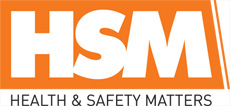
![]() |
Mark Sennett
Managing Editor |
![]() |
Kelly Rose
Editor |
Home> | Breathing Safely | >Breathing Air | >Know your limits |
Home> | Breathing Safely | >Dust and Fume Extraction | >Know your limits |
Know your limits
02 April 2024
Bob Latimer discusses monitoring and control limits for dust and fumes in the work environment.

WORKPLACE SAFETY regulations are crucial for safeguarding the health and wellbeing of employees across a multitude of industries. Among the hazards encountered in many workplaces are dust and fumes which can pose significant health risks if not properly controlled. In the United Kingdom, there are stringent regulations and guidelines in place to ensure the protection of workers from exposure to a potentially harmful workplace environment.
This article delves into the importance of the regulatory frameworks governing these hazards and setting appropriate workplace control limits. Further, the use of an automated monitoring and reporting system for both dust and fumes in industrial workplace environments is presented as a powerful element of a facilities ongoing Health and Safety Compliance strategy.
Health risks of dust and fumes
Many industrial environments can be inherently hazardous with dust and fumes being common byproducts of transformative processes, including metalworking, woodworking, plastics manufacturing, textiles and apparel, construction, mining, waste management and agriculture. These substances can consist of various particles and chemicals, some of which are known to be hazardous to human health.
Inhalation of dust (particulate matter or PM) can lead to respiratory issues, such as asthma, chronic obstructive pulmonary disease (COPD), and even lung cancer. Exposure to high levels of volatile organic compounds (VOC) can cause irritation of the eyes, nose, and throat, as well as headaches, dizziness, and fatigue. Some VOCs are also known to have long-term health effects, including cancer and damage to the liver, kidneys, and central nervous system.
In 2022, the UK government DoE National Statistics show that around 40% of PM10 and 30% of PM2.5 emissions in the UK were attributable to ‘industrial processes and product use’ which largely includes steel production and the use of manufactured products such as solvents, adhesives and lubricants.1
Dust
Particulate matter (PM) refers to tiny particles or droplets in the air that are composed of various substances. The terms "respirable particles" and "inhalable particles" refer to different size ranges of airborne particles that can enter the lungs.
Figure 1 Visualisation and comparison of PM2.5 and PM10
The main difference between respirable and inhalable particles lies in their size range and their ability to penetrate into different parts of the respiratory system. Inhalable particles tend to get trapped in the upper respiratory tract, while respirable particles are smaller, typically less than 10um and can penetrate deep into the lungs. Very small particles can pass contaminants across the alveolar-capillary membrane and enter the bloodstream, potentially causing more serious health issues for example cardiovascular problems.
Figure 2 Respirable particles can be categorised based on respective upper size limit in micrometres (µm). Smaller particles penetrate deeper into the respiratory tract.
Fumes
Total Volatile Organic Compounds (TVOC) refers to the collective measurement of various organic compounds that exist as gases in the air. These compounds can be released from a variety of sources including solvents, paints, coatings, cleaning products, plastics, resins, metal-working fluids, printing, and packaging.
Companies can mitigate TVOC emissions in manufacturing environments by implementing various strategies, including switching to low/no-VOC materials, improving ventilation systems, process optimisation and control, provide ongoing personnel training and personal protective equipment for workers. Additionally, real time TVOC monitoring can be an invaluable alert tool, however knowledge of the VOCs in use or being produced is needed and control values need to be selected based on the workplace or procedure carried out.
UK Workplace Exposure Limits
The UK Health and Safety Executive (HSE) COSHH EH40/2005 is a publication that provides Workplace Exposure Limits (WELs) for various hazardous substances. WELs are legal limits on the concentrations of hazardous substances in the air within the workplace. They are intended to protect the health of workers by ensuring that exposure to harmful substances is kept below levels known to cause adverse health effects. WEL values are generally specified for two time periods.3
- long-term, 8 hour TWA (time weighted average)
- short-term, 15 minute short term exposure limit (STEL)
Limits are expressed in units of either parts per million (ppm) or milligrams per cubic meter (mg.m-3) or both. Generally, VOC values are best handled using ppm and dust using mg.m-3.
Dust limits
It is important to note that not all dust types are covered in the EH40 document while some dusts have been assigned specific WELs, for example crystalline silica, some metal dusts, wood dust etc.
However, the COSHH definition of a substance hazardous to health includes “dust of any kind when present at a concentration in >10 mg.m-3 8-hour Time-Weighted Average (TWA) of inhalable dust or 4 mg.m-3 8-hour TWA of respirable dust.” These “blanket” concentration limits effectively means that any dust will be subject to COSHH if operators are exposed to dust above these levels.
Even with the COSHH regulations in place there exist arguments for even lower limits. The COSHH values for particulate limits are very high when compared to the current UK Air Quality Regulations 2010:
The Air Quality Standards Regulations 2010 require that concentrations of PM in the UK must not exceed:
- An annual average of 40 µg. m-3 for PM10
- A 24-hour average of 50 µg. m-3 more than 35 times in a single year for PM10
- An annual average of 20 µg. m-3 for PM2.5
(It is important to note that when comparing the COSHH values and the UK Air Quality Regulations that 1mg. m-3 = 1000 µg.m-3 )
Scientific evidence considered by the UK HSE Advisory Committee on Toxic Substances (ACTS) suggested that the current UK limits for inhalable and respirable dust of 10 mg.m-3 and 4 mg.m3 respectively, are not safe. In 2011, the Trade Union Congress (TUC) published a position that the current levels are inadequate when it comes to protecting workplace health, recommending 1mg.m3 for respirable dust and 2.5mg.m3 for inhalable.2
VOC limits
There are legal limits in place for exposure to VOCs in the workplace with hundreds of substances having specific exposure limits. High risk materials such as benzene, have very low exposure limits,1 ppm (8-hour TWA), whereas acetone, has a limit of 500 ppm (8-hour TWA), and even similar materials such as alcohols have very different values.
Setting appropriate control limits
Setting appropriate workplace control limits for dust and fumes involves a thorough assessment of the potential health hazards and risks associated with specific substances. This may involve sampling air quality, measuring particle concentrations, and evaluating ventilation systems to determine the effectiveness of control measures currently in place.
Once the risks have been assessed, employers can implement control measures to reduce exposure levels below the established WELs. This may include engineering controls, such as local exhaust ventilation systems (LEV), dust suppression techniques, and the use of enclosed work processes to minimise the release of dust and fumes into the air. Personal protective equipment (PPE), such as respiratory masks and protective clothing, should also be provided to employees as a secondary control measure.
Regular monitoring and review of control measures are essential to ensure that exposure levels remain within acceptable limits. Employers should conduct periodic air quality testing and health surveillance to monitor the effectiveness of control measures and identify any areas for improvement.
Automated continuous monitoring systems for dust and fumes
PM and TVOC are both useful indicators of air quality in the workplace and continuous monitoring of these levels in the workplace can help identify sources of indoor air pollution and assess the effectiveness of ventilation and air filtration systems in reducing exposure.
It is important to note that the use of continuous environmental monitoring systems for PM and TVOC is NOT a replacement for formal risk assessment studies conducted by qualified occupational hygienists. However, such assessments are by their nature limited to a “snap-shot” in time and can be augmented by ongoing automated monitoring against established baseline profiles. Any changes or adverse trends can be identified, triggering further investigation.
The ASYS dBELL continuous monitoring system comprises a comprehensive range of scalable tools designed to make the task of demonstrating compliance easier.
1. Helps build a baseline signature of workplace noise and airborne hazards.
2. Supports assessing and validation of mitigation strategies.
3. Provides ongoing monitoring with periodic automated reporting.
Deploying the ASYS dBELL continuous measurement system provides the Health & Safety professional with a comprehensive baseline picture of Noise and Air Quality in the workplace. Armed with quality baseline data, it is then possible to deploy noise and airborne-hazard mitigation strategies and assess their subsequent effectiveness. Ongoing continuous area monitoring forms a critical alert mechanism to any unexpected shifts in baseline conditions or unusual trends during work and process operations. Facility-tailored work-shift status reports including charts, alerts and action limits are presented clearly making it easier to assess compliance to regulatory guidelines and standards.
Protecting workers from the health hazards associated with dust and fumes exposure is paramount in the workplace. Setting appropriate control limits in accordance with regulatory guidelines helps to minimise the risks and ensure the safety and wellbeing of employees. By conducting thorough risk assessments, implementing effective control measures, and monitoring exposure levels, employers can create a safer working environment and prevent long-term health complications associated with dust and fumes exposure.
References
1 Dept. for Environment, National statistics, Emissions of air pollutants in the UK – Particulate matter (PM10 and PM2.5), Updated 19 February 2024
2 Dust in the Workplace: Guidance for Health and Safety Representatives. 2011
3 Health and Safety Executive, EH40/2005 Workplace exposure limit.
Bob Latimer is product engineer at National Photonic. For more information, visit www.nationalphotonic.com
- Monitoring airborne hazards and noise
- Monitor workplace noise and airborne hazards
- The new ASYS dBELL system for workplace dust, fume and noise
- Monitoring system for workplace dust, fume and noise
- Air quality and noise monitoring system
- See the new ASYS dBELL at SHW Live
- Detecting danger
- Powerful monitoring system