand and forearm.
The local authority prosecuted the company and on successful conviction the magistrates imposed a fine of £15,000. The investigating environmental health officer stated that the accident was completely avoidable, as the company had failed to maintain a safe system of work or to carry out a suitable and sufficient assessment of the risks associated with slipping within the kitchen.
Then there’s the case of a company that, after a routine health and safety inspection visit from a local authority inspector, was required to replace a piece of carpet that represented a trip hazard. Some months later the inspector found that the carpet had still not been replaced and issued a written warning to the proprietor. 15 months after that initial inspection an employee suffered an injury when she tripped on the stair carpet. Tape placed across the worn out section had come away and the employee suffered a broken ankle and a dislocated foot. Ankle surgery followed and she was unable to walk for several months and still in pain and using a stick almost a year later. The proprietor pleaded guilty to offences under the Workplace (Health, Safety & Welfare) Regulations 1992, with a substantial fine being imposed and the proprietor being ordered to pay the prosecuting authority's legal costs.
High alert
Working at height is a high risk activity and since 2001 an average of 50 people in the UK have died at work each year as a result of a fall from height, and around 8,000 have been seriously injured. The construction industry has the majority of these types of incidents and of the 196 fatalities that occurred in this sector in the five years to 2016-17, 49 per cent were falls from height.
In 2013 Southwark Crown Court heard that two workers accessed the top level of a unit that was to be dismantled as part of construction work at a site in London. One of the workers slipped and fell over the side of the platform, hitting the wall and then landing on the concrete floor 5.9m below. He sustained multiple injuries including internal bleeding, a collapsed lung, and fractures to his pelvis and right arm and was left unable to work.
Injury and death to those working in the construction sector can be minimised by the provision of suitable access equipment being properly used. The Work at Height Regulations 2005 state that working at height should not be carried out unless essential, the platform must be stable and secure and there has to be adequate space to undertake the work with all open edges protected by use of guard rails and barriers.
Counting the cost
To date the largest fine imposed in the UK for a health and safety offence was £15m on Transco in 2005. That unenviable record could soon change though, as in February 2016 new sentencing guidelines for health and safety, corporate manslaughter and food safety and hygiene offences came into force. It now means potentially unlimited fines for companies and public sector bodies who fail to comply with health and safety law.
Three factors will be key in determining fines for health and safety offences – the degree of harm caused, the culpability of the offender, and the turnover of the offending organisation. The guidelines underline the need for companies of any size to have an effective approach to complying with the law, and a key message is to have sensible and effective, but also proportionate, arrangements for ensuring health and safety, and to have access to relevant advice.
Strategic direction
One of the most effective ways to ensure a high level of health and safety provision in the workplace is through an occupational health and safety management system. Not only will this help to address physical wellbeing by preventing slips, trips and falls, it can also play a key part in ensuring the mental health of employees. The Thriving at Work report found that one worker in six suffers from a mental illness and 300,000 people with long-term mental health problems lose their jobs every year.
When it was introduced in 1999, OHSAS 18001 helped to enhance the development of accident prevention and risk management strategies. OHSAS 18001 certification demonstrates a company's commitment to providing a safer working environment and protecting its employees. By creating objectives, targets and documented responsibilities, awareness of the issue becomes ingrained in an organisation’s ethos and culture.
Standards are constantly evolving and in early 2013, the International Organization for Standardization (ISO) received a new work item proposal from the British Standards Institute (BSI) for the development of a standard for occupational health and safety management systems. This proposal was subsequently approved and ISO established a project committee and assigned the number ISO 45001 to the future standard. In March 2018 ISO 45001:2018 was ratified and will supersede OHSAS 18001, which will be withdrawn in 2021, with organisations now being urged to make the migration to the new standard.
Theory of evolution
ISO 45001:2018 is designed to integrate with other ISO management systems standards and complement ISO 9001:2015 and ISO 14001:2015, with key terms and definitions consistent across all standards, a common superstructure in Annex SL, and parallels in the core text.
Annex SL is based upon the Plan, Do, Check, Act structure pioneered by management quality expert, W Edwards Deming. This is used to ensure that the hazards and risks associated with an organisation’s activities, products and services are systematically identified, assessed, controlled, monitored and continuously improved.
The framework for Annex SL consists of 10 clauses, which render all ISO management systems more compatible and consistent, giving writers, management and auditors the advantage of a basic set of generic requirements as a guideline to follow. It has simplified the use of ISO management systems and eliminated the differences previously experienced in the perception and implementation of such standards. By providing standardised text, terms and definitions for management system standards, Annex SL has also lowered the administrative costs for organisations that choose to apply more than one standard.
Top down approach
Although there are similarities between OHSAS 18001 and ISO 45001:2018, there are some key differences too and the most fundamental concerns the role of top management. The new standard requires them to be much more involved in understanding an organisation’s risks, opportunities and stakeholder expectations, along with ensuring that its operational objectives are compatible with its overall strategic direction.
In addition, understanding the internal and external factors that can affect an organisation’s ability to manage its occupational health and safety performance and achieve its intended outcomes is to the fore. ISO 45001:2018 also facilitates an understanding of the needs and expectations of workers and other interested parties, so that existing knowledge can be considered when establishing a management system.
‘If you can’t measure it, you can’t manage it,’ is the now famous quote from renowned management consultant, Peter Drucker. ISO 45001:2018 recognises the importance of the gathering and analysis of data and requires an organisation to implement key indicators. This leads to a structured assessment of performance and organisations are expected to establish monitoring and measuring that is relevant, reliable and ensure that results are evaluated and analysed. The reporting and investigation of incidents allows hazards to be eliminated and associated risks to be minimised, with documented information communicated to relevant workers and other interested parties.
In terms of attitudes towards health and safety provision, a study by SGS found that the UK’s public sector organisations are falling well behind their private sector counterparts. Nearly 47 per cent of private sector organisations have implemented an occupational health and safety management system, compared to only 36 per cent of those in the public sector. Meanwhile, more than 54 per cent of private sector organisations conduct health and safety inspections on a monthly basis, with only 27 per cent of public sector organisations doing likewise.
Knowledge is power
All too often the potential for a slip, trip or fall is due to an inability, or unwillingness, on the part of an organisation to take the issue seriously by undertaking a formal risk assessment. Put simply, if risks aren’t identified, a building’s occupants are in danger and a risk assessment is not about creating copious amounts of paperwork, but rather about taking sensible measures to control the risks in a workplace.
A risk assessment is simply a careful examination of what could cause harm to people, so that it is possible to ascertain whether enough precautions have been taken to prevent incidents. Workers and others have a right to be protected from harm caused by a failure to take reasonable control measures and employers are legally required to assess workplace risks, so that plans can be put in place to control them.
The HSE advises employers to follow five steps when carrying out a workplace risk assessment:
• Step 1 – Identify the hazards
• Step 2 – Decide who might be harmed and how
• Step 3 – Evaluate the risks and decide on precautions
• Step 4 – Record your findings and implement them
• Step 5 – Review your assessment and update if necessary
Cultural analysis
ISO 45001:2018 certification demonstrates a company's commitment to a safer working environment and the protection of employees against injury at work. However, it is also important to encourage a culture of ‘near miss’ reporting and preventative action.
Most individuals have a tendency to feel a sense of embarrassment or feel that they have been clumsy if they have a slip, trip or fall, and don't wish to ‘make a fuss’. However, if it can happen to one person then it’s highly likely that it could also happen to someone else – with potentially more serious consequences. Therefore, employees should not be reluctant to report any near misses and, if they are not able to rectify the issue themselves, be encouraged to highlight potential dangers or risks to a relevant person. Employees should also be asked to regularly look around their work areas to identify any hazards and be proactive in removing them.
Think about it
Reducing the risk of slips, trips and falls in the work environment demonstrates diligence and commitment towards good and responsible health and safety management, significantly reduces the likelihood of accidents, and provides a framework for legal responsibilities. ISO 45001:2018 compliance encourages all levels of an organisation to become involved through setting objectives, targets and documented responsibilities. Some business owners might think that they can’t afford to implement an occupational health and safety management system – but the real question they should ask is, can they afford not to?
For more information, visit www.sgs.co.uk
- Services now accessible in one click
- Satisfied with survey
- ISO/FDIS 45001:2018 training courses
- SGS urges swift transition to ISO 9001:2018
- Pre-audit & gap analysis
- Focusing on mental health and wellbeing
- Exclusive Mental Health in the Workplace sponsorship
- SGS finds private sector has better health and safety
- Maintain food and hygiene standards with SGS Academy courses
- 0HSAS 18001 certification success