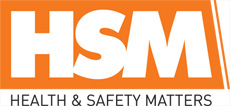
![]() |
Mark Sennett
Managing Editor |
![]() |
Kelly Rose
Editor |
1/7 (1 to 10 of 67)
Be prepared for cardiac events | 17/08/2025 |
---|---|
CARDIAC PREPAREDNESS should be part of every workplace safety strategy. Defibspace provides an insight. Sudden cardiac arrest (SCA) is a medical emergency in which the heart suddenly stops beating effectively. It differs from a heart attack, which is caused by a blockage in blood flow. SCA can lead to death within minutes without immediate action. For employers, cardiac preparedness is becoming a vital component of workplace risk management and wellbeing planning. Each year in the UK, around 30,000 people experience an out-of-hospital cardiac arrest. An estimated 15% take place in public or workplace settings, which adds up to around 4,500 events annually. Access to automated external defibrillators (AEDs) in the workplace remains inconsistent, despite these stats. Early use of an AED, combined with effective cardiopulmonary resuscitation (CPR), significantly increases survival chances. However, many UK workplaces still operate without a defibrillator on site, leaving gaps in their emergency preparedness strategies. Cardiac preparedness refers to the integration of:
These need to be added into an organisation’s overall health and safety planning. It forms an extension of existing duty-of-care policies. It also signals a commitment to creating a safe, responsive and health-literate work environment. Legal and duty‐of‐care considerations There is currently no specific legal requirement in the UK for workplaces to have a defibrillator on site. However, several pieces of health and safety legislation make it clear that employers have a duty to assess and manage risks and this increasingly includes consideration of cardiac events. First aid regulations Under the Health and Safety (First-Aid) Regulations 1981, all employers must ensure that employees receive immediate attention if they are injured or taken ill at work. This includes conducting a first aid needs assessment based on the nature of the work, workforce demographics, and associated health risks. While defibrillators are not mandated, the Health and Safety Executive (HSE) encourages employers to consider AEDs as part of their assessment, particularly in higher-risk or large-scale environments. Duty of care Employers also have broader responsibilities under the Management of Health and Safety at Work Regulations 1999. These require suitable measures to mitigate foreseeable health risks and sudden cardiac arrest is increasingly recognised as a plausible workplace emergency. Industry bodies such as the British Standards Institution (BSI) and the Resuscitation Council UK support the inclusion of AEDs in public and occupational settings. As awareness grows, so does the expectation that employers will take proactive steps to support staff safety, particularly in high-footfall workplaces or where medical response times may be delayed. Failing to address cardiac preparedness could expose employers to criticism or reputational harm, even if legal liability is unlikely. Time, CPR and AED Sudden cardiac arrest is a time-critical emergency. Survival rates fall sharply with each passing minute. This makes immediate intervention essential, well before emergency medical services (EMS) arrive on site. First few minutes According to the Resuscitation Council UK, for every minute that passes without CPR or defibrillation, a person’s chance of survival decreases by approximately 7-10%. After just 10 minutes without treatment, the likelihood of survival is extremely low. However, if CPR is started immediately and an AED is used within 3-5 minutes, survival rates can reach up to 70% in some cases. These statistics are supported by findings across multiple studies and public health programmes. Bystanders While ambulance services in the UK aim to reach patients with life-threatening conditions within 8 minutes, this is not always achievable. This is especially true in large workplaces, remote locations, or during peak demand. Having trained staff and an accessible defibrillator on site allows a bystander to intervene before EMS arrival. CPR maintains circulation, while the AED delivers a controlled electric shock to try to restore a normal heart rhythm. Many modern AEDs are fully automated and guide the user with visual and voice instructions. This chain of survival, early recognition, early CPR, early defibrillation, and early advanced care is only effective if the first three links occur in the workplace. Wellbeing culture and employer brand For HR, Health & Safety, and Wellbeing teams, cardiac preparedness reinforces strategic goals around workforce health, psychological safety, and corporate responsibility. Safety Employers who invest in AEDs and cardiac training demonstrate a tangible commitment to employee welfare. This supports a positive safety culture, where staff feel that their wellbeing is prioritised not only in policy but in practice. AED signage, staff awareness sessions, or inclusion in induction materials, help normalise cardiac preparedness as part of everyday workplace safety. Wellbeing The presence of a defibrillator can also reduce anxiety in employees who may be concerned about their health or that of colleagues, especially in higher-risk roles or among older staff. Including AED awareness in wellbeing communications helps build psychological readiness to act in an emergency. Some organisations now incorporate defibrillator training within broader wellbeing programmes. This aligns physical health with mental preparedness and workplace resilience. Employer brand In competitive sectors, visible investment in staff health and emergency readiness can support employer branding. Clients, visitors, and potential hires may view AED provision as a signal of professional and ethical standards. This reputational value aligns with Environmental, Social and Governance (ESG) goals, particularly the “social” dimension relating to occupational health and safety, although this is difficult to measure. Practical implementation Introducing cardiac preparedness into the workplace involves more than purchasing an AED. It also requires clear planning, integration into existing protocols, and ongoing management. 1. Cardiac Risk Assessment Begin with a cardiac risk assessment tailored to your workplace. Factors to consider include:
Larger or higher-risk workplaces may require more than one device, particularly across multiple floors or buildings. 2. Selecting the Right AED Key considerations when picking an AED:
Consulting manufacturers or medical suppliers can help match the device to your workplace context. 3. Accessibility and Placement Defibrillators must be:
Consider using a wall-mounted cabinet with visual signage. Outdoor models require heated, weatherproof cabinets. 4. Training and Familiarisation AEDs are designed for use by untrained bystanders, providing basic training builds confidence and reduces hesitation. The Resuscitation Council UK and HSE recommend integrating AED awareness into workplace first aid training. Many providers now include this by default. 5. Maintenance and Registration Every AED requires routine checks, even if rarely used. Appoint a responsible person to monitor:
Register your AED with The Circuit (the national defibrillator network), so emergency services can direct bystanders to it when needed: www.thecircuit.uk Cardiac preparedness in wellbeing and safety strategy Cardiac preparedness should not be treated as a standalone initiative. It must be embedded within the organisation’s broader health, wellbeing and safety culture. Integrating into wellbeing frameworks HR and wellbeing teams can align defibrillator provision with existing health initiatives, such as:
This positioning shifts AEDs from a reactive safety measure to part of proactive health promotion and reinforces the message that the organisation takes all aspects of wellbeing seriously. Adding to safety systems AED provision should also feature in:
Some organisations include cardiac drills in their emergency testing calendar, especially in larger or higher-risk premises. Encouraging participation Awareness campaigns, short lunch-and-learn sessions, or internal communications can increase staff understanding and engagement. Some employers share anonymised stories of successful AED use or run demonstrations during wellbeing weeks. Normalising the presence and use of defibrillators encourages faster action in an emergency and reduces fear of using the device. Summary & what to do next Cardiac preparedness is a practical, evidence-backed enhancement to any workplace safety and wellbeing strategy. For HR, Health & Safety, and Wellbeing teams, it offers a way to strengthen risk management, staff confidence, and organisational reputation. Key points to consider:
Next Steps for Implementation
This approach helps organisations meet emerging expectations, support their workforce more holistically, and prepare effectively for emergencies. For more information, visit www.defibspace.com Sources below is a list of sources used in this article. Resuscitation Council UK - AED Use and Guidance https://www.resus.org.uk/sites/default/files/2020-03/AED_Guide_2019-12-04.pdf The Circuit - National Defibrillator Network (British Heart Foundation) https://www.thecircuit.uk Health and Safety Executive (HSE) - First Aid at Work Regulationshttps://www.hse.gov.uk/firstaid/legislation.htm St John Ambulance - Workplace AED Provision https://www.sja.org.uk/course-information/blog/save-lives-protect-staff-your-guide-to-wor kplace-defibrillators British Red Cross - AEDs and Staff Wellbeing https://www.redcrossfirstaidtraining.co.uk/first-aid-blogs/how-defibrillators-in-the-workpla ce-can-support-employee-wellbeing Wolverson Medical - AED Importance in the Workplace https://www.wolverson.uk.com/the-importance-of-a-workplace-defibrillator Skills Training Group - Legal Overview of AEDs in the UK https://www.skillstg.co.uk/blog/the-legal-requirements-for-defibrillators-uk-essential-guide lines-simplified Steroplast Healthcare - AED Placement and Maintenance https://www.steroplast.co.uk/knowledge-base/workplace-defibrillator-everything-you-nee d-to-know.html CESafety - AED Training and Operational Integration https://cesafety.co.uk/news/complete-guide-aed-defibrillators-training-use-operation Gov.uk - AED Guidance for Educational Settings (General Principles Apply) https://assets.publishing.service.gov.uk/media/67936b102de28ea2d392f35b/Automated_ External_Defibrillators__AEDs__guidance_for_schools.pdf |
|
|
|
Protecting lone workers in a warming world | 08/07/2025 |
SAM TOWENS discusses the steps that employers should be taking to protect workers - especially those working alone - with rising heatwaves expected across the globe. According to the Health and Safety at Work Act 1974, employers have a general duty to ensure the health, safety and welfare of their workers. When carrying out this duty, are enough companies considering the danger of extreme heat? There’s an 80% chance that the world will experience the warmest year on record over the next half-decade. With around 4 billion people already experiencing thirty extra days of extreme heat over the last annum, made twice as probable by the warming planet, action to protect the population must be taken now. For business leaders, the risk to employees must not be downplayed. The story of David Azevedo, a construction worker who died from a ‘cardiac arrest caused by severe hyperthermia’ in 2022, is a stark reminder of the danger. By introducing proactive measures, including training on the symptoms of heatstroke and changes to working hours, deaths like David’s can be prevented. When lives are at risk, it's just not enough to do the bare minimum. Heat-related illnesses, such as heatstroke, dehydration, and heat exhaustion are the most immediate risks. For lone and remote workers, who may not have immediate access to medical assistance, the stakes are even higher. Lone workers: An at-risk group Lone workers, those who work by themselves without close or direct supervision, are particularly vulnerable to rising temperatures. Without colleagues nearby, they are more vulnerable to the effects of extreme weather, and any delay in identifying or responding to heat-related symptoms can lead to severe outcomes. Concerningly, our latest ‘Lone Worker Landscape Report’, revealed that fewer than 30% of lone workers feel adequately protected or included in risk assessments. This highlights a significant gap in workplace safety, with many workers being left unaccounted for in emergency planning. For businesses, this means a lack of visibility and limited ability to ensure the safety of workers in high-risk environments. Technology as a safety enabler As the risks of heatwaves and extreme weather grow, technology plays an important role in protecting workers, particularly lone and remote workers. By leveraging technology, businesses can enhance risk assessments and create more effective safety strategies.
Resilience amid chaos As heatwaves become more frequent, employers must take proactive steps to protect workers and ensure long-term business resilience. With 50% of businesses affected by extreme weather events in the past few years, companies must act now to mitigate risks and prepare for worst-case scenarios. In the long term, this approach brings value by minimising losses and reducing operational expenses after a disaster, with potential savings of up to five times the amount invested. Sam Towens is product marketing manager at EcoOnline, To find out more about crisis preparedness in a warming world, you can read insights from EcoOnline’s latest The Situation Room article or register here to join the live debate on 30 July 2025. |
|
|
|
Gas detection and monitoring: Safety as a service | 24/06/2025 |
BUSINESSES ARE rethinking how they acquire safety equipment and are increasingly renting equipment when it is needed. Neil Shepherd provides an insight. When it comes to managing corporate health and safety responsibilities such as gas detection and monitoring, having the right equipment in place to keep employees safe, and to protect company assets, is essential. However, when it comes to funding this type of equipment, there is a growing recognition that in some situations and environments, renting apparatus may provide advantages compared to buying outright. The continued global economic uncertainty, in addition to the impact of domestic policy, such as the changes to employers’ National Insurance (NI) contributions means that for many businesses, cashflow has inevitably been affected. This situation makes the case for rental increasingly compelling, providing a way to optimise cash flow, conserve capital and increase borrowing capacity; while giving companies access to the very latest, up-to-date safety equipment. Traditionally, safety equipment, (whether for gas monitoring, respiratory protection, or other aspects of safety), has usually been purchased outright, and businesses will often store such safety apparatus on their own premises, managing tasks such as ongoing maintenance and calibration so that it can be employed as needed. In some instances, this may not be more than once or twice a year (for shutdowns or specific short-term projects, for example), meaning that equipment – although vital to have in place – can quickly become outdated, or even obsolete. Increasingly we are seeing businesses rethinking how they acquire safety equipment, instead adopting a ‘safety as a service’ style approach focused on renting equipment as and when it is needed. Although a relatively innovative method of procuring equipment in safety, this type of approach is of course common when it comes to acquiring other items across businesses, such as corporate vehicles or large capex items involved in manufacturing or construction. It is broadly recognised that using rental rather than outright purchase for these capex items has a range of economic benefits, providing more control over cashflow and preserving working capital. These same benefits often apply to safety equipment. Furthermore, when it comes to safety, advances in technology mean that accompanying software and systems are constantly evolving, becoming ‘smarter’ and offering more flexible assets with greater connectivity. So, instead of raising capital to update their own systems, an option open to UK businesses is to use a rental service, meaning that the business always has cost effective access to the latest equipment, fully updated and maintained to all relevant safety specifications. Additionally, newer equipment is often less complex and easier to use, reducing training requirements and allowing staff to get up to speed quickly, as training can be carried out easily and swiftly online. Furthermore, such innovation isn’t limited to the equipment itself. Over recent years, suppliers like us have developed ‘self-service’ methods of safety equipment rental – for example, at Dräger we have a Rental Robot system – essentially a vending machine style approach to safety devices and equipment, which can be located on a company’s premises for as long as needed. Such systems ensure kit is fully serviced, charged, calibrated and updated before it is released to each user, as well as ensuring the user is registered, trained and cleared to use the equipment in question. Originally these units were most frequently set up for decommissioning shutdowns in the oil and gas industry, but they are now widely in use throughout the UK for applications within a wide range of general industry settings, providing round the clock access and tracking of all assets. This saves on time, cost and resources while providing transparent accountability when projects require an audit trail. The equipment in Rental Robots is remotely updated – with the responsibility of doing so resting with the equipment hire company – effectively outsourcing a business’ safety equipment needs and ensuring the very latest, fully-working and serviced technology is on site, ready for use when it is needed. An additional, and important, benefit of rented equipment is that it is more sustainable: equipment is re-used, reducing environmental impact by minimising waste, conserving resources, and promoting efficient use of equipment. In conclusion, whether a company is looking to acquire hydrogen gas detection devices for a laboratory in a science park, or fire and escape equipment in a heavy industry setting, or drug and alcohol testing equipment for an office environment, renting such equipment can provide a cost-effective option. Crucially, without compromising on safety, whilst also streamlining the funding and operational aspects of safety and adhering to best practice as well as broader corporate social responsibility (CSR) policies. Rental Robot case study A large multinational chemical company uses Dräger’s Rental Robot units at 11 locations, giving its workforce access to fully charged, fully serviced, updated and calibrated, ready-to-use equipment whenever needed, so workers can focus on timely completion of projects. In doing so, the company saves time and money on preventative maintenance and worker downtime and has a fully audited record of the usage history, performance and maintenance of equipment, and a readily available analysis for compliance and procurement. Since installing the rental robots – the first totally autonomous turnaround and shutdown (TAR) system, the company has reported a 44% saving on staffing costs in this area as there is no longer a need for personnel to operate the stores, and a 29% saving on equipment costs as a result of charging being made on a pay-as-you-use model, rather accruing daily hire charges. In addition, there have been savings on consumables due to reduced testing requirements. At a glance – five reasons to rent:
Neil Shepherd is marketing manager at Dräger Hire. For more information, visit www.draeger.com/en_uk/Safety/Services/Draeger-Hire |
|
|
|
Road deaths rise a wake-up call for businesses | 17/06/2025 |
RECENT STATISTICS show that UK road deaths in 2024 rose by 1% year-on-year. This equates to losing at least four people every day on our roads. Nick Butler discusses how this is a backwards step for the UK and a wake-up call for businesses who have a duty to protect their drivers. Department for Transport (DfT) provisional data for 2024 shows there were 1,633 fatalities on the road last year. Of those who died, 977 were males aged 17 to 69 and 235 were working-age women. In addition, 66,245 men aged 17 to 69 were recorded as casualties, alongside 38,468 women. I think everyone will agree that - while unsurprising - these figures are nothing short of shocking. Key risk groups Fatalities among motorcyclists increased by 9%, in the largest rise among all road user types. This increase can be put down to a surge in novice riders (especially those working in food delivery) who may lack sufficient training and road experience. There’s a clearly particularly urgent need to refocus around this vulnerable group, and the sooner the better. Pedestrian fatalities are also up by 2% as a result of the growing number of larger vehicles on the road, such as SUVs and pickups, which pose a threat to vulnerable road users. Equally, why aren’t we reconsidering urban vehicle design and updating regulatory frameworks to enhance pedestrian safety? Deaths in service Outside of these vulnerable groups, we know a third of all road deaths involve someone driving for work (UCL and Agilysis), so it’s vital as employers we all take note of these numbers. Every death on our roads is a tragedy - and each one is avoidable. As a collective, the government, businesses, and drivers, we need to be doing more to make zero road deaths a reality – and together we can! The wider picture Let’s put these figures into context. Sadly, the UK is falling behind many EU countries when it comes to road safety. The EU has set a target to halve the number of road deaths by 2030 (based on 2019 levels) and most European countries have similar national targets. 56% of the countries monitored by European Transport Safety Council’s Road Safety Performance Index (PIN) Programme saw a decline in road deaths in 2023 year-on-year. The top three were Malta, with a 38% reduction, Luxembourg achieving 27% and Belgium hitting an 11% cut. What these figures show us, is the difference between countries that are prioritising safe road strategies and those that aren’t. The road forward Put simply, the UK needs a road safety strategy designed for modern living, and fast. The government has one in development, which will mark the first new strategy for preventing road deaths in over a decade. But it’s already been too long coming, and we don’t have a guaranteed date for arrival. As The AA’s president Edmund King recently highlighted, we need a strategy that takes bold action. This includes bringing in the likes of harsher penalties for those not wearing a seatbelt and those driving under the influence of drugs. We also need to help safeguard newly qualified drivers to ensure they feel confident on the road before exposing them to additional risks such as peer-aged passengers. Here’s an example of why. Still, today, dispute all the awareness around seatbelt safety, the stats are horrifying. Recent analysis by The AA Charitable Trust found that almost half (43%) of young passengers (17-29) who die in car crashes are not belted. When the data is analysed across all ages, unbelted fatalities stand at 27% of car passengers. Wearing a seatbelt reduces the risk of death by around 50%, so we must get to the point where 100% of drivers and passengers are wearing them at all times. Support for new drivers To further support new drivers, we are calling for the introduction of Graduated Driver Licensing (GDL). One in five young drivers crash within a year of passing their test, with 1,500 young drivers killed or seriously injured each year. Did you know, with every extra same-age passenger, you are four times more likely to crash? GDLs would help address this, ensuring drivers have had time to demonstrate their skills on all road types. GDLs should also state that new drivers shouldn’t be allowed to carry same age passengers for at least six months. These are just two examples of issues that need addressing and should form part of the UK’s road safety strategy to cut road deaths. We need change and we need it now to save lives. Navigating the risks as a business With uncertainty around the timing of a national strategy, businesses cannot wait. We have to keep our workforce and other road users safe. We can do this by making road safety a business priority, embedding safe practices into its culture, and investing in the right driver training. These latest statistics are a timely reminder that we should never ever be complacent when it comes to road safety, and we have the power to make a difference. Final thoughts In 2024, the UK’s roads claimed more lives and showed troubling trends in key user groups. Without swift, decisive action from both government and businesses, these losses will continue. The time for bold leadership and innovative safety measures is now. Let’s not forget that behind every statistic is a family shattered - and potentially too, a business impacted. Nick Butler is director at Drivetech. You can download Drivetech's advisory guidance for motorcyclists and vulnerable road users at: https://www.drivetech.co.uk/downloads/. |
|
|
|
Achieve a culture of competence | 27/04/2025 |
WORLD DAY for Safety and Health at work offers us an important opportunity to reflect on how we approach safety in the workplace, particularly in high-risk industries. Deborah Yeats provides an insight. While we focus on procedures and compliance, true safety, isn’t about just checking boxes, it’s about ensuring competency. This article aims to explore the importance of competence, how it fits into safety management systems, and why we need to shift from simply following procedures to creating a culture of competence in the workplace. The Importance of Competence In high-risk industries such as construction, oil and gas, chemicals, renewables, and manufacturing, safety is paramount. It’s not enough for employees to merely follow procedures, they need to have the skills and understanding to apply those procedures effectively in real-world situations. This is where competency comes in. Competency is the ability to perform tasks to the required standard, consistently and confidently, with a heavy focus on safety. It’s not about completing a training course or obtaining a certificate; it’s about being able to perform under pressure and make the right decisions when faced with real-world challenges. A worker might have all the certifications in the world, but without the practical experience and the ability to think and act critically in a high-risk environment, they may not be competent. Competency encompasses safety, technical and behavioural knowledge and skills. It’s not just about knowing the procedures, it’s about applying them correctly, especially when things don’t go as planned. For example, a worker may be certified to operate machinery, but if an emergency arises, they need to act quickly and safely, something certification alone can’t guarantee. Certification vs. Competency: Why Competency Matters Certification is important, but it’s not the same as competency. Certification tells you that someone has passed a specific test or completed a training programme, but it doesn’t mean they can necessarily apply that knowledge in real, sometimes unpredictable situations. Certification is typically a one-off event, but competency is an ongoing process that is part of daily life. True competency means that all those performing safety-critical tasks can execute them safely, consistently, and in line with safety and technical standards, even under pressure. This involves continuous learning, adapting to new risks, and building practical experience. In safety-critical industries, this ability to adapt and apply knowledge is vital, as even small mistakes can have severe consequences. This shift in mindset, from simply checking off certifications to ensuring true competency, can lead to a more proactive safety culture. A competent workforce doesn’t just react to safety problems as they arise but actively works to prevent them from happening in the first place. Competence in the Context of Safety Management Systems A Safety Management System (SMS) is a structured approach to managing safety within an organisation. It includes policies, procedures, training, and practices designed to identify, assess, and control risks. Competence is an integral part of any SMS, as it ensures that the people responsible for safety-critical tasks are not just following the rules but are truly capable of confidently executing them at the highest standard. For an SMS to be effective, the competency of the workforce must be central. Without a competent team, even the most robust safety management system will fall short. Competence ensures that safety procedures are not just theoretical concepts on paper but are applied accurately and effectively in practice. Moreover, safety management systems should not be static, they must evolve to meet new challenges and risks. Competency allows organisations to adapt and continuously improve their safety practices, ensuring that employees are equipped to handle changing conditions and emerging hazards. Building a Culture of Competence Creating a culture of competence involves more than just ensuring employees have the right certifications or are just assessed against a set of criteria. It’s about embedding true competency into the fabric of the organisation where there is a proven, reliable and consistent application of knowledge, skills and behaviours as part of daily life. It’s not just about people knowing about something or following procedures, it’s about them doing it well whatever the situation. In my experience, here are some key steps to building a culture of competence:
The Role of 3t’s Competence Framework At 3t, we’ve developed a Competence Framework that helps organisations clearly define, develop and assess the safety, technical, leadership and behavioural competencies required for safety-critical roles. This framework focuses on the Knowledge, Skills, and Experience (KSE) needed for each role, and how to assess them against knowledge and performance standards. Our framework is tailored to meet the specific needs of high-risk industries. It is based on the understanding that safety is an ongoing journey, not a one-time achievement. By using this framework, organisations can ensure that their teams are not only knowledgeable but truly competent in managing risks and making safety decisions in real-world situations. A truly competent workforce goes beyond following procedures; they are able to adapt, think critically, and make informed decisions when it matters most. This approach not only improves safety but also creates a more resilient, proactive organisation that is well-equipped to handle the challenges of high-risk industries. As we work toward building safer workplaces, let’s prioritise competence at every level of our organisations, ensuring that our workforce is not only trained but truly capable of keeping themselves and their colleagues safe. Deborah Yeats is training and competence director at 3t. For more information, visit www.3tglobal.com |
|
|
|
Protection from a distance | 15/04/2025 |
WHEN IT comes to protecting lone workers, distance doesn’t have to mean danger, says Alastair MacLeod. Each year, hundreds of thousands of people work alone, many of these in remote or unpredictable environments. With no nearby colleagues to spot hazards or offer immediate help, they face risks that can turn deadly in a matter of minutes. Think for example about technical inspection of remote power lines or telecommunications infrastructure, or even search and rescue where individuals are required by the situation to operate on their own and off grid. According to the Health and Safety Executive (HSE), around a fifth of the UK workforce are classed as lone workers. Under the HSE’s guidance, these include individuals operating away from a fixed base: social workers, sales representatives, HGV drivers, and engineers, among others. Not all lone workers face the same type or degree of danger. A social worker regularly visiting unfamiliar housing estates might encounter volatile situations, while an engineer could be sent to a desolate wind farm during a winter storm. In both scenarios, they’re entirely reliant on technology or self-assessment to stay safe. Under the Health and Safety at Work etc. Act 1974, employers bear a duty of care for all staff, including those out on their own. Yet the question remains, are firms doing all that they can to keep workers out of harm’s way? Every UK organisation must formally assess risks to employee health and safety under the Management of Health and Safety at Work Regulations 1999 (Regulation 3). This includes evaluating whether being alone amplifies a known threat, something the HSE highlights in its guidance1. For example, an injured telecoms engineer atop a rural mast is far more vulnerable if there’s no one immediately nearby to help. One practical solution is to deploy dynamic risk assessments, in which the worker themselves keeps an eye on changing conditions - be it weather, location hazards, or people onsite. However, some may argue that this culture of real-time vigilance doesn’t always take root without proper training or technology. Technology takes centre stage Satellite-powered IoT (internet of things) devices bring a host of benefits to different sectors, and each type of solution is typically tailored to the demands of specific industries. Take rugged models with generous battery capacity and robust global coverage, for example, that lend themselves to military, security, and heavy machinery environments. By delivering detailed satellite tracking updates and a dedicated SOS function over multiple weeks, they ensure a constant safety net for personnel who may be stationed in harsh or remote conditions. The hardware’s durability and water-resistant casing can also stand up to rough handling, extreme weather, or prolonged outdoor use. For adventure and expedition settings, there are solar-powered trackers that function for years with minimal user intervention. These devices are often used in adventure racing events, long-distance expeditions, group travel, or for tracking valuable equipment on the move. Because the trackers can run continuously under sufficient sunlight, they are ideal for projects that require long-term, low-maintenance monitoring. Although they may not always include two-way messaging, they excel at reliably relaying position data and providing reassurance to teams scattered across wide-ranging terrains. Finally, in scenarios where individual explorers, journalists, or recreational enthusiasts need both portability and real-time communications, compact satellite units with two-way messaging can be a lifesaver. Their small footprint makes them easy to carry in a backpack or clipped onto gear, and their ability to send or receive brief messages, even in cellular dead zones, adds a valuable layer of reassurance. Whether someone is sailing, hiking, or flying over remote stretches, the capacity to check in with contacts or call for help, without relying on mobile networks, can significantly reduce risk and improve overall situational awareness. Across all these use cases, the core advantage of satellite-powered trackers is that they offer location tracking and emergency communication in places where smartphones simply aren’t robust enough. Smartphones are gaining the ability to access satellite networks, but the devices themselves are vulnerable to battery failure, overheating or damage, making them a poor substitute for a dedicated, ruggedised tracking device. This enhanced connectivity bolsters lone-worker safety, enabling swift responses to incidents and fostering peace of mind in industries where isolation is common, ultimately ensuring that distance and difficult conditions don’t equate to vulnerability. Ultimately, whether it’s a rugged, multi-week device for remote security teams or a small unit built for individual explorers, the key message is the same: technology has reached a point where no one needs to be left vulnerable and isolated. As employers, and as a society, we have the power to choose robust, reliable systems that ensure no worker goes unprotected, no matter where their duties take them. Alastair MacLeod is CEO at Ground Control. 1 https://www.hse.gov.uk/pubns/indg73.htm |
|
|
|
The differences between low and high concentrations of H2S gas | 06/03/2025 |
HYDROGEN SULFIDE (H2S) gas can be fatal at high concentrations. But even low concentrations can cause health issues, particularly with prolonged exposure. So how can you best protect workers and minimise downtime? Alexander Barbashin answers your common questions about H2S. Hydrogen sulfide is a highly flammable, toxic and corrosive gas found in several industries including oil and gas, wastewater and chemical processing. It’s sometimes called ‘sour gas’, ‘sewer gas’ or ‘stink damp’ because of the way it smells like rotten eggs. However, H2S can’t reliably be detected by smell as it quickly deadens the sense of smell (a process known as ‘olfactory desensitisation or fatigue’). How dangerous is H2S? Exposure to high levels of H2S can be fatal, leading to loss of breathing, coma, seizures and death. It’s the second most common cause of fatal gas inhalation exposure in the workplace, second only to carbon monoxide.1 But H2S can also be harmful at low concentration levels, causing headaches, dizziness, nausea, breathing difficulties and a sore throat. These health impacts can become more serious with prolonged exposure. Low concentration vs. high concentration H2S – exposure limits The health impacts of H2S depend on how much is inhaled and for how long. The recommended exposure limit set by NIOSH (the US National Institute for Occupational Safety and Health) for ten minutes is 10 ppm2. However, some U.S. states have developed ambient air standards for H2S well below OSHA and NIOSH standards due to concerns about health risks from chronic exposure3. For longer exposures to H2S, the recommended limits are a lot lower. For example, if you’re exposed for up to 24 hours, the World Health Organisation (WHO) recommends a maximum exposure of 0.1 ppm. In response to concerns about the risks of H2S to human health even at low concentration levels, some countries have introduced equally stringent guidelines requiring businesses to monitor H₂S at such concentrations. That’s why we’ve recently updated our ALTAIR io™ 4 Connected Gas Detector, offering the option of a low-concentration hydrogen sulfide sensor that can detect H2S at very low levels*. H2S in industry – the different sector impacts H2S creates safety challenges for many industries. But some industries are more likely to be affected. These include: Oil, Gas & Petrochemical (OGP) OGP facilities handle raw ‘sour’ gas and oil which are naturally high in H2S. Extraction and refining processes release H2S, which may accumulate in confined, poorly ventilated spaces like processing units, pipelines and storage tanks. Closed systems with high-pressure conditions amplify the risks for workers. Balancing safety and operational efficiency is an ongoing challenge in the OGP industry. Some are tackling this challenge by integrating new technological solutions into their safety management practices. Waste water management Wastewater facilities such as closed pipelines and sludge tanks have low oxygen levels and so provide the ideal conditions for H2S buildup. This is because sulfate-reducing bacteria which break down organic material and produce H₂S as a byproduct thrive in anaerobic (low-oxygen) conditions. One of the key risks for wastewater workers is when they’re entering confined spaces like tanks and sewer lines. For many waste water management businesses, real-time monitoring of gas levels is considered a must-have. Steel production The steel industry’s use of high-temperature processes and sulfur-rich materials can lead to the release of H2S, creating hazards for workers. Confined, poorly ventilated spaces and desulfurisation units pose particular risks. A safety challenge for large steel production facilities can be determining who has used which portable gas detector and when. One company has found a solution to this common problem using the Connected Work Platform driven by ALTAIR io™ 4 connected gas detector. Preventative measures – safeguarding workers Given the well-documented risks of H2S to workers, safety managers are seeking out effective preventative measures, including regular training and effective ventilation. The use of Personal Protective Equipment is also important. But a particularly helpful method for avoiding excessive H2S exposure is constant monitoring by advanced gas detection systems such as our ALTAIR io 4 Connected Gas Detector. Such systems can give you an early warning of even subtle increases in H2S concentration, helping you stay ahead of potential risks. Our updated ALTAIR io 4 device can detect subtle changes in H2S concentration levels at a resolution of 0.1 ppm, offering enhanced protection to workers. The default configuration for low-concentration H2S detection starts at 0.3 ppm, but customers may choose to configure the device to detect H2S starting at 0.0 ppm. This capability is particularly important in industries like oil and gas where companies wish to monitor low levels of H2S. Our low-concentration H2S sensor also offers processes designed to streamline regulatory compliance, minimising downtime and allowing readiness even for large-scale operations. As with all toxic gases, early detection of H2S is an excellent way to alert safety managers to small increases in H2S emissions so they can help workers avoid harmful exposure, even at low concentrations. *The default configuration for low-concentration H2S detection on the ALTAIR io 4 connected gas detector starts at 0.3 ppm, but customers may choose to configure the device to detect H2S starting at 0.0 ppm (in increments of 0.1 ppm). Alexander Barbashin is customer marketing manager FGFD MEAIRR at MSA Safety. For more information, visit msasafety.com References |
|
|
|
Bridging the gender gap | 24/03/2025 |
IT'S TIME to bridge the gender gap in health and safety, says Sarah Mlundira. According to the British Safety Council, less than a quarter (21.7%) of health and safety professionals are women. For an industry that operates across such a diverse array of sectors, it’s concerning that women are significantly underrepresented professionally. In fact, only 15% of leaders in health and safety were women, compared with 29% in senior business roles globally; this means gender-related risk is not being given the priority it deserves, which can have dangerous effects. While this can be attributed to a number of factors, such as the historical imbalance between men and women and a lack of female role models in the sector, it’s no excuse for the health & safety industry to ignore the issue. Encouraging girls into STEM from a young age Inspiring girls from young age to see the vast opportunities a STEM career can offer is essential to increasing female representation in the sector. The health and safety industry, for example, is still dominated by male-centric imagery – think stock photos of men in hard hats – despite the fact that everyone on site, regardless of gender, has to wear the same protective gear. Breaking these gendered stereotypes is crucial to encouraging more women to enter this field. The challenge often begins in schools, where girls are less likely to be actively encouraged to consider STEM careers, despite the fact that they often outperform boys in these subjects at GCSE and A-level. Yet, participation in these fields remain overwhelmingly male-dominated. By encouraging girls from a young age to consider careers in health and safety, or even adjacent industries, this helps foster a strong pipeline of talent. Both schools and industry leaders should focus on promoting female role models in these fields through mentorship programmes, career talks, and hands-on STEM activities: such programmes have been shown to improve promotion and retention rates for women and minorities. By creating an environment that supports and encourages women to consider these career paths, more young girls will feel confident and inspired, helping to close the gender gap in a vital industry. Advancing the role of health and safety Health and safety roles are often undervalued, and even frequently ridiculed, despite being essential in protecting workers from serious injuries – or worse. To elevate its status within organisations, companies should consider integrating health and safety leadership at the highest levels, such as appointing a dedicated board-level representative. This not only reinforces the importance and respect the industry deserves, but also makes it a more attractive career path to consider. Furthermore, promoting diversity and breaking down gendered stereotypes is a responsibility of that should fall on all business leaders - not just female professionals in the sector. It’s crucial that this is seen as a problem for everyone to solve, not least because non-inclusive environments can actually be dangerous for health and safety. For example, current PPE is almost always designed for men, with little consideration for specific needs that women might have. Ill-fitting safety equipment can increase the risk of injury, create unnecessary stress for employees, and even deter women from entering the field altogether. Making career transitions easier While it’s very important to build up a pipeline of young talent, the problem isn’t one that can wait for years, if not decades, to be resolved. We must also look at the current state of the workforce. Women often transition into the health and safety sector from adjacent industries, which can cause significant professional challenges. Streamlining this process through targeted training programmes and upskilling opportunities can make the move appear more accessible and appealing. Even small changes – such as reviewing job descriptions to ensure they focus on essential skills, rather than outdated stereotypes – can attract a broader range of candidates. Proactively closing the gender gap in health and safety Closing the gender gap in health and safety is not only necessary but entirely possible. By encouraging young girls to explore STEM careers from an early age, we can break down historical imbalances and inspire the next generation of female professionals in the industry. Making the transition into health and safety more accessible for women, alongside increasing the visibility of female role models, will help create a more diverse and inclusive workforce. Furthermore, elevating the perception of health and safety beyond outdated stereotypes will highlight its critical role in workplace wellbeing. Tackling these barriers can help organisations tap into a more diverse talent pool and more inclusive workplace. This greater diversity will not only strengthen teams, but lead to better decision-making and improved safety outcomes for everyone. Sarah Mlundira is global head of technical department at Sentric Safety Group |
|
|
|
Wisdom and wit from a safety psychologist | 28/01/2025 |
TIM MARSH gives us a taste of what you can expect in his recently launched book - Wisdom and Wit from a Safety Psychologist. I’m delighted to have been given the opportunity to revisit my old articles, partnering with the British Safety Council to publish this collection, and raise money for two wonderful mental health charities, Mates in Mind and Brawd. Collating these articles has been a fascinating way to look back over the evolution of thinking about safety through the decades. From the now-total acceptance of culture as key, through to the emergence of our understanding that wellbeing, mental health and general mindset are vital risk factors that also need the most practical, constructive and pro-active approach possible. My first job as a psychologist was studying suicides in the military, some 30 years ago. So, in some ways, this means that my career has come full circle. Last year, in the UK, we celebrated the 50th year of the famous Health and Safety at Work Act (1974). It’s enabled the UK to become a world leader in the field of workplace safety with a recent average of less than 200 people killed at work annually. Yes, of course, that is 180 or so too many but international figures when it comes to wellbeing and mental health are nowhere near as impressive – very middle of the pack. So, we must compare this figure against the estimated 4,200 working-age people who kill themselves in the UK every year. In recent times, in the UK, it’s reached a place where more students and pupils take their own lives than people killed at work. These students are the next generation moving into the workplace and more funding is urgently needed to deal with acute mental health issues, let alone long-term cost-effective and proactive initiatives and investment. We’re going to have to sort this risk factor out for ourselves inside and outside of work. There has been a sea change in our perception but there’s still mountains of work to shift. In August 2024, Graham Thorpe’s family talked openly about the fact that his death was a suicide and about his long-standing struggles with depression. (A few years ago, it would almost certainly have been announced that a famous ex-cricketer would have died at 55 of an ‘undisclosed cause’). The same week, an Australian weatherman announced live on TV that he had to hand back to the anchor as he was having an on-air panic attack. Encouragingly, the weatherman (Nate Byrne) reported that the public response afterwards was ‘entirely positive’ - essentially ‘good on you mate for being open about it’. Where we once took confident-looking people at face value, increasingly, we know that we very often don’t know what’s going on inside. We know a stiff upper lip can be hugely useful on some occasions – but a killer on others. We know that sitting around any table of ten people, typically two or three will be really struggling. We know we need to not accept ‘I’m fine thank you, how are you?’ at face value but to ‘ask twice’ if their first answer is not altogether convincing. More proactively, we need to ask ‘high value / critical incident’ based questions like ‘how did you sleep last night? And gently ask ‘why?’ if the answer is ‘terrible actually’. As part of making this book available both online, and through a limited number of hard copies, we are seeking to raise money to support two charities; Welsh mental health charity Brawd, and Mates in Mind, a sister charity to British Safety Council which works to support better mental health in the construction, transport and logistics sectors. Digging through my early pieces for this book, I realise that all of the early writings are about safety leadership, behavioural safety, and safety culture. However, about 8 years (or so) ago, when I returned from a few years off dealing with a family illness, they started to focus more and more on wellbeing and mental health at work. Initially, talking about mental health at work was quite controversial (it came long before we considered things like victim blaming). However, I’d argue simply not at all, now, as we increasingly take a holistic, integrated and humanistic approach to human error and risk management. So, as we look to the future, and consider health, safety and wellbeing at work, we need to remember that good work is good for you (because it brings meaning, purpose, banter and camaraderie) but bad work is bad for you, so it’s important how we treat our colleagues and what our organisational cultures are like. Looking out for one another in work and outside of work is a small thing that we can all do. As Brawd say in much of their literature: we need to ‘listen and be listened to’. Allow me to slightly paraphrase the famous Hollies song, ‘He Ain’t Heavy, He’s My Brother’: The road is long, with many a winding turn … be a ‘brother’. Dr Tim Marsh is a safety psychologist. His book, Tim Marsh’s Musings: wisdom and wit from a safety psychologist, can be downloaded, once a small donation has been made, from this link: Download your copy of: Tim Marsh’s Musings – Wisdom and Wit from a Safety Psychologist - JustGiving. |
|
|
|
The hidden workplace risks of cold weather | 11/12/2024 |
EMPLOYERS CAN limit the negative health impact of the cold weather, says John Kushnick. In recent weeks, winter has officially arrived in the United Kingdom. Following Storm Bert and a weekend of heavy rain, flooding and strong winds, parts of the country are now facing fallout. With unpredictable weather and a high likelihood of ice and frost comes risky working environments, especially for those in labour intensive, outdoor jobs. This is especially relevant now, due to The Royal Society for the Prevention of Accidents (RoSPA) warning that the country is "facing an accident crisis" after it’s data showed a UK-wide rise of 42% in accidental deaths over the last decade, with more than 20,000 people killed each year. Employers must protect their workers in these conditions to battle long term sick leave and ensure all employees are well cared for at work – so what should they be looking out for? How cold is too cold? Cold temperatures both make working conditions uncomfortable and pose safety risks. When hands and feet become cold, carrying out tasks can become painful, and the loss of sensation increases the risk of accidents. Cold environments can lead to loss of concentration, tiredness, and even more severe conditions like vibration white finger or muscular injuries. For these reasons, employers must ensure the workplace remains safe during the colder months. Workplace temperatures are covered by the Workplace (Health, Safety and Welfare) Regulations 1992, which place a legal obligation on employers to provide a ‘reasonable’ temperature in the workplace. The regulations suggest that the minimum temperature should be at least 16 degrees, or if the work involves rigorous physical exertion, it can be 13 degrees. There are no laws which specifically state that workers can stop working if the temperature gets too hot or cold. However, every employer has a responsibility to maintain a safe working environment and must protect the wellbeing of their employees under UK law. This legal obligation is otherwise known as ‘Duty of care’. If an employer neglects their responsibility, and this results in someone falling unwell or being injured, that person may be able to claim compensation. Reducing risks As mentioned, when working outdoors, the risks of working in cold conditions are heightened. The cold temperatures often create ice, significantly increasing the risk of falls and slips. Industries such as construction, delivery services, and outdoor maintenance are particularly affected, and it’s clearly not practical to maintain a workplace temperature in excess of 13 degrees in these environments. As such, precautions are essential for outdoor workers. Employers are advised to provide suitable equipment and protective clothing such as hats and gloves, as well as waterproof and breathable clothing for manual workers. Additionally, rotating work from cold to warm areas, or scheduling outdoor work for the warmer part of the day can help reduce health risks. Employers should also set up warm rest areas with facilities to make hot drinks, and keep air-flow to a minimum to reduce drafts and protect workers from the cold. Adjusting conditions for vulnerable employees The individual needs of vulnerable employees must not be forgotten or overlooked, such as those who are pregnant or have health conditions such as heart, circulation, or breathing issues, including emphysema. These individuals risk being more sensitive to working in cold temperatures, therefore extra precautions, such as flexible working hours, remote work options, or additional heating should be implemented. Failing to accommodate to vulnerable workers throughout the winter season could not only lead to serious health implications but also legal consequences if employers are found to have neglected their duty of care. However, keeping workers warm and safe is not just about avoiding legal issues; it’s about ensuring employee wellbeing and maintaining productivity during the winter months, no matter the personal circumstances. It is critical that employers take their duty of care seriously. By conducting risk assessments, providing the right protective measures, and adjusting working conditions where necessary, they can prevent staff from falling unwell or being injured. In turn, this will help to boost productivity and maintain the health of the workforce – something that will only grow in importance as the Labour government endeavour to ‘Get Britain Working’ and remedy the increasing rate of workplace sickness across the country. John Kushnick is legal operations director of National Accident Helpline |
|
|
