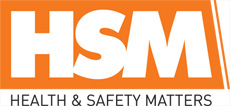
![]() |
Mark Sennett
Managing Editor |
![]() |
Kelly Rose
Editor |
ARTICLE
In safe hands
23 January 2013
In a market populated by cheap and counterfeit products, how does a premium supplier make the case for its range? Georgina Bisby went to hand arm protection specialist Marigold Industrial's Portuguese factory to find out
In a market populated by cheap and counterfeit products,
how does a premium supplier make the case for its range?
Georgina Bisby went to hand arm protection specialist
Marigold Industrial's Portuguese factory to find out
Like much of the PPE market, when it comes to hand arm protection there are several solutions available that differ in quality and price.
While some counterfeit or imitation products are of poor quality and offer little protection, others, for a time at least, may perform reasonably well and can be difficult to distinguish from higher quality items.
At Marigold Industrial's (part of the Comasec group) Portuguese plant there is a wealth of glove making expertise.
Dipping for the company's seamless range and knitting for the textiles range take place twenty four hours a day, five days a week and the plant has the capacity to make over 23 million pairs of gloves annually with the potential to increase this thanks to a recent lean manufacturing drive. An on-site R&D centre employs three chemical engineers and two textile engineers whose job it is to ensure the company continually innovates.
Focus on R&D To achieve this, staff at the R&D centre work in partnership with universities, textile manufacturers and other Marigold experts around the world to develop new yarns, glove coatings and product concepts.
Having a highly skilled R&D centre on site has the advantage of giving Marigold more control over its innovation.
Products developments are planned five years in advance and a minimum of one year is invested in any R&D for any project. Having on-site expertise also means Marigold doesn't shy away from more challenging innovations such as its recent success in incorporating leather technology into its gloves. This was a particular challenge because of the regulations that govern the use of leather but it was one that Marigold persevered with and the company now has a specially trained team working on this range.
Another advantage of having in-house expertise is that Marigold can customise new product developments to meet specific customer requirements, which enables the company to target specialised markets.
The company aims to bring out new products every year. Current projects include the development of a flexible level 5 cut resistant glove which is planned for launch this October.
Quality assurance Stringent manufacturing quality control measures are essential for any PPE manufacturer but even more so for those at the top end of the market. All of Marigold Industrial's suppliers are validated and approved before any orders are made and the company has a dual sourcing policy for strategic raw materials.
All critical products are inspected by a metal detector and there is a batch traceability number printed on all Bladecut level 5 gloves.
Marigold also goes beyond the required EN388 blade-cut test for its cut resistant range using the ASTM test method in addition. "Level 5 cut resistance can vary greatly," explains plant manager Alan Rimington. The Portugal plant has invested in one of the few ASTM testing machines in the world so that it can ensure all of its relevant gloves meet this standard.
While it is commendable that the company goes to this effort there is evidence to suggest there is a serious lack of knowledge among specifiers and users of protective gloves so it is questionable whether the market appreciates this? According to Rimington it is, because equal to this lack education is extensive product knowledge in areas where the need for hand protection is paramount: "Many car manufacturers for example now insist that level 4&5 gloves are tested to this standard," Rimington explains, adding. "ASTM is the future." Rimington notes that there has also been a shift in specifying attitudes since the recession. "People are waking up to the fact that quality is an investment and a better product will often last a surprising amount longer than a cheaper alternative." says Allen. "Our Nitrile range for example has been exceeding expectations and our sales teams are complaining that the gloves are lasting too long and putting them out of a job." All critical products are inspected by a metal detector
The future is green Another factor driving the market is the demand for more sustainable and environmentally friendly products.
Marigold's N1000 range passing the criteria for the Oeko-Tex standard marks a recent achievement in this area for the company. (Further details on the standard right) Rimington reports that user feedback on this range has been extremely positive so far and sustainability and environmental factors will be a key consideration in the development of future products. By way of an example, a key challenge for the future explains Rimington: "is to develop a fully biodegradable glove."
Getting a grip on hand protection According to Marigold Industrial there are several common mistakes made in the choice and use of hand protection, including:
Incorrect sizing which makes the user reluctant to wear gloves thereby reducing the level of protection Wrong type of glove: i.e. mechanical gloves are often used when a chemical glove is needed and vice versa Wrong level of protection: Chemical glove incorrect material for the hazard Wrong level of protection: a low mechanical model is used when cut resistance is required Lack of awareness of operator of allergy issues Disregard of Food approval EC/1935/2004 when working with and handling food Lack of knowledge of EN standards which assist in correct glove selection Incorrect donning and doffing procedures: resulting in operator chemical contamination Lack of pre-donning (air leaks) checks which highlights glove integrity and ensures operator safety
Like much of the PPE market, when it comes to hand arm protection there are several solutions available that differ in quality and price.
While some counterfeit or imitation products are of poor quality and offer little protection, others, for a time at least, may perform reasonably well and can be difficult to distinguish from higher quality items.
At Marigold Industrial's (part of the Comasec group) Portuguese plant there is a wealth of glove making expertise.
Dipping for the company's seamless range and knitting for the textiles range take place twenty four hours a day, five days a week and the plant has the capacity to make over 23 million pairs of gloves annually with the potential to increase this thanks to a recent lean manufacturing drive. An on-site R&D centre employs three chemical engineers and two textile engineers whose job it is to ensure the company continually innovates.
Focus on R&D To achieve this, staff at the R&D centre work in partnership with universities, textile manufacturers and other Marigold experts around the world to develop new yarns, glove coatings and product concepts.
Having a highly skilled R&D centre on site has the advantage of giving Marigold more control over its innovation.
Products developments are planned five years in advance and a minimum of one year is invested in any R&D for any project. Having on-site expertise also means Marigold doesn't shy away from more challenging innovations such as its recent success in incorporating leather technology into its gloves. This was a particular challenge because of the regulations that govern the use of leather but it was one that Marigold persevered with and the company now has a specially trained team working on this range.
Another advantage of having in-house expertise is that Marigold can customise new product developments to meet specific customer requirements, which enables the company to target specialised markets.
The company aims to bring out new products every year. Current projects include the development of a flexible level 5 cut resistant glove which is planned for launch this October.
Quality assurance Stringent manufacturing quality control measures are essential for any PPE manufacturer but even more so for those at the top end of the market. All of Marigold Industrial's suppliers are validated and approved before any orders are made and the company has a dual sourcing policy for strategic raw materials.
All critical products are inspected by a metal detector and there is a batch traceability number printed on all Bladecut level 5 gloves.
Marigold also goes beyond the required EN388 blade-cut test for its cut resistant range using the ASTM test method in addition. "Level 5 cut resistance can vary greatly," explains plant manager Alan Rimington. The Portugal plant has invested in one of the few ASTM testing machines in the world so that it can ensure all of its relevant gloves meet this standard.
While it is commendable that the company goes to this effort there is evidence to suggest there is a serious lack of knowledge among specifiers and users of protective gloves so it is questionable whether the market appreciates this? According to Rimington it is, because equal to this lack education is extensive product knowledge in areas where the need for hand protection is paramount: "Many car manufacturers for example now insist that level 4&5 gloves are tested to this standard," Rimington explains, adding. "ASTM is the future." Rimington notes that there has also been a shift in specifying attitudes since the recession. "People are waking up to the fact that quality is an investment and a better product will often last a surprising amount longer than a cheaper alternative." says Allen. "Our Nitrile range for example has been exceeding expectations and our sales teams are complaining that the gloves are lasting too long and putting them out of a job." All critical products are inspected by a metal detector
The future is green Another factor driving the market is the demand for more sustainable and environmentally friendly products.
Marigold's N1000 range passing the criteria for the Oeko-Tex standard marks a recent achievement in this area for the company. (Further details on the standard right) Rimington reports that user feedback on this range has been extremely positive so far and sustainability and environmental factors will be a key consideration in the development of future products. By way of an example, a key challenge for the future explains Rimington: "is to develop a fully biodegradable glove."
Getting a grip on hand protection According to Marigold Industrial there are several common mistakes made in the choice and use of hand protection, including:
Incorrect sizing which makes the user reluctant to wear gloves thereby reducing the level of protection Wrong type of glove: i.e. mechanical gloves are often used when a chemical glove is needed and vice versa Wrong level of protection: Chemical glove incorrect material for the hazard Wrong level of protection: a low mechanical model is used when cut resistance is required Lack of awareness of operator of allergy issues Disregard of Food approval EC/1935/2004 when working with and handling food Lack of knowledge of EN standards which assist in correct glove selection Incorrect donning and doffing procedures: resulting in operator chemical contamination Lack of pre-donning (air leaks) checks which highlights glove integrity and ensures operator safety
MORE FROM THIS COMPANY
OTHER ARTICLES IN THIS SECTION