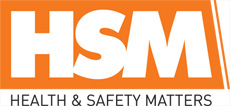
![]() |
Mark Sennett
Managing Editor |
![]() |
Kelly Rose
Editor |
Home> | Plant & Machinery | >Safety Light Curtains | >When were your light curtains tested? |
When were your light curtains tested?
31 May 2017
Light curtains are commonplace in today’s manufacturing and packaging facilities. They fall into the category of ESPE (Electro Sensitive Protective Equipment). They use AOPD (Active Opto-electronic Protection Devices) for safeguarding persons when interacting with machinery.

From an operator safety point of view, their primary function is to protect people from contact with moving hazardous parts of machinery. Along with physical guarding, light curtains and other ESPE are regarded as primary safety devices. Suitable applications are many and varied from trip devices (such as manually loaded and unloaded hydraulic presses) to human presence sensing at the conveyor infeed and outfeed to hazardous machinery.
Light curtains can be specified with different resolutions i.e. the distance between successive beams. The selected resolution has an effect on the minimum safety distance allowed between the light curtain and the hazardous moving part(s) i.e. the higher the resolution, the smaller the safety distance required to the hazard.
In order to validate that the light curtain is positioned at an adequate distance from the nearest hazardous moving part, a suitable stop time performance test needs to be carried out. The test provides an accurate measurement of the overall stopping time of the machine from detection of the light curtain to the point of where the hazardous moving part(s) has come to a standstill condition.
Throughout industry, there are many existing installations where theoretical calculations or suitable testing has never been carried out. Others have had light curtain positions set using the theoretical calculations only. A relatively small number of applications are supported by testing and documented results when the machinery/installation was commissioned (new machinery).
The typical lifespan of machinery can be 10, 20 or 30+ years in service. Mechanical parts wear, machine speeds can be increased and energy sources (such as pneumatic supplies) can fluctuate or be adjusted throughout this time. These variations have an effect on the stopping time of the machine. What was an adequate safety distance when the machine was first installed may not be adequate today!
HSG 180 (free to download from HSE Books) provides guidance on the application of electro-sensitive protection equipment using light curtains and light beam devices to machinery. It provides the equation for calculating the theoretical safety distance required (as found in EN ISO 13855:2010).
There is also an ‘Inspection and test’ section in the guide that, in accordance with PUWER, there is a requirement to not only carry out an initial inspection and test of the ESPE, but also periodic inspection and test throughout the lifetime of the machinery.
If suitable arrangements are not in place and an incident occurs, there is a risk that the employer could face charges for breaching a number of PUWER regulations, in particular Regulation 6 and Regulation 11.
If you have any questions or concerns regarding your current status, Pilz has a team of professional and competent engineers that can provide informed, pragmatic advice and deliver suitable testing of your ESPE, so that you have peace of mind and the relevant evidence available at your fingertips.