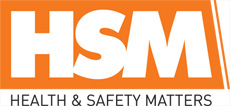
![]() |
Mark Sennett
Managing Editor |
![]() |
Kelly Rose
Editor |
Home> | Slips, Trips & Falls | >Fall Prevention | >Chemical company employee suffered multiple fractures |
Home> | Slips, Trips & Falls | >Fall Protection | >Chemical company employee suffered multiple fractures |
Chemical company employee suffered multiple fractures
17 May 2021
ESSECO UK Ltd has been sentenced for safety breaches after an employee fell 2.7 metres onto a concrete floor and suffered a fracture to his skull.
Health and safety inspectors have also said it was fortunate nobody was injured in an explosion at a chemical plant in Wakefield in November 2014, for which the company was also fined.
Leeds Crown Court heard that on 11 May 2015, the employee entered the first floor of a building on Calder Vale Road, Wakefield known as ‘the Wendy House’, in order to inspect the building prior to demolition. As he walked across the metal decking on the first floor, he fell through a gap, which had been created by removal of a piece of equipment, to the floor below. He suffered a fractured skull, fractures to five vertebrae a broken clavicle, broken ribs, a cut on the leg and a dislocated finger.
An investigation by the Health and Safety Executive (HSE) found that the building was redundant and due for demolition. A section of the metal decking floor had previously been removed on 24 April 2015 leaving a gap measuring 0.9m by 0.7m.
Esseco UK Ltd of Calder Vale Road, Wakefield, West Yorkshire pleaded guilty to breaching Section 2 (1) of the Health & Safety at Work etc Act 1974. The company has been fined £140,000 and ordered to pay costs of £7,642.
Speaking after the hearing, HSE’s head of operations (Chemicals South and East and Human Factors) Catherine Cottam said, “Falls from height remain the one of the largest single causes of death and serious injury within the workplace, and as such it is vital that employers ensure that work with associated with height risks is properly planned, executed and monitored.”
Esseco was also prosecuted by HSE following an explosion at the company’s chemical plant, also in Wakefield. Nobody was hurt in the blast on 19 November 2014, which caused damage to the steel structure and a release of sulphur dioxide into the atmosphere. The construction of a new process plant at the site was near completion and commissioning of the plant had started in September 2014. Trials were being run on the new plant, which involved the use of the chemicals used in the production process of agricultural liquid fertilizer, including sulphur prill (granules of solid sulphur). There were problems with the enclosed bucket conveyor feed system, which transported the prill from a hopper into the chemical reactor tank. Sulphur dust was created within the conveyor due to physical break down of the prill. The sulphur dust cloud ignited, which caused the explosion.
An investigation by HSE found that commissioning of the plant with inert materials would have identified that the conveyor system was not aligned correctly, resulting in physical degradation of the prill to form an explosive dust cloud. The specification of components of the conveyor system had not been checked by the dutyholder resulting in the presence of potential of ignition sources within the conveyor system.
The company pleaded guilty to breaching Regulation 4 of the Control of Major Accident Hazard Regulations 1999, was fined £90,000 and ordered to pay costs of £7,642.
Catherine Cottam added, “It was fortunate nobody was injured when this explosion happened. Risks associated with the commissioning of new plant must be considered in detail at early planning stages, and commissioning must be carried out in a detailed and controlled fashion to ensure that risk is reduced to a level as low as is reasonably practicable.”
- Pallet company fined after fork lift truck accident
- Farmers warned of machinery fire risk
- Chemical Awareness & COSHH Management free workshop
- Network Rail fined £3.4m following death of track worker
- Crackdown on illegal waste activities
- First corporate manslaughter conviction
- Joinery firm fined for health and safety failings
- Injured workers should retain legal representation
- Sarah Newton appointed as new Chair of HSE
- IOSH competency framework to 'drive highest standards'