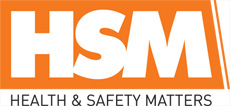
![]() |
Mark Sennett
Managing Editor |
![]() |
Kelly Rose
Editor |
Home> | Handling & Storing | >Safer Manual Handling | >Handling it well |
ARTICLE
Handling it well
23 January 2013
More than a third of over-three-day injuries reported are caused by manual handling activities.Nasar Farooq considers employers obligations in this area The Manual Handling Operations Regulations, implemented in 1

More than a third of over-three-day injuries reported are
caused by manual handling activities.Nasar Farooq
considers employers obligations in this area
The Manual Handling Operations Regulations, implemented in 1992 (amended in 2002) apply to a variety of activities, including lifting, lowering, pushing, pulling and carrying a load (an inanimate object - box or trolley, or animate object - person or animal).
Under the regulations, so far as is reasonably practicable, an employer must avoid the need for hazardous manual handling operations. Where a hazardous operation can't be avoided, a thorough assessment must be undertaken and measures introduced to either avoid the risk or reduce it to the lowest possible level.
What do employers need to do to comply with these regulations? Identify the risks, consult and inspect - Employers need to identify all manual handling activities undertaken that may pose a risk of injury, referring to a generic risk assessment of work activities, they must also consult with employees and carry out workplace inspections.
Avoid the need - A manual handling activity that represents a significant risk should be avoided where possible.
Employers should: Check whether the material needs to be moved - can an activity be done from where the item is located? Consider automation, mechanisation and using handling aids such as a conveyor or electric hoist.
Beware of new hazards introduced from automation or mechanisations - e.g. an automated plant needs cleaning and maintenance, and lift trucks should have properly trained operators.
Assess the risk of injury If a manual handling activity cannot be avoided, a preliminary risk assessment should be carried out to determine which activities involve a significant risk of injury and therefore warrant a full risk assessment.
Once identified, activities must then be evaluated to determine those that present a significant risk.
The HSE provides a risk assessment guideline filter which gives numerical values of loads above which a risk may exist - approx 25kg for men and 17kg for women. Applying these guidelines provides a reasonable level of protection to around 95 per cent of working men and women, but it's important to note the HSE figures are suggested guidelines and should only be used as a tool for determining which operations are risky.
Other factors to consider include whether the handler twists to the side during the operation. If so, guideline figures should be reduced by about 10% if twisting beyond 45 degrees, and 20% if twisting beyond 90 degrees. The guidelines are also only recommended for infrequent lifting and should be reduced for employees undertaking over 30 manual handling operations an hour.
Once activities that pose a significant risk are identified, employers should undertake a full risk assessment, looking at the complete manual handling operation and anticipating reasonably foreseeable factors.
It should take into account the task, the load, the environment in which the activity takes place and the individual's capabilities.
The assessment must be carried out by a competent person who has an understanding of the regulations, knowledge of the operations, judgement of what constitutes a risk and ability to recommend reasonably practicable solutions.
Any significant findings should be recorded and stored in an accessible place, except when the risks are proved to be insignificant, the assessment is simple and easily repeatable, and the handling operations are low risk, only lasting for a short period of time.
Reduce the risk Following the completion of the manual handling risk assessment, the employer must introduce suitable risk control measures to reduce the risk of injury to as low as possible. Employers should also regularly monitor their processes to ensure the effectiveness of risk reduction measures, and re-assessment must be carried out where necessary.
Staff training Employers should also train their staff, making them aware of their duties and responsibilities and of the hazards associated with manual handling operations, as well as control measures to avoid or reduce these risks. It should cover: The risks associated with manual handling activities The principles of correct handling, a safe system of work and the use of any risk reduction measures provided by the employer Precise information on the nature of the load to be handled, including weight, centre of gravity and so on Training is important but it's not enough on its own and cannot overcome a lack of mechanical aids, the handling of unsuitable loads, or poor working conditions. Employers should look to take a proactive approach with employees, talking to them informally about their tasks and discussing whether improvements could be made.
Employee duties Employees also have a duty to take reasonable care of their own health & safety. Employees are required to follow appropriate systems of work laid down for their safety and make full proper use of any equipment intended to reduce the risk of injury from manual handling activities.
They are required to co-operate with their employer on health and safety matters, informing them if they identify hazardous activities and taking care to ensure their activities don't put others at risk.
Nasar Farooq is health & safety technical manager at Croner, part of Wolters Kluwer
Top Tips for Safe Handling Stop and think - Never lift beyond your capability and if in doubt get some help Avoid the lift - Ask yourself, is it necessary to manually lift the load? Can it be avoided and can mechanical aids be used? Assess the load - What is the weight? What is its shape and size? Is the heaviest side closest to your body? Plan the task - Assess your route. Is it clear? Do doors need opening? Is the route level and what's the lighting like? Team work - Do you need help with the load and who's around to give you instructions? Personal protective equipment - Do you need gloves, protective footwear or clothing? Information - Has the activity been risk assessed? Have you been given training to lift the load or sought guidance from management?
The Manual Handling Operations Regulations, implemented in 1992 (amended in 2002) apply to a variety of activities, including lifting, lowering, pushing, pulling and carrying a load (an inanimate object - box or trolley, or animate object - person or animal).
Under the regulations, so far as is reasonably practicable, an employer must avoid the need for hazardous manual handling operations. Where a hazardous operation can't be avoided, a thorough assessment must be undertaken and measures introduced to either avoid the risk or reduce it to the lowest possible level.
What do employers need to do to comply with these regulations? Identify the risks, consult and inspect - Employers need to identify all manual handling activities undertaken that may pose a risk of injury, referring to a generic risk assessment of work activities, they must also consult with employees and carry out workplace inspections.
Avoid the need - A manual handling activity that represents a significant risk should be avoided where possible.
Employers should: Check whether the material needs to be moved - can an activity be done from where the item is located? Consider automation, mechanisation and using handling aids such as a conveyor or electric hoist.
Beware of new hazards introduced from automation or mechanisations - e.g. an automated plant needs cleaning and maintenance, and lift trucks should have properly trained operators.
Assess the risk of injury If a manual handling activity cannot be avoided, a preliminary risk assessment should be carried out to determine which activities involve a significant risk of injury and therefore warrant a full risk assessment.
Once identified, activities must then be evaluated to determine those that present a significant risk.
The HSE provides a risk assessment guideline filter which gives numerical values of loads above which a risk may exist - approx 25kg for men and 17kg for women. Applying these guidelines provides a reasonable level of protection to around 95 per cent of working men and women, but it's important to note the HSE figures are suggested guidelines and should only be used as a tool for determining which operations are risky.
Other factors to consider include whether the handler twists to the side during the operation. If so, guideline figures should be reduced by about 10% if twisting beyond 45 degrees, and 20% if twisting beyond 90 degrees. The guidelines are also only recommended for infrequent lifting and should be reduced for employees undertaking over 30 manual handling operations an hour.
Once activities that pose a significant risk are identified, employers should undertake a full risk assessment, looking at the complete manual handling operation and anticipating reasonably foreseeable factors.
It should take into account the task, the load, the environment in which the activity takes place and the individual's capabilities.
The assessment must be carried out by a competent person who has an understanding of the regulations, knowledge of the operations, judgement of what constitutes a risk and ability to recommend reasonably practicable solutions.
Any significant findings should be recorded and stored in an accessible place, except when the risks are proved to be insignificant, the assessment is simple and easily repeatable, and the handling operations are low risk, only lasting for a short period of time.
Reduce the risk Following the completion of the manual handling risk assessment, the employer must introduce suitable risk control measures to reduce the risk of injury to as low as possible. Employers should also regularly monitor their processes to ensure the effectiveness of risk reduction measures, and re-assessment must be carried out where necessary.
Staff training Employers should also train their staff, making them aware of their duties and responsibilities and of the hazards associated with manual handling operations, as well as control measures to avoid or reduce these risks. It should cover: The risks associated with manual handling activities The principles of correct handling, a safe system of work and the use of any risk reduction measures provided by the employer Precise information on the nature of the load to be handled, including weight, centre of gravity and so on Training is important but it's not enough on its own and cannot overcome a lack of mechanical aids, the handling of unsuitable loads, or poor working conditions. Employers should look to take a proactive approach with employees, talking to them informally about their tasks and discussing whether improvements could be made.
Employee duties Employees also have a duty to take reasonable care of their own health & safety. Employees are required to follow appropriate systems of work laid down for their safety and make full proper use of any equipment intended to reduce the risk of injury from manual handling activities.
They are required to co-operate with their employer on health and safety matters, informing them if they identify hazardous activities and taking care to ensure their activities don't put others at risk.
Nasar Farooq is health & safety technical manager at Croner, part of Wolters Kluwer
Top Tips for Safe Handling Stop and think - Never lift beyond your capability and if in doubt get some help Avoid the lift - Ask yourself, is it necessary to manually lift the load? Can it be avoided and can mechanical aids be used? Assess the load - What is the weight? What is its shape and size? Is the heaviest side closest to your body? Plan the task - Assess your route. Is it clear? Do doors need opening? Is the route level and what's the lighting like? Team work - Do you need help with the load and who's around to give you instructions? Personal protective equipment - Do you need gloves, protective footwear or clothing? Information - Has the activity been risk assessed? Have you been given training to lift the load or sought guidance from management?
MORE FROM THIS COMPANY
OTHER ARTICLES IN THIS SECTION