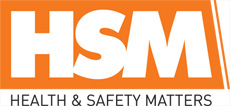
![]() |
Mark Sennett
Managing Editor |
![]() |
Kelly Rose
Editor |
Is an ‘old friend’ compromising your workers’ safety?
18 November 2015
Dr Martin Kidman, safety specialist for Sick UK, looks at the pros and cons of one of the most basic safety devices - safety mats - and asks when is it right to consider a change?
For more than half a century, safety mats have been the ever-present ‘old faithful’ of virtually every industrial environment – a universal standard form of safety protection for workers.
But, as technology costs have plummeted and factory safety control systems have become more complex, the choice of replacing a safety mat with a safety laser scanner has become an affordable option. Not only is a laser scanner justifiable in terms of cost, it may offer additional benefits.
In many small works and machine shops up and down the land, workers are protected from hazardous processes such as stamping, cutting and pressing with the simple safety mat. You stand on it and the machine stops. From garages to packaging firms, finishers to printers this simple, old friend is taken for granted.
Simple? Yes. Dependable? Hopefully. Safe? Maybe. Good value? Now very debatable – especially if you measure value in terms of employee safety. In fact, a laser scanner may cost less than two mats. Changing to laser technology could have additional benefits too, be easy to use and ensure compliance with the latest machine safety directives.
Stepping on it
Typically, safety mats operate using an open switch which responds to compression via a transducer that sends a signal to a controller connected to the machine being guarded. Pressure on the mat completes a circuit which stops the machine safely and may also trigger an alarm.
One of the biggest issues with safety mats is that they stop working properly because people repeatedly step on them - after all, that’s what they’re designed to do. The compressive resilience of the mat changes with age and use, becoming inherently less safe. Worn or old mats may not compress enough except under ever increasing loads and the insulating materials degrade causing false alarms.
The reliability of the mat can be damaged by heavy items such as forklifts, trolleys, loaded pallets, and stillages. Punctures can allow fluids such as hydraulic oils or chemicals to compromise safety.
All this leads to downtime, frequent replacement and growing uncertainty of the risks involved. The latest machine safety directives concentrate on speed of response of a safety device compared with the distance moved by an operative. If the mat response is uncertain can you be sure the machine will stop quickly enough to prevent a moving limb from getting into the danger zone?
Time of flight measurement
With nearly 20 years of successful use already under its belt, the safety laser scanner is a small, all-in-one device, with very precise and easily programmable operation.
The principle of operation is simple, comprising a pulsed laser beam that reflects if it meets an object and the reflection is registered by a receiver. The difference in time between emitting and receiving the reflected signal is measured by the software in the scanner. Pulses are emitted and received at the rate of 100 – 200 per second depending on model, so detection of movement is very rapid.
If the time of the reflected pulse is shorter than a set level, i.e. the object is too close, a command signal goes to the machine controller to issue an alarm, or shut it down. Time-of-flight measurement is used in millions of laser devices all around the world.
An internal rotating mirror deflects the pulsed laser beam so that a fan-shaped scan is made of the surrounding area. So, not only is the safe distance set, the field of coverage can be set as a segment of a sphere – up to 270° around - and also from the ground upwards.
Safety laser scanners can define protective and warning fields, also referred to as zones or areas. These zones are freely programmable and can be changed easily by authorised personnel. By having warning fields machine down time can be reduced significantly, because an approaching person can be warned by an audible or visible alarm before the machine needs to be stopped.
Fail safe
Laser safety scanners are reliable and durable. They will not wear out with use in the same way as a mat would do and, as a non-contact technology mounted above the ground, they are less likely to be damaged. A laser scanner is a fail-safe device not subject to gradual deterioration; it either works or doesn’t.
If a mat fails because of physical contact, a machine will likely have to be shut down, depending on a company’s internal processes and procedures regarding safeguarding. This shut down will remain in effect until the safety mat is replaced by one in stock or another is shipped and mounted. This process takes time and disrupts production, in addition to incurring capital costs. Laser safety scanners are not subject to this risk.
Because safety mats are not "one-size fits all” a range of mat sizes need to be carried in stock for different machines and floor plans to avoid extended downtime. If a new machine configuration is introduced, the previous mat may not fit the safety area and could even need to be custom-fitted.
Replacing a mat is likely to mean replacing the controller too and this could result in compatibility problems.
With a safety laser scanner, the scanning field can be configured to whatever is required. Static obstructions like walls or pillars can be swiftly taught-in and the same scanner is easy to reconfigure whenever a change is made.
If the device is damaged, it is frequently only the scanner head that needs changing; a simple plug-in replacement. The safety settings are retained in the system plug memory and are automatically downloaded to the new scanning head.
Few exceptions
Are there some times when lasers are still not the best choice? Some. Although the safety laser scanner is designed for reliable operation in challenging environments where there is extreme dirt or heavy moisture. Leaking oil, grease or dust can cause the laser scanners to trip in some circumstances.
However, manufacturers like Sick are constantly improving the technology to make laser scanners highly reliable even in the most challenging environments. They can be IP67/69 protected and can be programmed with advanced algorithms to compensate to a large degree for particles, spray and even snow, although response times will be degraded.
As laser safety scanning technology becomes accessible and universal, the argument for change gets ever stronger. There may a few applications where a simple step-on mat is a better choice, but this is likely to be only in extreme conditions where a safety mat will still need frequent replacement.
Perhaps it is time to consider making the change? If you are still unsure, manufacturers like Sick have vast experience in design, development and application of laser sensing and machinery safety technologies. A call to expert advisers can help to answer any questions.