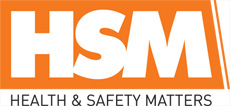
![]() |
Mark Sennett
Managing Editor |
![]() |
Kelly Rose
Editor |
Home> | Trade Body | >BSiF | >Shield yourself |
Home> | Industry Update | >Company News | >Shield yourself |
Home> | PPE | >General PPE | >Shield yourself |
Shield yourself
31 July 2023
From false product certifications and missing documentation to misleading performance claims, non-compliant personal protective equipment and safety products are rife and can present significant risks. The British Safety Industry Federation (BSIF)'s Check, Select, Protect scheme provides a simple solution for procuring appropriate products

THERE ARE many factors that can lead to injuries in the workplace - and it is essential for employers to do all they can to minimise the number of avoidable incidents in line with the HSE’s hierarchy of controls. While PPE is often referred to as a last resort for protecting against risks, where it is necessary it’s essential to ensure that workers have access to safe and compliant products.
PPE and safety equipment risks
Following the “Risk Assessment” the selected PPE must provide the required levels of protection for any workplace hazards and need to be worn and used correctly. The PPE must also fit well and be comfortable in order to perform and ensure wearer compliance.
One of the biggest challenges can be ensuring that the PPE is up to standard. There is a vast array of products on the market from thousands of suppliers across nearly all PPE categories. Those in charge of PPE and safety product procurement need to be extremely vigilant, with suppliers all too often incorrectly claiming UKCA or CE approvals. Although the law states that PPE must be correctly tested and certified to comply with the Personal Protective Equipment Regulations, the lack of market surveillance and enforcement in the UK means it can be difficult to distinguish responsible suppliers from less responsible ones.
Nonetheless, the British Safety Industry Federation's own research has clearly and consistently shown an alarming prevalence of non-compliant PPE and safety equipment currently on the market. Between December 2021 and December 2022, we completed tests on 127 non-BSIF member products, which included checking their compliance with relevant standards and testing whether they perform as advertised. Only 18 products were fully compliant, with 108 - or 85% - failing to meet regulatory criteria.
By contrast, 86% of the 387 tests on products supplied by members of the BSIF's Registered Safety Supplier Scheme (RSSS) passed immediately. The issues around the remaining 14% were then quickly resolved and all 387 products are now fully compliant.
It is difficult to determine how much of the overall PPE in use is non-compliant, but the test results illustrate that it is likely to be an uncomfortably high number.
Consequences
Non-compliant products often do not perform as they should, putting workers at risk and, in doing so, expose businesses, duty holders and individuals to prosecution for failing to protect staff.
It is also clear that many employers are unaware of the ramifications if they do not carry out effective due diligence. Employers’ legal duty of care is compromised when a non-compliant product is specified regardless of whether it was selected inadvertently, and in addition to obvious safety concerns, there are significant financial, legal and reputational consequences.
Solution
Sourcing products from companies signed up to our Registered Safety Supplier Scheme (RSSS) is a simple way to cut the risk of inappropriate PPE selection and the serious consequences that can occur. We recommend that buyers and end users follow the Check, Select, Protect process to ensure their PPE is fit for purpose.
CHECK
The first step should always be to check suppliers are BSIF-registered.
Serious PPE suppliers already comply with stringent demands with regard to legislation, regulation, ethical trading. Signing up for the RSSS is evidence of their intention to go beyond the standard obligations. It involves a commitment to ensuring the highest quality standards by endorsing process audits and random independent product testing.
Process audits feature an extensive checklist of compliance requirements within the regulatory framework as well as a review of procedures to support safe and effective product recall.
RSSS membership also includes the obligation to enrol customer-facing sales personnel in the NEBOSH-endorsed Safe Supply Qualification. This course features a series of E-learning modules followed by an invigilated exam resulting in the qualification. It confirms that an individual has demonstrated a clear understanding of the various factors that define the safety and personal protective equipment market and is well-placed to engage in professional, plausible and credible discussions with PPE decision-makers.
Companies do not need to sign up for the RSSS to meet their legal obligations. They choose to do so to demonstrate their determination to go above and beyond for their customers.
SELECT
The BSIF's own testing shows all too clearly that not all PPE is created equal. Those responsible for procurement are responsible for selecting appropriate, certified and compliant products that meet workers' specific requirements.
Due diligence is vital. Buyers must assess the extent to which the product is fit for purpose. They should also look for wearer benefits above and beyond protection and make sure it fits comfortably in order that it performs correctly. They must also determine whether it is compatible with other PPE that may be required.
With the exception of single-use products, buyers should also consider the lifespan of the products, which has potential consequences for safety, cost and the environment. Any sustainability claims - especially around environmental impact - should be backed up with clear evidence. All of the BSIF Registered Suppliers are required to adhere to the Competition and Markets Authority (CMA) Code of Conduct1 on “Greenwashing”.
The BSIF has created a checklist to help specifiers and users check whether PPE is fit for purpose. It includes questions such as whether the PPE has a UKCA, UKNI or CE Mark; if it was issued with user instructions; and if there is a Declaration of Conformity. If any questions present cause for concern, users should seek support and guidance from their company’s health & safety advisor and the manufacturer of the PPE. BSIF also offers an additional checklist featuring advice on how to check if the supporting documentation for PPE is genuine.
Buyers can also optimise the process by sourcing through a BSIF member. As well as providing peace of mind around product compliance, RSSS companies have the competence, capability and knowledge to provide expert advice on the most appropriate PPE
PROTECT
The UK has one of the best combined health and safety records in the world, but substandard PPE and safety products are all too common. Buyers and specifiers of these products are responsible for ensuring they are properly certified and approved so that they provide the protection workers need.
Verifying that your supplier is signed up to the RSSS provides reassurance that the necessary checks have been performed and that they are committed to the highest standards. Companies displaying the RSSS shield have signed a binding declaration that the PPE and safety equipment they offer meets the correct standards, fully complies with the regulations and is UKCA and or CE marked.
Anyone can sell safety, but you shouldn't buy safety from just anyone: Always specify the shield.
References
Find your nearest Registered Safety Supplier at www.registeredsafetysupplierscheme.co.uk/suppliers/
- CEO's desk - June 2021
- About the British Safety Industry Federation
- Fit2Fit success
- A fresh new look for the British Safety Industry Federation is unveiled
- EN353-1 Safety warning
- Working in the rain?
- Safer Highways
- Battling against fake and illegal products
- Working towards standardisation of the Oil Storage Regulations
- Questions & Answers - Selection of Chemical Clothing