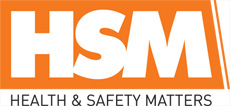
![]() |
Mark Sennett
Managing Editor |
![]() |
Kelly Rose
Editor |
ARTICLE
Dressed to protect
23 January 2013
The recent Gulf of Mexico disaster has brought safety in the oil and gas industry into the spotlight.Calum Squires offers some guidance on specifying and selecting the right products for this hazardous workplace As th

The recent Gulf of Mexico disaster has brought safety in
the oil and gas industry into the spotlight.Calum Squires
offers some guidance on specifying and selecting the right
products for this hazardous workplace
As the investigation into the recent oil rig disaster in the Mexican Gulf continues, questions are being raised about health & safety management in the offshore oil and gas industry. The UK offshore industry currently employs more than 20,000 people, who are exposed to a range of occupational health risks every day, including exposure to a wide range of hazardous substances, radiations, noise, vibration, extremes of heat and cold and ergonomic hazards.
Although accident rates in the UK industry have improved significantly since the Piper Alpha disaster in 1988, the industry remains a hazardous place to work. The main causes of major injuries in 2009/10 were related to slips/trips/falls (26), being trapped or struck by moving objects (11), or injuries associated with lifts/pulls/pushes/handling of loads (5), accounting for 83% of the total.
(www.hse.gov.uk/offshore/statistics/stat09 10.htm). Some accidents and illnesses can be prevented with the proper deployment and use of personal protective equipment (PPE) including clothing, head, arms and feet protection.
The specification and selection of personal protective equipment and clothing can still be a daunting task for those responsible for making the buying decisions. With so many products available, selecting products that are fit for purpose, that are within budge and that ensure the employer is meeting all the legal obligations can seem a daunting task.
In the offshore oil and gas industry key areas for consideration are: safety footwear to prevent injury from heavy objects and accidents from slips and trips; protective clothing for potential exposure to flame, chemicals, extreme weather conditions and high visibility and finally, respiratory protection.
What determines whether protective clothing or equipment is required? A risk assessment, carried out by a competent risk assessor, will identify the requirement for an employer to provide safety equipment as a last line of defence after all other reasonable precautions have been taken. Once safety equipment has been deemed the appropriate option, the resulting risk assessment will advise that for some applications or in some working environments, a certain level of protection must be supplied to employees, contractors and/or visitors, depending on the hazard and the perceived level of risk. It is an employer's legal duty to adhere to the advice on the report and supply appropriate protective equipment, where required, free of charge.
How do I know if a garment or product is fit for purpose? Choosing a garment or product that is fit for purpose may be difficult, depending on the complexity of the job and/or the nature of the working environment. In the case of high visibility clothing for example, the risk assessment report may identify the need for BS EN471 compliant, Class 1, 2 or 3 garments to be supplied to those deemed to be at risk. Class 1 garments offer the lowest level of protection, while Class 3 garments offer the highest level. Specific information on Class requirements is available freely from the HSE and in order to comply with the BS EN471 Standard for high visibility clothing, each garment must carry a CE mark, stating its Class. Couple the requirement for high visibility with protection against chemicals or oils, wet weather or extreme cold, heat exhaustion, or electric shock, the task of selecting a garment or garments that will suit everyone may become even more complicated.
Offshore clothing requirements focus on flame retardant standards EN 11612:2008 and EN 1149 - 5:2008 for Antistatic performance. There is also an electric arc rating standard IEC 61482-2-2009 for specific work relating to electrical switchgear flash hazard protection.
If unsure, advice should be sought from reputable manufacturers and suppliers as well as organisations such as the HSE, the BSIF and the Reflective Equipment Manufacturers Association (REMA).
Chemical protective clothing By definition chemical protective clothing keeps the wearer safe from potential contamination from hazardous materials via the skin in whatever form and concentration it may come: solid particulates, gases, liquids under pressure or not, from low to high concentrations, organic or inorganic chemicals. When selecting appropriate chemical protective clothing, several factors must be taken into account such as the type of task being performed, the nature and concentration of the substance used, but also the best possible balance between protection and comfort to ensure the clothing is worn.
While there are many protective coveralls available on the market, not all of them provide the same level of performance, even if they are certified for the same type of protection.
To assist with the selection of chemical protective clothing, the EU has identified several 'Types' of protection within Category III of the PPE directive. The manufacturer's CE certification to a particular 'Type' offers an indication of the garment's protection against a specific hazard: be it gas, liquid or dust.
Protective clothing 'Types' include: Type 2: Non Gas Tight Protective Clothing; Type 3: Liquid Tight Suits; Type 4: Spray Tight Suits; Type 5: Dry Particle Suits and Type 6: Reduced Spray Suits.
How do I ensure the protective safety garments comply with industry standards? In order to conform to the relevant industry standard and therefore legally comply with workplace health and safety legislation, all workplace safety clothing sold in the UK as personal protective clothing must be CE marked with clear information on the relevant EN standard, Type and Class (where applicable).
Whether your required protection is high visibility, thermal or chemical protection or cut resistance, each type of garment has a dedicated set of European standards to which it must legally conform.
Respiratory protective equipment Approximately 5.5 million workers are exposed to respiratory hazards in the workplace and recent research by both the British Safety Industry Federation (BSIF) and HSE has highlighted concerns that RPE is not being effectively selected, used and maintained in a significant proportion of workplaces where a respiratory hazard exists, leaving workers at risk. When the risk assessment has been completed and all the relevant factors are measured against the correct standards, the employer is able to make an informed decision about the type of RPE required to protect workers in any given situation.
The selection process doesn't end here though because one of the main excuses for workers' reluctance to wear any kind of protective equipment is bad fit. The difference between a correctly fitting face mask and a poorly fitted, leaky and uncomfortable one could mean the difference between life and death. Poor fit testing may affect you, your company and most importantly your staff. It can cause serious long term respiratory problems, you may be wasting your money on ineffective safety products and you may not be compliant with the law.
Consequently legislation actually requires the employer to use a competent fit tester when selecting products for employees to wear.
Arco has supported the BSIF in the development of its recently launched Fit2Fit Accreditation Scheme. Up until now, fit testers of RPE have not been accredited, often making the selection of a 'competent' person a matter of luck and guess work.
Arco is actively encouraging businesses in the offshore oil and gas sector to ensure their workers are fitted with adequate respiratory protection by supporting Clean Air? Take Care!, a joint initiative between the British Safety Industry Federation (BSIF) and the Health and Safety Executive (HSE). The campaign aims to help reduce occupational respiratory disease caused by ineffective use of respiratory protection in the workplace, by raising awareness of the issues that surround it and highlighting the importance of selecting the correct respiratory protective equipment.
Preventing slips, trips and falls According to HSE statistics, accidents as a result of Slips, Trips or Falls are the most common types of accidents across all industry sectors, including offshore oil and gas. Selecting safety footwear is often a difficult issue as comfort is a key factor for the wearer, who could be on their feet all day. If boots or shoes are badly fitting and uncomfortable to wear over long periods then they may be discarded, leaving workers exposed to danger and according to Arco's latest customer research, comfort is the number one criteria when selecting safety boots and shoes.
Arco is now able to offer businesses across all industries a one-stop shop service for risk assessing and managing slips and trips in the workplace. Using an innovative surface testing service that is integrated into the HSE's SAT Slip Assessment Tool, it can now help customers to assess the risk, identify the right footwear solution and provide a choice of high quality, comfortable shoes and boots in order to minimise the risk of slips and trips in the workplace.
Consult an expert To speed up and ease the burden of the PPE selection process and ensure compliance with legislation, it is always beneficial to seek the knowledge, experience and advice of a specialist supplier. With years of experience, expert knowledge of legal requirements and indepth knowledge of a vast range of products, an unbiased safety equipment supplier can collaborate with specialist manufacturers, assess the situation on site and advise on a suitable and compatible range or brand of product.
Partnering with a specialist supplier like Arco, can be beneficial in terms of expert advice, particularly for employers that require a range of PPE types across different applications or sites. In these circumstances, a rationalisation of core products can save money and many manhours each year.
Calum Squires is Arco's regional sales manager for Aberdeen & Highlands. ARCO is on Stand 101 at Health & Safety '10 North
As the investigation into the recent oil rig disaster in the Mexican Gulf continues, questions are being raised about health & safety management in the offshore oil and gas industry. The UK offshore industry currently employs more than 20,000 people, who are exposed to a range of occupational health risks every day, including exposure to a wide range of hazardous substances, radiations, noise, vibration, extremes of heat and cold and ergonomic hazards.
Although accident rates in the UK industry have improved significantly since the Piper Alpha disaster in 1988, the industry remains a hazardous place to work. The main causes of major injuries in 2009/10 were related to slips/trips/falls (26), being trapped or struck by moving objects (11), or injuries associated with lifts/pulls/pushes/handling of loads (5), accounting for 83% of the total.
(www.hse.gov.uk/offshore/statistics/stat09 10.htm). Some accidents and illnesses can be prevented with the proper deployment and use of personal protective equipment (PPE) including clothing, head, arms and feet protection.
The specification and selection of personal protective equipment and clothing can still be a daunting task for those responsible for making the buying decisions. With so many products available, selecting products that are fit for purpose, that are within budge and that ensure the employer is meeting all the legal obligations can seem a daunting task.
In the offshore oil and gas industry key areas for consideration are: safety footwear to prevent injury from heavy objects and accidents from slips and trips; protective clothing for potential exposure to flame, chemicals, extreme weather conditions and high visibility and finally, respiratory protection.
What determines whether protective clothing or equipment is required? A risk assessment, carried out by a competent risk assessor, will identify the requirement for an employer to provide safety equipment as a last line of defence after all other reasonable precautions have been taken. Once safety equipment has been deemed the appropriate option, the resulting risk assessment will advise that for some applications or in some working environments, a certain level of protection must be supplied to employees, contractors and/or visitors, depending on the hazard and the perceived level of risk. It is an employer's legal duty to adhere to the advice on the report and supply appropriate protective equipment, where required, free of charge.
How do I know if a garment or product is fit for purpose? Choosing a garment or product that is fit for purpose may be difficult, depending on the complexity of the job and/or the nature of the working environment. In the case of high visibility clothing for example, the risk assessment report may identify the need for BS EN471 compliant, Class 1, 2 or 3 garments to be supplied to those deemed to be at risk. Class 1 garments offer the lowest level of protection, while Class 3 garments offer the highest level. Specific information on Class requirements is available freely from the HSE and in order to comply with the BS EN471 Standard for high visibility clothing, each garment must carry a CE mark, stating its Class. Couple the requirement for high visibility with protection against chemicals or oils, wet weather or extreme cold, heat exhaustion, or electric shock, the task of selecting a garment or garments that will suit everyone may become even more complicated.
Offshore clothing requirements focus on flame retardant standards EN 11612:2008 and EN 1149 - 5:2008 for Antistatic performance. There is also an electric arc rating standard IEC 61482-2-2009 for specific work relating to electrical switchgear flash hazard protection.
If unsure, advice should be sought from reputable manufacturers and suppliers as well as organisations such as the HSE, the BSIF and the Reflective Equipment Manufacturers Association (REMA).
Chemical protective clothing By definition chemical protective clothing keeps the wearer safe from potential contamination from hazardous materials via the skin in whatever form and concentration it may come: solid particulates, gases, liquids under pressure or not, from low to high concentrations, organic or inorganic chemicals. When selecting appropriate chemical protective clothing, several factors must be taken into account such as the type of task being performed, the nature and concentration of the substance used, but also the best possible balance between protection and comfort to ensure the clothing is worn.
While there are many protective coveralls available on the market, not all of them provide the same level of performance, even if they are certified for the same type of protection.
To assist with the selection of chemical protective clothing, the EU has identified several 'Types' of protection within Category III of the PPE directive. The manufacturer's CE certification to a particular 'Type' offers an indication of the garment's protection against a specific hazard: be it gas, liquid or dust.
Protective clothing 'Types' include: Type 2: Non Gas Tight Protective Clothing; Type 3: Liquid Tight Suits; Type 4: Spray Tight Suits; Type 5: Dry Particle Suits and Type 6: Reduced Spray Suits.
How do I ensure the protective safety garments comply with industry standards? In order to conform to the relevant industry standard and therefore legally comply with workplace health and safety legislation, all workplace safety clothing sold in the UK as personal protective clothing must be CE marked with clear information on the relevant EN standard, Type and Class (where applicable).
Whether your required protection is high visibility, thermal or chemical protection or cut resistance, each type of garment has a dedicated set of European standards to which it must legally conform.
Respiratory protective equipment Approximately 5.5 million workers are exposed to respiratory hazards in the workplace and recent research by both the British Safety Industry Federation (BSIF) and HSE has highlighted concerns that RPE is not being effectively selected, used and maintained in a significant proportion of workplaces where a respiratory hazard exists, leaving workers at risk. When the risk assessment has been completed and all the relevant factors are measured against the correct standards, the employer is able to make an informed decision about the type of RPE required to protect workers in any given situation.
The selection process doesn't end here though because one of the main excuses for workers' reluctance to wear any kind of protective equipment is bad fit. The difference between a correctly fitting face mask and a poorly fitted, leaky and uncomfortable one could mean the difference between life and death. Poor fit testing may affect you, your company and most importantly your staff. It can cause serious long term respiratory problems, you may be wasting your money on ineffective safety products and you may not be compliant with the law.
Consequently legislation actually requires the employer to use a competent fit tester when selecting products for employees to wear.
Arco has supported the BSIF in the development of its recently launched Fit2Fit Accreditation Scheme. Up until now, fit testers of RPE have not been accredited, often making the selection of a 'competent' person a matter of luck and guess work.
Arco is actively encouraging businesses in the offshore oil and gas sector to ensure their workers are fitted with adequate respiratory protection by supporting Clean Air? Take Care!, a joint initiative between the British Safety Industry Federation (BSIF) and the Health and Safety Executive (HSE). The campaign aims to help reduce occupational respiratory disease caused by ineffective use of respiratory protection in the workplace, by raising awareness of the issues that surround it and highlighting the importance of selecting the correct respiratory protective equipment.
Preventing slips, trips and falls According to HSE statistics, accidents as a result of Slips, Trips or Falls are the most common types of accidents across all industry sectors, including offshore oil and gas. Selecting safety footwear is often a difficult issue as comfort is a key factor for the wearer, who could be on their feet all day. If boots or shoes are badly fitting and uncomfortable to wear over long periods then they may be discarded, leaving workers exposed to danger and according to Arco's latest customer research, comfort is the number one criteria when selecting safety boots and shoes.
Arco is now able to offer businesses across all industries a one-stop shop service for risk assessing and managing slips and trips in the workplace. Using an innovative surface testing service that is integrated into the HSE's SAT Slip Assessment Tool, it can now help customers to assess the risk, identify the right footwear solution and provide a choice of high quality, comfortable shoes and boots in order to minimise the risk of slips and trips in the workplace.
Consult an expert To speed up and ease the burden of the PPE selection process and ensure compliance with legislation, it is always beneficial to seek the knowledge, experience and advice of a specialist supplier. With years of experience, expert knowledge of legal requirements and indepth knowledge of a vast range of products, an unbiased safety equipment supplier can collaborate with specialist manufacturers, assess the situation on site and advise on a suitable and compatible range or brand of product.
Partnering with a specialist supplier like Arco, can be beneficial in terms of expert advice, particularly for employers that require a range of PPE types across different applications or sites. In these circumstances, a rationalisation of core products can save money and many manhours each year.
Calum Squires is Arco's regional sales manager for Aberdeen & Highlands. ARCO is on Stand 101 at Health & Safety '10 North
MORE FROM THIS COMPANY
OTHER ARTICLES IN THIS SECTION