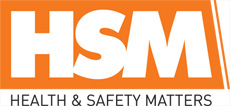
![]() |
Mark Sennett
Managing Editor |
![]() |
Kelly Rose
Editor |
Home> | Training & Development | >Conferences/ Seminars | >Forklift training:Where are your blind spots? |
ARTICLE
Forklift training:Where are your blind spots?
23 January 2013
Richard Shore, of materials handling training provider, Mentor Training,warns of some common oversights when arranging forklift traini Despite recent improvements, forklift trucks remain statistically the most danger

Richard Shore, of materials handling training provider,
Mentor Training,warns of some common oversights
when arranging forklift traini
Despite recent improvements, forklift trucks remain statistically the most dangerous type of transport in the workplace.
The past five years alone have seen UK forklifts involved in more than 9,000 three-day injuries in addition to over 2,500 hospitalisations and, tragically, 50 fatalities.
Forklift trucks are large, powerful and heavy - frequently with low-visibility "blind spots" when laden - and, as any health and safety professional will know, employers have a legal duty to ensure workers operating such potentially hazardous equipment are properly trained.
Regulation 9 of the Provision and Use of Work Equipment Regulations 1998 (PUWER 98) states: "Every employer shall ensure that all persons who use work equipment have received adequate training for purposes of health and safety, including training in the methods which may be adopted when using the work equipment, any risks which such use may entail and precautions to be taken." This legal requirement for training complements a powerful business case for avoiding damage to goods, buildings and reputation, not to mention lost time and legal costs - plus, of course, the moral duty to protect employees.
However in practice, there are common oversights that occur in companies' forklift training arrangements. Just like with forklifts themselves, these "blind spots" can jeopardise safety unless addressed.
Temporary workers A temporary operator, even if they're only on your premises for a matter of days, requires the same safeguards as any permanent employee - including the requirement for training - under PUWER 98. This becomes more complicated when operators claim prior experience and training. Section 30 of the L117 Approved Code of Practice for Rider Operated Lift Trucks is clear: "Where employees claim to be trained and experienced, employers should insist upon evidence. Employers need to satisfy themselves that the training, experience and ability is in fact sufficient and relevant to the lift trucks and handling attachments to be used." Worryingly, a recent survey by the FLTA found 85% of recruitment advertisements for forklift operators required a "forklift licence" - when in fact there is no such document in the UK.
Where there is any doubt about a potential operator's experience with your equipment, environment and task, it is good practice - and good sense - to arrange a skills assessment.
Hand pallet trucks Because hand pallet trucks are not "driven", and do not have a lifting or stacking capability, they are often overlooked when it comes to training - or taken too lightly by employees.
However, they are as much subject to PUWER 98 as any other kind of equipment, and can do permanent damage to feet, ankles and lower legs if used inappropriately.
Adequate cover Don't forget, you need sufficient trained operators to cover holidays, unplanned absences like sickness, sudden surges in workload and, hopefully, future business expansion.
A surprising number of employers train operators, but find themselves caught out - and under pressure to take a major risk - because of a need to move a load at short notice, with no qualified staff available.
Colleagues working nearby An estimated two thirds of UK forklift accident victims are not the operator but a colleague on foot, in the wrong place at the wrong time. That's at least four pedestrians injured or killed by forklift trucks per day.
It's deceptively easy for an untrained colleague to assume a forklift operator has seen them when they're actually in a blind spot, or not to understand the danger zones caused by rear-wheel steer.
For this reason, independent advice from the FLTA strongly recommends that all staff who work near forklift trucks are at least trained in the risks involved and how to avoid them.
What about you? Another part of PUWER 98, Regulation 9, says: "Every employer shall ensure that any of its employees who supervises or manages the use of work equipment has received adequate training…" Supervisors have been identified as a "weak spot" in many companies' forklift training regimes. All too often, poor practice goes unchecked because managers aren't trained to spot it.
A practical course, as short as two halfday sessions, can make all the difference to a manager's ability to eliminate potential risks - so think: have you paid enough attention to your own training?
Despite recent improvements, forklift trucks remain statistically the most dangerous type of transport in the workplace.
The past five years alone have seen UK forklifts involved in more than 9,000 three-day injuries in addition to over 2,500 hospitalisations and, tragically, 50 fatalities.
Forklift trucks are large, powerful and heavy - frequently with low-visibility "blind spots" when laden - and, as any health and safety professional will know, employers have a legal duty to ensure workers operating such potentially hazardous equipment are properly trained.
Regulation 9 of the Provision and Use of Work Equipment Regulations 1998 (PUWER 98) states: "Every employer shall ensure that all persons who use work equipment have received adequate training for purposes of health and safety, including training in the methods which may be adopted when using the work equipment, any risks which such use may entail and precautions to be taken." This legal requirement for training complements a powerful business case for avoiding damage to goods, buildings and reputation, not to mention lost time and legal costs - plus, of course, the moral duty to protect employees.
However in practice, there are common oversights that occur in companies' forklift training arrangements. Just like with forklifts themselves, these "blind spots" can jeopardise safety unless addressed.
Temporary workers A temporary operator, even if they're only on your premises for a matter of days, requires the same safeguards as any permanent employee - including the requirement for training - under PUWER 98. This becomes more complicated when operators claim prior experience and training. Section 30 of the L117 Approved Code of Practice for Rider Operated Lift Trucks is clear: "Where employees claim to be trained and experienced, employers should insist upon evidence. Employers need to satisfy themselves that the training, experience and ability is in fact sufficient and relevant to the lift trucks and handling attachments to be used." Worryingly, a recent survey by the FLTA found 85% of recruitment advertisements for forklift operators required a "forklift licence" - when in fact there is no such document in the UK.
Where there is any doubt about a potential operator's experience with your equipment, environment and task, it is good practice - and good sense - to arrange a skills assessment.
Hand pallet trucks Because hand pallet trucks are not "driven", and do not have a lifting or stacking capability, they are often overlooked when it comes to training - or taken too lightly by employees.
However, they are as much subject to PUWER 98 as any other kind of equipment, and can do permanent damage to feet, ankles and lower legs if used inappropriately.
Adequate cover Don't forget, you need sufficient trained operators to cover holidays, unplanned absences like sickness, sudden surges in workload and, hopefully, future business expansion.
A surprising number of employers train operators, but find themselves caught out - and under pressure to take a major risk - because of a need to move a load at short notice, with no qualified staff available.
Colleagues working nearby An estimated two thirds of UK forklift accident victims are not the operator but a colleague on foot, in the wrong place at the wrong time. That's at least four pedestrians injured or killed by forklift trucks per day.
It's deceptively easy for an untrained colleague to assume a forklift operator has seen them when they're actually in a blind spot, or not to understand the danger zones caused by rear-wheel steer.
For this reason, independent advice from the FLTA strongly recommends that all staff who work near forklift trucks are at least trained in the risks involved and how to avoid them.
What about you? Another part of PUWER 98, Regulation 9, says: "Every employer shall ensure that any of its employees who supervises or manages the use of work equipment has received adequate training…" Supervisors have been identified as a "weak spot" in many companies' forklift training regimes. All too often, poor practice goes unchecked because managers aren't trained to spot it.
A practical course, as short as two halfday sessions, can make all the difference to a manager's ability to eliminate potential risks - so think: have you paid enough attention to your own training?
MORE FROM THIS COMPANY
RELATED ARTICLES
- Quick hitch safety road shows
- Key speakers for seminars
- Event to share best practice
- Free safety seminars
- Health & Safety '10 goes north
- Online resource
- Inspectors courses still
- Tackling Scotland's safety challenges
- Building knowledge and developing confidence
- "Businesses must make time to practise and train"
OTHER ARTICLES IN THIS SECTION