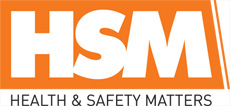
![]() |
Mark Sennett
Managing Editor |
![]() |
Kelly Rose
Editor |
Home> | Handling & Storing | >Safer Manual Handling | >Reduced manual handling for safer battery management |
ARTICLE
Reduced manual handling for safer battery management
28 October 2014
Batteries for lift trucks and other motive power applications are usually chosen on the basis of their performance and whole life costs but for many operators an increasingly important factor is the safe handling of their power sources. Making the right choices can help improve sustainability and health and safety compliance.
In the past, installations where battery changes were necessary often used some kind of crane to lift the battery from the truck or vehicle before a fully-charged unit was lowered back in. Progress in truck and battery design made by OEM and battery manufacturers means there is no longer any need to do this. Many vehicles now incorporate a battery compartment with side access and rollers in the floor while charging facilities are configured with battery beds at the same height. The truck drives alongside a charging position and, using a battery changing cart, the depleted battery is rolled out and a fully charged unit rolled back in.
There is no need for any lifting and minimal effort is needed to push the battery in and out of position. This simple system is popular for pallet handlers, low-level order pickers and similar trucks with relatively small batteries. For larger vehicles such as reach and counterbalance trucks or high-level order pickers and because of battery weight and dimensions, the battery change cart can incorporate mechanical assistance such as magnet arm extraction to move the battery in and out of position.
For large numbers of battery changes, another option is to use special change carts that are designed as operator ride on battery changers. Sometimes known as "Battery Bulls” these devices incorporate driven rollers and an electro-magnetic extraction arm and operated together pushes and pulls the batteries to and from the charging station and on and off the truck. These offer additional flexibility and versatility by providing a safe battery change operation, speeding up battery change and increasing truck up times.
In the most advanced facilities there is no longer any need to keep batteries at ground level. Instead, charging stations can be arranged on two, three or even four levels to minimise the footprint and make much better use of the available space. The Co-operative Group was the first operator to utilise four-high charging installations in the UK and has continued to invest in the technology at the majority of its new-build distribution centre projects.
While optimising available space and freeing resources for productive use is often the biggest driver for such installations there are other benefits. In particular, they minimise truck movements and time spent in charging areas which is safer for operators, pedestrians and bystanders. In a typical installation the charging stations are arranged along aisles with the outer face towards the truck operating area. The inner face is configured for pedestrian access which removes potential points of contact between moving trucks and staff responsible for managing the installation. Routine battery checks and maintenance can be carried out safely while normal warehouse operations continue.
Another safety consideration is the albeit small risk of arcing during disconnection or connection when swapping batteries. Advanced chargers such as the Hawker LifeIQ range from EnerSys incorporate circuitry and programmable features that minimise this risk. Although arcing is undesirable at any time it can present an increased risk in confined areas because hydrogen is produced during the normal charging of conventional batteries. Charging areas often incorporate ventilation systems to remove any gasses produced but these can be uneconomic in smaller warehouses or when charging stations are dispersed throughout a large site. Under these circumstances batteries which offer "low gassing” can represent an ideal alternative.
Finally, although by no means the most arduous operation in the warehouse, battery topping often requires the lifting and handling of water bottles and other equipment. Automated filling equipment removes many of the risks by eliminating the need for any manual handling and lifting. As an alternative, the latest-generation batteries with gel electrolytes require little or no topping. The main benefit is improved and consistent battery and truck performance but the reduction in handling risks may be a consideration for some operators.
MORE FROM THIS COMPANY
OTHER ARTICLES IN THIS SECTION