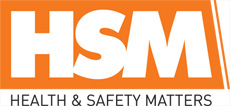
![]() |
Mark Sennett
Managing Editor |
![]() |
Kelly Rose
Editor |
Home> | Trade Body | >BSiF | >Cut through the noise |
Home> | PPE | >Ear Protection | >Cut through the noise |
Cut through the noise
09 September 2024
IF WORKERS are exposed to excessive noise, high-quality hearing protection is vital. British Safety Industry Federation (BSIF) CEO Alan Murray explains how PPE buyers can identify the protection they need – and avoid the large number of substandard products

Construction, manufacturing and engineering workers often face high levels of noise exposure on a daily basis. Excessive noise can impair concentration and focus, potentially increasing the risk of workplace accidents. It can also lead to permanent noise-induced hearing loss and even deafness.
The ear contains sensory ‘hair cells’ that are responsible for converting the mechanical sound vibrations into electrical signals that the brain can interpret as sound. Regular exposure to loud noise can damage these hair cells, which means they can no longer send signals to the brain and noise will not be heard. This type of hearing loss cannot be repaired – once lost, it stays lost.
Tinnitus is another significant risk. It is a distressing condition that may include the perception of ringing, whistling, buzzing, hissing or humming, often leading to difficulty concentrating, sleep disturbances and stress.
Based on Labour Force Survey data, it is estimated that around 11,000 workers in Britain had work-related hearing problems in the period from 2020/21 to 2022/23.1 The Industrial Injuries Disablement Benefit scheme, meanwhile, recorded 85 new cases of deafness in 2022. This is based on a measured loss of more than 50 dB of hearing in both ears.
The PPE regulation (EU) 2016/425, which came into effect in 2018, recognises harmful noise as an irreversible health risk. As such, hearing protection moved from category II (intermediate PPE) to category III (complex PPE). So what action do employers need to take to keep their workers safe?
Controlling risk
Employers have a legal responsibility not to damage the hearing of their workforce. The 2005 Control of Noise at Work Regulations require them to assess the risks to employees from noise at work and take action to reduce the noise exposure that produces those risks.
Ideally, the source of the noise should be eliminated completely. If that is not possible, employers should investigate whether the noisy process can be undertaken in a different, quieter way. If it can’t, it may be possible to limit the transmission of noise through measures such as dampening vibrating panels, fitting silencers to exhausts, acoustically screening or enclosing noisy components, or providing noise havens at workstations. Employers should also implement administrative controls including buying or hiring low-noise equipment as policy and ensuring the equipment is properly maintained.
If these measures are insufficient, hearing protection is required. Employees should receive hearing protection if noise exposure is above the lower action level of 80dB average or 135dB peak. Noise levels above 85dB average or 137dB peak represent the upper action level and require action to reduce noise exposure with a planned programme of noise control. The exposure limit values, meanwhile, are 87dB average and 140dB peak and must not be exceeded.
All employees and visitors who are required to enter noisy areas should receive suitable hearing protection along with instructions and training to ensure it is worn correctly. It should be worn at all times in the noisy area. Removing protection for just five minutes when faced with an hour of noise will reduce the protection achieved by more than half.
Selecting safe products
It is important to ensure that the hearing protection provided is suitable for the user and their work activities, and that they can use it comfortably with any other required PPE or equipment.
Hearing protectors receive a Single Number Rating (SNR) based on the level of noise reduction they provide when fitted correctly. Choosing the correct product for the level and duration of the noise hazard is important. This will not usually be the highest level available. Users will find it uncomfortable and isolating if they use too high a level of protection – and they will be more likely to remove it.
PPE buyers should also take care to only buy products that perform as advertised. All hearing protection must have UKCA or CE marks and comply with all relevant PPE regulations. However, British Safety Industry Federation (BSIF) investigation has revealed that hearing protection on the UK market from non-BSIF Registered Safety Suppliers frequently shows failures against product claims and/or documentation.
Registered Safety Supplier Scheme
We work hard to eliminate unsafe PPE from the market. Our Registered Safety Supplier Scheme (RSSS) was set up with the aim of tackling the threat posed by non-compliant and potentially unsafe products The RSSS was created to provide assurance to users that only compliant and correctly performing products are being supplied through a capable, educated, competent supply chain.
We carry out tests on member products as well as non-member products. Annually, or in the event of a complaint, we will source on the open market one product from a registered member’s PPE or relevant related product offering. An accredited test laboratory will test the product to one or more clauses of the relevant standard. In the event of a product fail, the BSIF will contact the member to begin corrective measures – or ensure the product is withdrawn from the open market if required. Any member that refuses corrective action and communication can be removed from the RSSS and Trading Standards will be informed.
Buyers can be assured that any vendor displaying the RSSS shield has signed a binding declaration that the PPE and safety equipment they offer meets the correct standards, fully complies with the regulations, and is appropriately UKCA and or CE marked.
Harmful noise is too big a risk to take chances. Where PPE is required, UK buyers and specifiers of PPE should always look for the RSSS shield so they can be confident that products will deliver the protection that users require.
In April 2024, the BSIF released a new hearing protection campaign Just because it fits. The campaign focuses on hearing protection and making sure that the selected PPE fits and is effective when incorporating other elements of PPE such as safety helmets.
A full list of registered suppliers is available to view at: https://www.bsif.co.uk/rsss
[1] https://www.hse.gov.uk/statistics/causdis/deafness/index.htm
We suggest buyers and end users follow a simple three-step process when buying PPE to ensure that products are fit for purpose:
1) CHECK your supplier is BSIF registered. BSIF Audited suppliers are compliant, competent and trustworthy. Don't settle for less.
2) SELECT appropriate, certified and compliant products. Registered Safety Suppliers can support the product selection process through their competence, capability and knowledge.
3) PROTECT your workforce and your business. Registered Safety Suppliers go above and beyond, helping to keep your people safe and helping your business to thrive.
Anyone can sell safety but you shouldn't buy safety from just anyone: Always specify the shield.
- Clean Air? Take Care! campaign kicks off
- Providing a helping hand to the industry
- Seton joins Registered Safety Supplier Scheme
- The BSIF comments on the Government's announcement of a "red tape blitz to boost business growth"
- BSIF In Action: Westminster updates
- CEO's desk
- Recognising excellence
- BSIF Commended Product Innovation Awards
- BSIF Welcomes Chinese Safety Delegation
- BSIF Launch the Safe Supply Qualification
- Breaking free from a cycle of failure
- From the Secretary's desk
- Support for Exporting Activities
- Breathe easily with Fit2Fit
- BSIF Safety Awards 2010 launched
- Ensure you purchase safe products - look for the Registered Safety Supplier shield
- PPE Regulations - where from here?
- Year of the Ear initiative commended
- From the Secretary's desk
- BSIF at the Safety & Health Expo