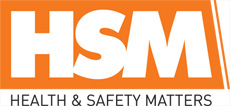
![]() |
Mark Sennett
Managing Editor |
![]() |
Kelly Rose
Editor |
The holy grail of construction
16 January 2020
Will Woodhead gives an insight into how technology is helping to solve problems in the construction industry.

Perhaps you have heard of a project manager describing the completion of a successful project, it may have sounded something like, “we completed the entire project on budget, on schedule and without hurting anyone”. Even as recent as 10 years ago that project manager may have described success as “not killing anyone” instead of hurting anyone. Times have changed, fantastic progress has been made however the appetite to do better has still not been satisfied, perhaps it may have swung the other way and people are even more motivated to prevent the injuries on site.
There is no getting away from the fact that safety is categorically one of the hardest problems to solve, NASA put a man on the moon but couldn’t stop people getting hurt. We have a dynamic, subjective multidimensional problem that is only considered solved when no-one gets hurt or sick. Zero injury and more recently zero illnesses really is the holy grail of construction.
What’s changed?
20 years ago, when I was working in shipyards and heavy industry construction sites, the primary focus was on safety (not necessarily health) and such hazards as falling from height or dropped objects. Fall protection in the form of harnesses or regularly inspected scaffolding was one of the first items discussed in every safety meeting. The consequence of this approach on safety saw very positive results and looking at the figure below it can be easily seen that this has saved 100s of lives every year since. But what about the ‘health’ part of H&S, have we forgotten this?
In contrast, over the last 20 years the work-related ill health has remained flat. Ill-health often influences mental health as well as involuntary retirement age. Construction is a physical job and not being able to work due to ill-health has significant consequences on a family reliant on a sole bread-winner. Saving lives undoubtably has a significant positive impact on society however improving the health of a workforce can deliver positive changes which can also have profound consequences.
This is genuinely being recognised by many forward-thinking construction companies as an area which needs attention and improvement. This is great for the UK’s construction industry however the problem remains, how do we solve this? Health and safety is a complex multi-dimensional problem with high stakes and people at the heart of it.
Leading or lagging indicators
In order to better understand where the risks are in an organisation, ‘HOC’, ‘HAZID’, ‘STOP’, ‘CLOSECALLS’, ‘NEARMISS’ cards are often used to identify hazards which nearly or could have created a safety incident. These are what’s known as leading indicators and using the principle of Heinrich’s Safety Pyramid areas of high / low risk can be identified so resources can be focused and safety improved. The problem is, this leading indicator data is not complete or robust enough to form strong correlations between unsafe conditions and the fatalities or injuries (lagging indicators) which follow. This is true when safety is discussed but how about health? If someone is consistently exposed to high levels of noise or continuous repetitive strain we are confident that these individuals will develop tinnitus or a muscular skeletal injury. So if ill-health is ‘so predictable’ why have we been more successful in reducing safety events which are historically harder to predict?
Industry 4.0
Enter industry 4.0 and the ability to understand an individual’s exposure to various different hazards. Industrial Internet of Things (IIoT) now allows as to measure noise, hand and arm vibration, fatigue and potentially the muscular-skeletal dosage someone is receiving whilst performing a task. Although this does not solve the initial problem it does allow us to better understand the exposure so that mitigation measures or technology can be put in place to reduce the harmful effects. The challenge is to create a system which effectively understands exposure however does not place any additional burden on the individual nor compete for his or her attention. Unfortunately some approaches to collecting data have resorted to additional reporting being completed by the individual on a smart phone or tablet. The thought is that this is smart technology but in truth it is just modern day paperwork.
Data transparency
Safety is the responsibility of all individuals, not just the HSE manager. Perhaps further empowering the workforce to understand problems by giving them access to the information and then getting them to implement the changes creates a culture of ownership and responsibility whilst also improving the engagement of the employees. Helping a colleague reduce the exposure to a hazard and then seeing the positive effects of that change would surely warm the most disengaged employees and help create a culture where health and safety really does come first.
Will Woodhead is the managing director of a Construction tech company called Mafic. Mafic uses Industry 4.0 technology to help solve these health and safety problems in construction. Mafic want to help improve the health, safety, employee engagement and job satisfaction of the construction industry and create some exceptional workplaces. www.mafic.ltd
- Cognitive bias and defending health and safety investigations
- Six steps to improve mental well-being in the workplace
- Why workplace safety is important
- Data shows decline of workplace injuries while mental health rises
- Top tips for driving in the dark
- Driving a shared global approach to H&S in the construction sector
- Let’s never stop being ‘starry eyed’ about safety and health
- Gas detection and monitoring: Safety as a service
- The hidden workplace risks of cold weather
- The human factor
- No related articles listed