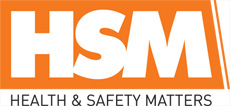
![]() |
Mark Sennett
Managing Editor |
![]() |
Kelly Rose
Editor |
Home> | Handling & Storing | >Warehouse Safety | >Reduce the risk |
Reduce the risk
18 October 2023
David Thomas looks at common warehouse hazards and the precautions that can help avoid costly accidents and life-changing injuries.

WAREHOUSES ARE dynamic environments where numerous hazards exist. They are busy and sometimes chaotic, with multiple activities taking place, noise, limited visibility and regular use of manual handling equipment, all of which open the warehouse up to the potential for serious accidents.
It’s important to understand what the most common warehouse dangers are. The Health and Safety Executive (HSE) notes manual handling, slips and trips, working at height and vehicles in and around the warehouse as key areas of concern1. Overlooking safety hazards in the warehouse is a major risk. The impact of serious injury can be life changing and the death of a member of staff at work is devastating. The financial risk to the business is also substantial following a major accident with property damage, lengthy investigations, fines and lawsuits often amounting to huge sums while the reputational damage can be impossible to ever recover from.
One of the greatest risks to workers involves being hit by a moving vehicle. 20 people lost their lives due to being hit by a moving vehicle at work in the UK 2022/23 2. According to the British Safety Council, forklifts alone account for around a quarter of all workplace transport accidents in the UK and are considered the most dangerous form of workplace transport, with an average of 1,300 forklift accidents and related injuries each year. It's not just drivers at risk as RIDDOR data collected over a three-year period in the UK, shows, with 43% of incidents involving a forklift truck being impact with a third person working in the area3. Accidents are often attributed to insufficient training, poor maintenance, inadequate segregation, and lack of supervision
It’s important proactive measures to counteract the opportunity for vehicle/pedestrian collisions are taken and tailored to suit the specific workplace and its known safety risks.
Training and procedures
Good communication is vital in any workplace but is particularly relevant when it comes to safety. The importance of thorough training cannot be underestimated. Employers are of course obligated to provide minimum safety standards and training under national legal requirements, but it’s also advisable to go above and beyond.
It's vital drivers are fully trained and that only those who have successfully completed training are permitted to operate the vehicle. OSHA estimates that around 20-25% of forklift related injuries are caused by inadequate training4. For operators, clear procedures around vehicle inspections, driving standards, crossings, speed and seat belt use are important in reducing the risk of injury. It is equally important that everyone who works around vehicles including management and temporary workers receive training to ensure their own safety and the safety of others.
Training equips workers with the skills and knowledge to operate safely around vehicles and places health and safety at the forefront of everyone's mind. Regular recurrent training around vehicle use and how to work safely around vehicles, helps to combat complacency which easily sets in as people become more familiar with the daily routine.
Clear safety procedures provide a defined set of reference guidelines. They help to prevent confusion especially during emergencies and in high stress situations. The combination of robust safety procedures and regular training help to embed a positive safety culture and drive safe working behaviour.
Segregation
The UK Health and Safety Executive (HSE) states that, where people and vehicles work closely, they must be able to operate without causing danger, and recommends separate roadways and pathways where possible 5. Total segregation is always the best solution but is difficult to achieve in the warehouse. Floor markings, cones and mirrors are a starting point, while barriers and fencing create a physical divide but can be difficult to install when space is limited.
In 2022, a UK worker suffered multiple fractures and spent a month in hospital after being hit by a forklift6. The HSE investigation found that there were ‘inadequate measures to ensure safe segregation of delivery drivers. In 2019, a lorry driver suffered life changing injuries when he was struck by a forklift truck while assisting in the loading of pallets. While loading, the forklift truck reversed and struck the driver, crushing his leg. Once again, the investigation found there was a lack of ‘suitable segregation between pedestrians and vehicles7.’
Safety technology such as cameras, sensors and proximity warning systems go a long way to combatting this issue. These technologies work by allowing people working in and around the vehicle to ‘see’ hazards outside their line of vision. By alerting pedestrians to a vehicle they cannot physically see, they are more aware of their surroundings and opt to move before it’s too late. Drivers who are alerted to the presence of pedestrians can stop the vehicle – to do this could be the difference between life and death.
Safety signage
Signage is required where there is significant risk and is a quick and easy way to warn of danger. There should always be sufficient safety signage in areas where vehicles operate, and it should be well maintained and clean.
Although safety signage plays a vital role in warning of danger, there is always the opportunity for complacency or ‘sign blindness’ when multiple signs are in place. Sign blindness is a phenomenon where people who regularly work around safety signage become oblivious to the messaging, and it loses impact. When the signs are seen for the first time, they stand out, but become almost invisible after repeated exposure. In these cases, it is worth considering more engaging options such as signs that grab attention in a more effective way by flashing lights and sounding alarms, or signs that automatically illuminate as a vehicle approaches. Automatic signage is highly effective in poor lighting or in areas with blind spots. It offers another way to reduce the chance of collisions when total segregation is not possible.
Good housekeeping
Good housekeeping is one of the foundations of warehouse safety. Obstructed aisles and clutter can cause serious accidents and block escape routes so keeping the warehouse tidy is important.
When floors are slippery, forklifts and other vehicles are much more likely to skid and lose control and unstable floors are one of the main causes of forklifts tipping over which can easily result in the driver being crushed. Signs and lighting must be well maintained, free of dust and obstruction to maintain visibility.
In cramped areas, vehicles like forklifts and order pickers can easily collide with racking so it’s important to consider additional measures such as clear stopping distances, alarms and safety technology that alerts drivers when in close proximity. Shelves should also be completely secure – if a collision occurs, falling objects could cause serious injury to people working below. Cluttered shelves lead to overhead dangers and heavy loads should be kept at ground level. Where robots operate, attaching sensors or proximity warning devices can help to reduce the chance of collisions with obstructions or vehicles, avoiding costly damage and repair.
Personal Protection Equipment (PPE)
Common PPE seen in the warehouse includes high visibility clothing, safety goggles/glasses and boots, overalls, hard hats, ear plugs and face masks.
When it comes to safety around vehicles in the warehouse, PPE is essential in creating visibility and in protecting workers from accidents. Hi-vis jackets make pedestrians more visible to drivers, helping them to stand out. Employers can go one step further by incorporating lights into hi-vis clothing, that flash as vehicles approach.
Additional technology like warning tags can easily be added to everyday PPE to alert workers to the presence of moving vehicles. These tags work by interacting with vehicles in the areas and providing an alarm to the wearer when risk is present. Tags can be small enough to attach to a lanyard or worn in a pocket so as not to interfere with tasks or cause discomfort.
There is no doubt that warehouses are dangerous and workplace vehicles pose a real threat to workers but when preventative action is taken around safety, and procedures, training and additional safety consideration, most of these accidents can be avoided.
References
5 https://www.hse.gov.uk/workplacetransport/separating.htm
7 Manufacturer fined after lorry driver injured in forklift accident (fork-lift-training.co.uk)
David Thomas is general manager at ZoneSafe. For more information, visit www.zonesafe.com
- Safety & Health Excellence Awards 2022 shortlist revealed
- Workers at risk during warehouse renovation
- Judge steps down as HSE chief executive
- Major campaign to tackle road deaths
- Bird farm worker seriously injured in shed blaze
- Building company fined after wall collapses
- Employee sustains burn injuries in avoidable explosion
- Sheffield firm with poor welfare facilities sentenced
- Government reveals smarter regulations
- Health and Safety Matters Podcast - Episode 43