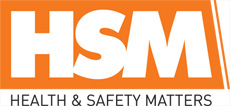
![]() |
Mark Sennett
Managing Editor |
![]() |
Kelly Rose
Editor |
Home> | Plant & Machinery | >General Plant & Machinery | >Shedding UV light on the problem |
ARTICLE
Shedding UV light on the problem
23 January 2013
Repairing sewers by no-dig methods is quicker and less disruptive than excavation. During a recent £1.7m project for Severn Trent Water (STW) to repair 2500m of sewers in the historic spa town of Buxton, UV light tec

Repairing sewers by no-dig
methods is quicker and less
disruptive than excavation.
During a recent £1.7m project for Severn Trent Water (STW) to repair 2500m of sewers in the historic spa town of Buxton, UV light technology from Lanes allowed the company to renovate pipes in a particularly short timeframe.
Lee Bow, Lanes project manager explains: "Using UV light we can cure a liner at, typically, one metre a minute compared to an average 8- to 12-hours to cure a liner with hot water. That meant we could reduce the installation 'window' for each liner greatly.
"There are other savings too. For instance, the fibreglass matting liners are preimpregnated with polyester resin so there is no wet-out process, nor a need to keep liners refrigerated; there are no scaffold towers to be erected and dismantled, no water boilers and no fleet of vehicles — a single unit carries all the equipment for each install, with the liner simply stored in a wooden crate and positioned by the access point. And of course there is no contaminated wastewater to be disposed of afterwards. All of this considerably lessens the carbon footprint." The UV process is straight - forward. A camera unit is dispatched through the pipe with a nylon pull-cord attached. This brings back the steel winch line, which in turn allows the liner to be drawn through the pipe, before end elements are fitted.
During a recent £1.7m project for Severn Trent Water (STW) to repair 2500m of sewers in the historic spa town of Buxton, UV light technology from Lanes allowed the company to renovate pipes in a particularly short timeframe.
Lee Bow, Lanes project manager explains: "Using UV light we can cure a liner at, typically, one metre a minute compared to an average 8- to 12-hours to cure a liner with hot water. That meant we could reduce the installation 'window' for each liner greatly.
"There are other savings too. For instance, the fibreglass matting liners are preimpregnated with polyester resin so there is no wet-out process, nor a need to keep liners refrigerated; there are no scaffold towers to be erected and dismantled, no water boilers and no fleet of vehicles — a single unit carries all the equipment for each install, with the liner simply stored in a wooden crate and positioned by the access point. And of course there is no contaminated wastewater to be disposed of afterwards. All of this considerably lessens the carbon footprint." The UV process is straight - forward. A camera unit is dispatched through the pipe with a nylon pull-cord attached. This brings back the steel winch line, which in turn allows the liner to be drawn through the pipe, before end elements are fitted.
MORE FROM THIS COMPANY
- Transport fleet accreditation success
- Innovation reaps rewards
- Helping TRiM mental stress in water utility industry
- Company shows it cares with feeling app
- Drainage jobs website
- Lanes wins seal of approval
- Drainage maintenance
- Strop improves railway work at height
- Fast response
- City & Guilds auditors praise unique drainage course
OTHER ARTICLES IN THIS SECTION