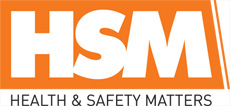
![]() |
Mark Sennett
Managing Editor |
![]() |
Kelly Rose
Editor |
Home> | Breathing Safely | >Dust and Fume Extraction | >Detecting danger |
Home> | Breathing Safely | >Gas Detection and Monitoring | >Detecting danger |
Detecting danger
27 March 2023
Craig Cowbrough talks to Mark Lynch of DMH about his use of cloud connected environmental sensor technology to help deliver better health and safety outcomes in the workplace.

MATERIALS HANDLING, fabrication and finishing can have an adverse impact on workplace noise and air quality requiring risk mitigation and controls supported by ongoing monitoring. For example, every year in the UK, breathing hazardous metal fume at work impacts welders’ health with severe cases being hospitalised, while workplace noise results in several thousand cases of hearing problems either directly caused or exacerbated.
Compounds found in solvents, cleaners, rust inhibitors, and degreasers etc, can have long term health impacts including liver and kidney damage as well as neurological conditions. Many volatile organic compounds (VOCs) have specific health risks including short term irritation of the eyes, throat and lungs, dizziness, nausea and headaches.
According to Health & Safety Executive (HSE) statistics 12,0001 deaths were reported as a result of lung disease from past exposures at work last year. Annually, there are an estimated 19,000 new cases of lung or breathing problems believed to be caused or made worse by the working environment.
Regulations and compliance
The workplace environment has come a long way since the introduction of the Health and Safety at Work Act in 1974. Critical milestones include the Noise at Work Regulations and the Control of Substances Hazardous to Health (COSHH) regulations, both implemented in 1989.
It’s easy to take health and safety for granted, yet it is a vital component of industry that ensures everyone stays safe while at work.
Employers have a legal obligation to protect their employees from workplace hazards, including noise (average and peak) and airborne contaminants such as respirable particulate matter (PM) as well as volatile organic compounds (VOCS).
To ensure a safe working environment, the HSE recommends regular monitoring and measurement of noise and airborne hazards in any premises that has a risk to employees’ health and safety, whether it be a garage, workshop, timber yard or spray paint shop.
When the HSE changed its regulations2 relating to weld fume exposure it highlighted some new challenges for manufacturers and fabricators.
It had identified new scientific evidence to suggest that exposure to all welding fume, including mild steel welding fume, can cause lung cancer. There was also some limited evidence linking fumes to kidney cancer as well. The scientific evidence comes from the International Agency for Research on Cancer. The Workplace Health Expert Committee has endorsed the reclassification of mild steel welding fume as a human carcinogen.3
In light of this the HSE decided to tighten enforcement legislation in relation to the control of exposure of welding fume and all businesses undertaking welding activities should ensure effective engineering controls are provided and correctly used to control fumes.
Further, the HSE would now no longer accept any welding undertaken without suitable exposure control measures in place, as there is no known level of safe exposure.
Last year metalworking businesses in South Yorkshire were the focus of a HSE campaign4 following an ‘alarming rise in incidents’ involving breaches of particle air quality legislation.
Firms which used welding and metalworking fluids were the main focus of the clampdown.
During the week-long operation inspectors visited more than 70 businesses identified as operating in a high-risk sector or performing poorly.
The businesses spanned metal fabrication, engineering, general manufacturing, waste and recycling.
A HSE spokesperson said that businesses needed to demonstrate they were managing risks to protect workers, or they could face an enforcement notice or prosecution.4
Embracing regulatory change
Inverness based DMH is one of the companies impacted by the changes to the regulations. They are a small, light engineering and blacksmiths working across the north of Scotland. They manufacture everything from gates and stairways to bridges and telecommunication towers.
“When the legislation changed, we had to think differently about how we protected our workers involved in the day to day activities in the workshop,” said DMH’s managing director, Mark Lynch.
“With health and safety, you have to understand what the issues are and then put in reasonable processes and procedures to mitigate them.
“Fundamentally the whole idea of what we were trying to do, is you can put in place mitigation strategies, but how do you know it is working and how do you manage it? How do you know when to make changes if circumstances change?’
“For our welders that meant PAPR air-fed helmets being introduced to keep harmful particulates away from their faces. However, there may be other workers on the premises carrying out other tasks related to fabrication marking up a job or grinding something.
“We then looked at an extraction table which basically took the air, filtered it, and recirculated it. We also installed extractors directly on welding torches to take fumes away.
“However, during a routine visit from HSE, while explaining what we had done to reduce harmful particulates I thought, ok, we’ve put all these processes and procedures in place to make the workplace safer, but how do we know if they are working?
“So, we looked at ways of measuring what we were doing. For us the noise monitoring within the workshop was also an issue. How did we know we were consistently staying within the safe limits,” said Mark.
“We can get people in to measure noise at any given time, but that’s not giving you a true picture of the situation. So having an air quality and noise monitoring system together seemed like a good solution for us.
“The dBELL system helped us quantify what our issues were and helped manage processes to mitigate potential hazards in the shop. The real time reporting element of the system can help ensure that you monitor the steps you’ve taken are still working, giving you a benchmark to monitor against and make further changes if needed,” he explained.
It’s not just light engineering workshops like DMH that will benefit from an automated, continuous monitoring system for noise and air quality. Any premises where noise, airborne particles and VOC’s are a concern will benefit from the deployment of the dBELL system making it easier for the business owners to demonstrate compliance to regulatory guidelines and standards.
A flexible system that can monitor the general environment as well as pulling data from remotely deployed or wearable devices enables the health and safety manager to manage risk more effectively.
Armed with quality baseline data it is possible for those responsible for site health and safety to develop a better understanding of air quality and noise levels within the premises. Giving them the ability to quickly adapt to any changes in levels that could potentially have an impact on employee wellbeing.
Adding ASYS dBELL series IIoT devices for personal exposure dosemetry, handheld measurement or remote deployment, forms a flexible system that can be adapted to meet the workplace monitoring requirement and conduct effective in-house environmental studies.
Installation is straightforward. Simply mount the ASYS dBELL100 area monitor then create an ASYS Cloud account. Optionally download the dBELL iOS/Android App to view metrics, trends and reports on your mobile devices.
The solution that Mark implemented helped him efficiently comply with the new rules.
“It can be a valuable tool to help ensure you are keeping your workplace and employees safe, in a cost effective manner,” he added.
Setting appropriate control limits
It is important to note that continuous environmental monitoring for noise, particles and volatile organics is not a replacement for formal risk assessment studies conducted by qualified occupational hygienists. Such assessments are by their nature limited to a “snap-shot” in time but can be greatly augmented by ongoing automated monitoring against an established baseline picture.
Establishing an appropriate action limit hierarchy should be based upon the baseline levels observed in the controlled environment, guided by formal risk assessment studies and regulation where limits exist.
Noise limits
The Control of Noise at Work Regulations L108 (2005) applies to all types of industries in Great Britain and is designed to ensure that workers are protected from hazardous levels of noise. Lower and upper action limits in addition to absolute exposure limits exist for both average and peak noise.
Particulate matter (PM) limits
Legal limits for exposure to dust in the workplace are defined in the EH40 document where general dust limits exist for PM4 (respirable) and PM10 (inhalable). The limits are tighter for certain higher risk materials such as crystalline silica, some metal dust and wood dust. In addition, guidance on general ambient limits can be found in the Air Quality Standards Regulations 2010 (UK) for PM2.5 and PM10.
Total Volatile Organic Compounds (TVOC)
EH40 defines legal limits for exposure to VOCs in the workplace, with 8-hour TWA and short term (15-minute) STEL values listed. Each VOC has different exposure limits due to some knowledge of the specific VOCs in use (or being produced) is needed and values need to be selected based on the workplace or procedure carried out. While this does make automated TVOC monitoring more difficult, changes or trends observed in either the general workplace environment, or at specific process locations can easily be spotted, triggering further investigation.
National Photonic, an ASYS Corporations’ UK partner, makes it easy to get the help you need when you need it.
References
1 https://tinyurl.com/ycx9znta
2 https://www.hse.gov.uk/welding/protect-your-workers/index.htm
3 https://tinyurl.com/4rmy5d97
4 https://www.bbc.co.uk/news/uk-england-south-yorkshire-59952888
Mark Lynch is director at DMH Ltd and Craig Cowbrough is an industrial journalist. For more information, visit www.nationalphotonic.com
- The new ASYS dBELL system for workplace dust, fume and noise
- Know your limits
- Powerful monitoring system
- See the new ASYS dBELL at SHW Live
- Monitor workplace noise and airborne hazards
- Monitoring airborne hazards and noise
- Air quality and noise monitoring system
- Monitoring system for workplace dust, fume and noise