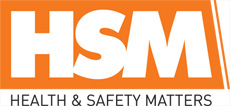
![]() |
Mark Sennett
Managing Editor |
![]() |
Kelly Rose
Editor |
Home> | Plant & Machinery | >General Plant & Machinery | >Experienced employee partially severs two fingers |
Home> | Plant & Machinery | >Physical Guarding | >Experienced employee partially severs two fingers |
Experienced employee partially severs two fingers
04 September 2023
A WELSHPOOL manufacturing company has been fined £100,000 after one of its employees partially severed two fingers while trying to find a fault in a machine.
Interior Products Group Limited (known as Newmor Group Ltd at the time of the incident) manufacture and sell pre-finished fit out products to a variety of sectors.
The experienced employee, from Wrexham, was attempting to identify a fault in an edgebander machine – used to apply edging tape to the raw edges of wood panels with a hot-melt adhesive or glue.
Wrexham Magistrates’ Court heard how the experienced employee suffered the injuries while checking for debris on the trimming unit of the edgebander. Having failed to turn the machine off correctly before raising it to look inside, the worker then stepped over two supporting rails and placed their fingers on a trimming unit, resulting in two being partially severed.
Following an investigation by the Health and Safety Executive (HSE), it was discovered that although the company had carried out a number of risk assessments on the machine, they failed to identify the hazards presented by the cutting and trimming units from the front of the edgebander. They also failed to provide suitable and sufficient, information, instruction and training to enable their staff to carry out activities such as cleaning, fault finding and minor repairs safely.
Interior Products Group Limited of Madocs Works, Henfaes Lane, Welshpool pleaded guilty to breaching Section 2(1) of the Health and Safety at Work etc Act 1974. They were fined £100,000 and ordered to pay costs of £7,688.
Speaking after the case HSE inspector Joe Boast said: “Those in control of work have a responsibility to devise safe methods of working and to provide the necessary information, instruction and training to their workers in that safe system of working.
“If a suitable safe system of work had been in place prior to the incident, the life changing injuries sustained by the employee could have been prevented.”
- Dangerous building site conditions leads to convictions
- Survey shows employers put drivers at risk
- BOHS appoints new president
- Worker suffers fractured spine
- RoSPA warns firms not to rush return-to-work practices
- NEBOSH HSE leadership session: What is good health and safety leadership?
- RoSPA warns firms not to rush return-to-work practices
- Relaxation of drivers’ hours a safety risk
- Registration open for HSM Digital Conference 2023
- Brake voices smart motorway concerns