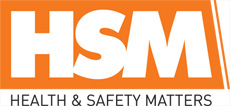
![]() |
Mark Sennett
Managing Editor |
![]() |
Kelly Rose
Editor |
LATEST NEWS
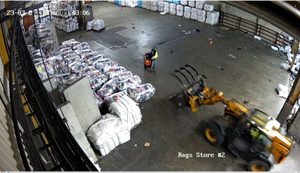
Textiles firm fined after worker hit by vehicle
13 July 2025
A COMPANY in the West Midlands that reclaims and processes textiles has been fined £300k after one of its workers was hit by a telehandler. [Read More]
EDITOR'S PICK - View More Editor's Pick
- Textiles firm fined after worker hit by vehicle
- Blue-collar workers say workplace is unsafe
- Workplace temperatures - week of action
- Call to get ahead of site cooling
- Tork receives certifiication first
- Recall of safety shoes exposes substandard PPE crisis
- Ban on controversial NDAs silencing abuse
- Teen’s thumb reattached after being severed off
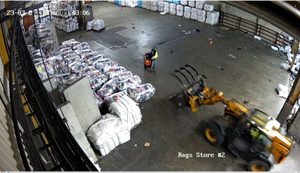
Textiles firm fined after worker hit by vehicle
13 July 2025
A COMPANY in the West Midlands that reclaims and processes textiles has been fined £300k after one of its workers was hit by a telehandler. [Read More]
SPONSORED CONTENT
-
Safety Unlimited pushes back the boundaries
The new, unrivalled and highly versatile Pushback System from critical storage specialists Safety Unlimited allows you to stack pallets containing any permutation of drums or IBCs within the same ultra accessible, time and space saving unit. [Read More]
More Sponsored Content
- Real-time measurements improve respirator fit testing
- A breath of fresh air: Zehnder presents at the 2020 Safety and Health expo
- Cardinus Bring New Expertise in Health, Safety and Property Risk
- Cardinus Partner with Warriors to Set New Standards in Stadium Safety
LATEST VIDEOS
INDUSTRY UPDATE