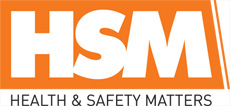
![]() |
Mark Sennett
Managing Editor |
![]() |
Kelly Rose
Editor |
Home> | Slips, Trips & Falls | >Fall Prevention | >Don't fall behind with fall protection inspection |
ARTICLE
Don't fall behind with fall protection inspection
23 January 2013
John Boyle looks at how keeping a building's fall protection systems fully tested and inspected is an essential part of minimising risks to workers on roofs and external facades It is a well known fact that too many a
John Boyle looks at how keeping a building's fall protection
systems fully tested and inspected is an essential part of
minimising risks to workers on roofs and external facades
It is a well known fact that too many accidents come about as a result of falls from heights. Figures from the HSE show that there are still around 4,000 serious injuries each year from work at heights, with falls from height still the largest reportable cause of fatalities in the workplace, as reported in RIDDOR (Report of Injuries, Diseases and Dangerous Occurrences Regulations).
Health & safety managers are well aware of their role in taking care not only of the internal workings of a building, but also the external façade - and this includes the protection of workers when carrying out cleaning or essential maintenance to roofs and walls.
The Work at Height Regulations 2005 have gone a long way to reinforce the importance of the protection of workers and the introduction of the Corporate Manslaughter Act in 2008 further emphasised the need for businesses to minimise their risks and provide greater protection to workers.
So what can be done to minimise the risks? The regular testing and inspection of fall protection systems is now an integral part of many companies' planned maintenance programmes. For multi-site health & safety managers, it is important to plan a dedicated inspection regime and how this should work.
Working with specialists in this area, like Eurosafe Solutions, provides peace of mind and is an option preferred by many health & safety managers as it means the external company takes responsibility for managing the whole maintenance schedule for one or a whole portfolio of buildings. This ensures that all testing is carried out on a planned basis to provide optimum protection.
Safe working order It is important to remember that safety devices installed to protect workers when working at heights need their own maintenance programme to ensure they remain safe and in good working order.
UK legislation states that cable-based fall protection systems should be tested at least every 12 months, as should PPE associated with work at heights and eyebolts on roofs.
Furthermore, Abseil anchors should be tested every six months, as part of meeting Work at Height legislation, including BS 3N 365, BS EN 795 and BS EN 7883. These are the set rules for testing and inspection, but frequency of inspection varies from product to product, so it is worth checking this with the manufacturer.
The Hierarchy of Risk Management separates fall protection systems into three categories: Eliminate the risk of a fall Collective protection Individual protection The safest method of fall protection is obviously to eliminate the risk, which means removing the need to work at height, however this is often unavoidable.
Staff training Training of staff is essential to ensure that everyone involved in the work is competent. The training should reduce the risk of a fall occurring and it should ensure that those who work at height are aware of how to avoid falling and how to minimise injury or risks to anyone who should fall. It is advisable that relevant staff undertake personal protective equipment (PPE) inspection training to ensure that protective equipment is worn correctly. With PPE it is definitely not a case of "one size fits all" and ensuring that PPE suits the heights and build of the individuals who regularly use the kit is important.
Once testing and inspection of fall protection systems has been carried out, a detailed inspection report should be provided which would highlight any potentially hazardous areas and any remedial action that needed to be taken.
The report should also contain an accurate assessment of the safety of the roof systems and identify if any maintenance or replacement work needs to be done. It should also provide up to date system certification that is valid for 12 months.
Whatever the fall protection method in place on a building, one thing is certain; that system will require an ongoing planned maintenance programme. Failure for this to be carried out by an experienced fall protection professional could lead to a lack of duty of care on the part of the company.
By working closely with health & safety managers to provide these services on one or a whole portfolio of buildings, we can create a system where risks are minimised, workers are offered best protection and fall protection systems are compliant with all relevant regulatory standards.
John Boyle is a director at Eurosafe Solutions.
It is a well known fact that too many accidents come about as a result of falls from heights. Figures from the HSE show that there are still around 4,000 serious injuries each year from work at heights, with falls from height still the largest reportable cause of fatalities in the workplace, as reported in RIDDOR (Report of Injuries, Diseases and Dangerous Occurrences Regulations).
Health & safety managers are well aware of their role in taking care not only of the internal workings of a building, but also the external façade - and this includes the protection of workers when carrying out cleaning or essential maintenance to roofs and walls.
The Work at Height Regulations 2005 have gone a long way to reinforce the importance of the protection of workers and the introduction of the Corporate Manslaughter Act in 2008 further emphasised the need for businesses to minimise their risks and provide greater protection to workers.
So what can be done to minimise the risks? The regular testing and inspection of fall protection systems is now an integral part of many companies' planned maintenance programmes. For multi-site health & safety managers, it is important to plan a dedicated inspection regime and how this should work.
Working with specialists in this area, like Eurosafe Solutions, provides peace of mind and is an option preferred by many health & safety managers as it means the external company takes responsibility for managing the whole maintenance schedule for one or a whole portfolio of buildings. This ensures that all testing is carried out on a planned basis to provide optimum protection.
Safe working order It is important to remember that safety devices installed to protect workers when working at heights need their own maintenance programme to ensure they remain safe and in good working order.
UK legislation states that cable-based fall protection systems should be tested at least every 12 months, as should PPE associated with work at heights and eyebolts on roofs.
Furthermore, Abseil anchors should be tested every six months, as part of meeting Work at Height legislation, including BS 3N 365, BS EN 795 and BS EN 7883. These are the set rules for testing and inspection, but frequency of inspection varies from product to product, so it is worth checking this with the manufacturer.
The Hierarchy of Risk Management separates fall protection systems into three categories: Eliminate the risk of a fall Collective protection Individual protection The safest method of fall protection is obviously to eliminate the risk, which means removing the need to work at height, however this is often unavoidable.
Staff training Training of staff is essential to ensure that everyone involved in the work is competent. The training should reduce the risk of a fall occurring and it should ensure that those who work at height are aware of how to avoid falling and how to minimise injury or risks to anyone who should fall. It is advisable that relevant staff undertake personal protective equipment (PPE) inspection training to ensure that protective equipment is worn correctly. With PPE it is definitely not a case of "one size fits all" and ensuring that PPE suits the heights and build of the individuals who regularly use the kit is important.
Once testing and inspection of fall protection systems has been carried out, a detailed inspection report should be provided which would highlight any potentially hazardous areas and any remedial action that needed to be taken.
The report should also contain an accurate assessment of the safety of the roof systems and identify if any maintenance or replacement work needs to be done. It should also provide up to date system certification that is valid for 12 months.
Whatever the fall protection method in place on a building, one thing is certain; that system will require an ongoing planned maintenance programme. Failure for this to be carried out by an experienced fall protection professional could lead to a lack of duty of care on the part of the company.
By working closely with health & safety managers to provide these services on one or a whole portfolio of buildings, we can create a system where risks are minimised, workers are offered best protection and fall protection systems are compliant with all relevant regulatory standards.
John Boyle is a director at Eurosafe Solutions.
MORE FROM THIS COMPANY
OTHER ARTICLES IN THIS SECTION