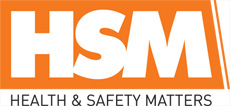
![]() |
Mark Sennett
Managing Editor |
![]() |
Kelly Rose
Editor |
Food for thought
25 July 2017
Sibtain Naqvi, UK product marketing manager for workwear at Berendsen examines the 10 key considerations when choosing workwear for the food industry.
There are many things to consider when choosing workwear for employees in the food industry. Most importantly, the garment should support the overall risk management for food safety and ensure that the products are not exposed to contamination risks from the employees. And of course, the workwear should be comfortable to wear for all employees, regardless of the tasks they are performing.
To help you when choosing workwear for your food company and to secure that you can live up to a high level of food safety and hygiene, not only now but also in the future, we have collected 10 key considerations:
1. Level of risk
Most importantly, the requirement for workwear when producing food correlates with the risk level in the production. The more perishable the food products, which you are producing, are, the higher the risk level. This is, therefore, crucial to consider when choosing your workwear setup. Furthermore, the production setup (open/closed) as well as the production process influences the risk level too.
Overall, we find it useful to work with three different levels of risk:
Maximum risk (handling of unpackaged, extremely perishable food for immediate consumption, e.g. salads or sushi)
High risk (handling of unpackaged perishable food or ingredients sometimes subject to further processing, e.g. raw meat)
Low risk (handling of not easily perishable food subject to further processing, e.g. potatoes or coffee)
Once you have identified the risk level, you can put together your workwear collection. In general, the higher the risk, the more stringent the design of the workwear should be. For instance, there should be no pockets on garments that are being used in maximum risk production areas, and only inside pockets in high-risk areas, in order to prevent foreign matters from ending up in your products or production process.
2. Requirements and expectations from your customers
Today, many food producers experience an increase in requirements from their customers. For instance, retailers, who require the whole supply chain to comply with certain standards for food safety and audit them regularly. What the employees wear during production has a huge impact on food safety, and the workwear setup can easily be standardized to comply with widely used international and national standards for food safety such as ISO 22000, BRC, Tesco and HACCP. Read more about how to comply with the standards here [link to the other content piece].
3. Protective aim of workwear
Usually, when working with food production, the work itself is not tied to safety risks for the employee. The most important function of the workwear is that it protects the products. However, there are exceptions for employees in specialist roles e.g. maintenance employees, who have to enter the production area to fix machines for instance. In these circumstances, the garment must protect both the employee and the products in production, as the work sometimes needs to be carried out, while the production is still running.
4. Climate in the production area
The workwear needs to be comfortable for the employees to wear, in order to ensure the best working environment. This means that the climate in the production area should also be considered when choosing workwear. If the temperatures are high, the clothes need to be light whilst still ensuring a high level of food safety. If it is cold, a thermal jacket is necessary. However, this fabric may not live up to common food safety standards and must, therefore, be worn underneath the regular coat or jacket, in order to meet the standard food safety requirements.
5. Right fit for everyone
The workwear needs to fit all employees and not hinder them in their tasks. Therefore, you should consider whether there are any tasks, which require that certain functionalities are added to the workwear, in order to make it fit for purpose. For example, workwear with sleeves made from water-repellant material, if the work includes regular contact with water and general moist. Also, consider if a standard unisex collection of workwear is sufficient, or whether you want to include female styles as well to ensure that the female employees feel comfortable wearing their workwear. You might also have a need for special sizes (extra tall, petite, etc.), all of which should be considered when choosing workwear setup.
6. Need for visual zone markings or monitoring your wearers behavior (when do they change to clean garments and return them onsite)
In certain production areas, where contamination is a maximum risk, it might be important that the uniforms help to visually control the flow of employees from one area or section to another. Here, zone markings on uniforms can be helpful, but it is important that it is done in a way that does not compromise food safety. Another way to do this is by digitally monitoring your wearers’ behavior, when it comes to changing their garments, by incorporating chips in the garments (for example Berendsen Smart Food tracking system).
7. Use of logos and corporate branding in workwear
In general, workwear in food production should be as clean as possible design-wise, but in food companies with very strong brands, logos on the workwear in production facilities are sometimes required. It is possible to add logos or other forms of visual recognition to workwear without compromising food safety, but there are some considerations that need to be taken into account. For instance, in order to comply with food safety standards, it is often required that the logo should be permanently attached, so it can last as long as the garment’s life cycle. To ensure this, the logo should be sewn on or directly embroidered and not transferred, as this can peel off and potentially cause a risk to production.
Also, some companies wish to add more than just a logo to their workwear by incorporating corporate brand identity through colors or special brand designs. However, this demands specially designed workwear in fabric that still meets food safety requirements, so it may be necessary to acquire bespoke or custom-made workwear.
8. Securing garment cleanliness
Another key consideration when it comes to workwear in the food industry is how you secure the cleanliness of the garment. The higher your production setup is on the risk ladder, the more important this becomes. Looking clean and being clean are two different things, and even the distribution of clean clothes can lead to contamination if not done properly. And in some maximum risk areas the staff might need to change their uniform several times a day e.g. after toilet visits, canteen visits or smoking breaks. By incorporating a chip in the garment, it is possible to have a full overview of workwear usage and, in this way, it can be monitored whether the garment has been washed. Part of choosing the right workwear is also choosing the setup for handling it. Are the employees required to wash their uniforms themselves, do you have an onsite laundry room or will you outsource the cleaning and handling of the garments?
9. Peak seasons and high staff turnover
In some food companies, the employee turnover is high and at times the production is influenced by peak seasons, which means fluctuating numbers of employees, who need to be dressed in the right sizes. This should also be considered when choosing your workwear setup. The rule of thumb is that the higher the turnover and the need for availability of workwear in peak seasons is, the less complex your workwear collection should be, i.e. less variation of garments by using uniforms for instance, which can be used for multiple positions.
10. Future hygiene ambition
Finally, when choosing garments for the food industry, it is important not only to look at your current hygiene ambition, but also to take your future hygiene ambition into consideration. The way you set up and administer your workwear should make you confident that the company will pass audits, not just now but also in the future. Strive to be ahead instead of lagging behind and having to update your setup along the way as new customers appear. A long-term strategy for workwear will help you streamline your hygiene control and secure brand reputation.
- Download Berendsen's new whitepaper
- Nationwide Platforms chooses Elis protective workwear
- Ensure your workwear is fit for purpose
- Fully managed workwear service
- Don't risk safety by washing workwear at home
- Berendsen Workwear: A story of strength and endurance.
- Preventing slips and trips before they happen
- Safety and hygiene all in one place
- New high-visibility workwear collections from Elis UK
- Sustainable workwear - reducing your environmental footprint