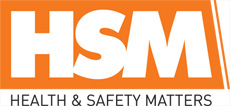
![]() |
Mark Sennett
Managing Editor |
![]() |
Kelly Rose
Editor |
Home> | Breathing Safely | >Gas Detection and Monitoring | >No room for error |
No room for error
16 August 2021
There really is no room for error when it comes to using the correct gas monitoring equipment in a confined space. Kelly Rose was joined on a webinar by Tony Pereira and Doug Kemp who are experts in this field.
WORKING IN a confined space is highly dangerous and workers face many risks including the loss of consciousness or asphyxiation from gas, fume, vapour or lack of oxygen; fire or explosion; risk of drowning due to an increase in liquids; free-flowing solids and loss of consciousness due to an increase in body temperature. Using gas monitoring equipment can certainly help with some of these risks and this became apparent in a recent webinar sponsored by MSA Safety which provided insight, guidance and advice around gas detection in confined spaces.
The Health and Safety Executive (HSE) defines a confined space as a place which is substantially enclosed (though not always entirely), and where serious injury can occur from hazardous substances or conditions within the space or nearby (e.g. lack of oxygen).
If upon a risk assessment the working space is classified as a confined space then there are certain measures that have to be taken to ensure that the worker can be rescued if necessary.
Tony Pereira looked at the risk-based assessment specifically to gas monitoring in confined spaces and looked at the properties of gas hazards. “Some compounds can be less dense than air, equal to air or lighter than air – and that is based on the molecular weight. Some gases can rise while others can drop to the floor. Depending on where that worker is located in that space they could be exposed at different levels. Part of this leads to stratification – also called layering – as the air becomes stratified with different gases at different levels.”
This was a very visual webinar and different scenarios are clearly demonstrated in the slides where you can see examples of complex spaces, and how different equipment can literally be the difference between life and death.
When your risk assessment has highlighted that the space is a confined space, you have to make sure your equipment is suitable for the task in hand. Suitable equipment used to detect gas in a confined space includes:
-
Single gas (personal protection)
-
Multiple gas (personal protection)
-
Sampling device (pre entry and remote sampling)
-
Area monitoring (area protection)
Tony says, “Area monitoring is not a replacement for any type personal protection or sampling devices – it is more supplementary to a gas detection programme that you may have for specific tasks based on your risk assessment.”
Points of consideration
For your risk assessment you need to consider that some single gas H2S devices to do not measure for Time Weighted Averages (TWA) and Short Term Exposure Limits (STEL) . You also need to look at T90 specification and not T50. The T50 is the time that it takes to measure 50% of the actual concentration of the sample you are reading, whereas T90 is the time that it takes to measure 90% of the concentration.
You also need to consider how many sensors are needed based on the risk assessment. If reactive gases have been identified then you need to consider the sampling line that is being used – so always check with your manufacturer of gas detection equipment.
When lowering a passive device or even a sampling line into a confined space you need to make sure that you are sampling at the different levels – and you need to provide enough time on each level for the sensors to respond. Continuous monitoring for atmospheric changes is very important and provides increased safety for the workers.
Tony says, “Personal monitoring may not detect atmospheric changes due to the stratification challenges and being a passive monitoring device they will only going into alarm when the gas is within the person's vicinity. Having an area monitor will allow you to mount the device or place the device in strategic locations in order to have multiple measurement points and to measure any change well in advance in order to mitigate any possible incidences.
“Area monitoring is supplementary to any gas protection programme and not a replacement to personal monitoring or sampling devices. Traditional passive area monitoring devices are heavy and may provide measurement challenges due to stratification. There is also a misconception regarding area monitors as being called an area monitor. The understanding within the market is that if an area monitor is put in a space then it is able to measure within 10, 15 or 20 metres of that specific area. This is not possible. The gas needs to make contact with the actual sensor – so it really is a point detection and the more points of reference that you have within a confined space gives you a far better homogenous reading and it is safer to complete your task.”
During these Covid times, cleaning hands and equipment has become part of the new normal – however there are concerns that hand sanitisers with alcohol in them can come in contact with the sensors and can lead to misleading measurements.
With all the hand sanitisers and disinfectants on site, the equipment is coming into more contact with these solutions than ever before, Tony advices, “The best way to validate the detector is fit for use is to bump test the device. Doing a bump test before every day's use is the only way to validate that the sensor is responding correctly.”
Digitalisation has been key for gas detection and MSA now offers live remote monitoring meaning that worksites can stay connected effortlessly. The Grid Fleet Manager ensures that overdue bump test schedules and compliance issues are highlighted straight away. Grid Live Monitor shares hazard and compliance concerns with you and you can initiate evacuations.
The webinar closed with a live question and answer session. You can watch the webinar and see the slides at:https://events.streamgo.live/gas-detection-in-confined-spaces-what-you-need-to-know/Gas-Detection-in-confined-spaces-what-you-need-to-know
Tony Pereira is marketing manager at MSA Safety, Doug Kemp is operations director at RIG Systems Limited. For more information, visit www.msasafety.com