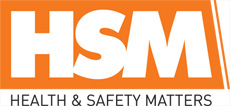
![]() |
Mark Sennett
Managing Editor |
![]() |
Kelly Rose
Editor |
Home> | Handling & Storing | >Forklift Truck Safety | >Get home safe |
Get home safe
18 September 2018
As Safetember, the Fork Lift Truck Association’s (FLTA) annual fork lift safety awareness campaign drew to a close, Peter Harvey discusses the challenges facing those responsible for ensuring safe operations.
NO ONE ever plans to have an accident, but the reality is that accidents can and do happen. Nowhere is this truer than in the materials handling industry, where we see humans and lift trucks work side-by-side day in, day out.
When this partnership goes as ‘planned’, it’s an exceptionally good one. But, what about when it goes off-plan? The results range from costly damage to racking and stock to hospitalisations, life-changing injuries or worse.
It’s too high a cost and it happens more often that you may think. On every working day in the UK, five people are seriously injured in accidents involving lift trucks. Sad events like these leave a big wake. They change the lives of those involved, as well as their families, friends and colleagues.
Employers are by no means immune. In a split second, an accident can place a stable and successful operation into significant financial peril. Worse still, nearly every single one of these life-changing accidents could have been avoided.
Human error
It would be easy if we could simply blame the machine. But, innovations in truck design mean that mechanical failures are very rare. Human error, on the other hand, is not. With so many people (and decisions) involved in lift truck operations, it’s incredibly easy to stray from best practice.
All it takes is an operator, colleague or manager/supervisor, to lose focus and take action without considering the consequences. That’s why, during Safetember, with the support of everyone working with or alongside lift trucks to take responsibility for their colleague’s safety, under the theme ‘make sure they get home safe’.
This message underlines our belief that safety is a collective responsibility. While leadership must come from managers and supervisors, everyone has a part to play in making their sites and jobs safer for themselves and their colleagues.
In recent years, our Safety Partner Mentor has developed free resources to support our campaign efforts. And this year was no exception. During Safetember, the company launched a new, free tool to help employers assess their refresher training needs. And, along with their free Show Your Hand campaign kits which aim to strengthen non-verbal communication, it’s available now from mentorflttraining.co.uk.
I sincerely hope that HSM readers will take advantage of the practical guidance opposite and that it will make a real and long-lasting difference to staff safety. After all, there is nothing more important than ensuring your colleagues go home safely at the end of each and every working day.
Everyone’s accountable
Managers and supervisors should be aware of what’s expected of themselves, as well as colleagues, to minimise the risk of accidents.
It would be impossible to sum up these responsibilities in a single article, so FLTA has compiled a list of dos and don’ts. It is by no means exhaustive.
Managers and supervisors should:
- Be adequately trained to recognise safe and unsafe practice;
- Know how to carry out effective observations regularly and read L117 (Rider-operated lift trucks: Operator training and safe use);
- Recognise the characteristics of lift trucks and associated hazards;
- Be vigilant with operators – reinforce to operators that trucks must only be used for their intended purpose and within their load capacity;
- Continuously monitor operators – giving praise and feedback as necessary organise training to fill any gaps in knowledge and ensure pre-use checks are being properly completed and recorded;
- Inform anyone who may come into contact with fork lift trucks of associated dangers before first contact (ideally at induction);
- Segregate workers and visitors on foot from lift truck operations, ensuring pedestrians adhere to segregation procedures;
- Encourage staff to speak up when they see bad practice occur and make sure all operators and pedestrians follow company procedures;
- Review operations continuously to identify improvements and communicate effectively with operators, pedestrians and line managers;
- Maintain and promote health and safety standards;
- Complete and record management checks on a regular basis; and
- Plan safety initiatives to avoid complacency
Managers and supervisors should not:
- Allow anyone to operate a machine unless they are qualified and authorised to do so;
- Never allow operators to carry passengers or lift passengers; and
- Not allow unsafe acts or practice to go unnoticed
Manage safely
When it comes to fork lift safety, the HSE makes it very clear that ultimate responsibility sits squarely on management’s shoulders. If there’s an accident on site, involving workers under your supervision, there’s a reasonable chance that you could be found at fault.
L117 (Rider-operated Lift Trucks: Approved Code of Practice) makes it clear that, as a manager, you have a legal duty to uphold safety. Your responsibilities include: carrying out risk assessments and ensuring necessary action is taken and identifying training requirements among staff.
As the person who ultimately influences workplace safety culture, you may have training needs yourself – so you’re able to easily identify bad practice and act upon it. There are a few effective measures which those overseeing operations can take to help them in upholding their responsibilities.
Appoint a safety champion
Management roles are never easy. With other duties and responsibilities to take care of, many managers spend more time in the office than on the work floor, overseeing operations.
In such cases, appointing someone to take assume that responsibility, to actively advocate best practice and supervise fork lift operations, is crucial. Your designated safety champion will need to be:
- Committed to improving the safety of your fork lift truck operations;
- Willing to dedicate the time to supervise and oversee safety improvements Appropriately trained to take on a role of such responsibility;
- Competent enough to identify and assess potential hazards in the workplace; and
- Confident enough to lead internal meetings and act appropriately when bad practice occurs
Make sure your managers/supervisors are properly trained
Your managers may hold ultimate responsibility for safe operations, but that doesn’t mean they need to be able to operate a forklift. What is crucial, however, is that they possess the skills and knowledge to adequately assess operational safety and take appropriate action where necessary.
Training, crucially, gives them the skills and knowledge they need to meet their legal duty to uphold workplace safety. Specifically, they must:
- Understand all tasks performed and the risks involved;
- Oversee regular inspections of the site and equipment;
- Act to keep both in good shape; and
- Ensure practices are in place to minimise risk.
Several FLTA members offer such training. Use the Member Finder at www.fork-truck.org.uk to locate one.
Share best practice
Seeing how other sites are organised, identifying their problems and looking at what safety precautions they have taken, can be a real eye-opener. It equips you with ideas and options which you can take back and implement at your own site.
Each year, the FLTA’s Safe Site Award celebrates companies that have gone above and beyond in their efforts to attain safe working conditions for employees working on and around fork trucks.
From safety barriers to training initiatives, video tutorials to site restructuring, the Safe Site Award’s past entrants are a veritable goldmine of effective – and often economical – safety measures.
Each year, our winners and highly commended entrants are invited to share their experiences and knowledge with delegates at the National Forklift Safety Convention.
Keep best practice in check
‘Managing Forklift Operations: Manager’s Checklist and Best Practice Guidance Notes’ is a valuable tool, which formalises and documents safety checks.
Developed in association with Safety Partner Mentor Training, as part of Safetember 2015, the pocket-sized booklet offers checklists designed to give managers and supervisors a formal structure for safety checks.
The booklet also includes a range of information which managers might need during a shift, such as important contacts, sources of further information and best practice advice.
Approved Code of Practice (L117)
This short, well-illustrated HSE publication is the definitive guidance for fork lift operations. It outlines the seven main pieces of legislation regulating the use of industrial trucks and, in clear and concise language, highlights what you need to do to comply with the Law.
Every fork lift manager should have a copy. Physical copies can be ordered from the HSE or the FLTA web shop. Alternatively, you can download a copy – at no cost – from www.hse.gov.uk.
Safety resources
Keeping track of constantly shifting safety regulations, government legislation and best practice procedures is a tough ask, but help is at hand. The FLTA’s Safe User Group (SUG) has been created to keep forklift managers up to date on best practice and the latest changes to legislation.
In addition, they get heavily-discounted admission to National Forklift Safety Convention; exclusive access to the FLTA’s comprehensive online resources; big savings on FLTA store items; technical bulletins and more.
Peter Harvey is chief executive of the Fork Lift Truck Association. For more information, visit www.fork-truck.org.uk- FLTA opens online nominations for Awards for Excellence 2014
- Manage to stay safe
- Recruiters warned: Fork lift truck 'licenses' do not exist
- Fork lift workers are not immune from falls
- Safety to the fore
- Peter Harvey appointed FLTA chief executive
- FLTA seeks Jurors for Excellence Awards 2018
- Advice issued following classification of Diesel fumes as carcinogenic
- Martin Bayfield to host 2016 FLTA Awards
- Why you need to be part of Safetember