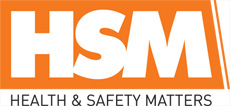
![]() |
Mark Sennett
Managing Editor |
![]() |
Kelly Rose
Editor |
Home> | Handling & Storing | >General Handling | >Taking stock of safety |
Home> | Handling & Storing | >Safer Manual Handling | >Taking stock of safety |
Home> | Handling & Storing | >Warehouse Safety | >Taking stock of safety |
Taking stock of safety
23 September 2021
As warehouse operations become more complex to handle customer demand, Jon Divers explains five key risk areas for 360-degree protection.
WAREHOUSE SAFETY has always required careful attention, but as operations become more complex to handle the rapid rise in customer demand, it is no longer enough to address risk in isolation.
With organisations looking to ever more automated and connected processes to meet new efficiency and productivity objectives, the warehouse must be considered in its entirety – with a holistic approach to the 360-degree protection of five key areas.
-
Protecting people
The safety of people is and always will be the number one priority within the warehouse, and not just of those operating equipment; research has shown that pedestrians are often the most likely to be harmed in the event of an incident. Providing regular certified training and materials handling equipment fitted with the latest safety solutions will therefore help reduce the risk of accidents and improve safety for all employees.
On-board cameras, scanners or sensors, for instance, can be used to continuously scan for potential obstructions in a truck’s path. Intelligent systems are available that can scan the hazard area using stereo cameras to recognise obstacles and differentiate between people and objects. When an obstacle is detected and identified, the system will deliver audible and visual alerts for the driver, while automatically slowing the truck to ‘crawl’ speed or ultimately stopping the vehicle in emergency mode.
With many organisations experiencing increasing demand for a faster, more agile supply chain, extra workers around peak periods such as Black Friday are often deployed in the warehouse, increasing the associated risk of accidents. Alongside implementation of the safest equipment, the use of automation can minimise the number of workers required on the warehouse floor to reduce accidents, enabling individuals to be redeployed to other, more low-risk areas of the operation.
-
Moving goods
With the working environment of warehouses and distribution centres continuously evolving to cater toward modern warehousing solutions – how will man and machine work together safely? There may be fewer workers on the shop floor in a more automated environment, but companies need to think carefully about the new risks created when the workforce is operating alongside robots and AGVs.
The development of advanced forklift truck technologies, from sensors and remote controls to on-board cameras and collision protection are ensuring that the safety of pedestrians is of the highest priority. Anything from floor spots that shine a light onto the warehouse floor, audible warnings or anti-collision systems can be fitted to equipment to warn of their approach and avoid accidents.
New innovations in forklift truck technology are crucial in continuing to reduce risk. It’s vital that organisations look at advancements in intralogistics technology, not only to help drive efficiencies and optimise their operations but also utilise the technology to enhance safety for those workers on the frontline of all operations within the warehouse.
Goods stored within the warehouse are a valuable asset to be protected at all times from loss or damage. At the same time, an efficient supply chain that handles goods quickly, reliably and to the highest standard delivers the most competitive advantage. It can even be argued, in the age of eCommerce, that a fast and convenient service is now more important to an organisation and its customers than the goods themselves.
Assistance systems therefore exist to ensure goods are manoeuvred both safely and efficiently around the warehouse. Technology however, is not enough on its own, especially within a fast-changing warehousing model. Operator training is a crucial part of safety and engineers contribute significantly to this. It’s the combination of people, processes, equipment and software that will successfully safeguard employees and create a collaborative warehouse.
-
The warehouse
As demand on the warehouse rises, organisations are forced to look at new and innovative ways to maximise their operations and optimise space. The increasing complexity and demands within the warehouse environment are, by default, creating new safety risks. For example, the stepped changes in volume or product profile can result in extra workers on the floor with the inherent associated risk of collision.
For example, the advancements of indoor positioning systems is a digital safety solution for locating industrial trucks inside the warehouse. This type of system can offer a position-based analysis of stacker movements, which can be viewed live or retrospectively using a web-based application. This means that each stacker can be paired with a smartphone that communicates with Bluetooth transmitters – so-called “beacons” – placed throughout the warehouse.
-
Equipment and machinery
With regular maintenance in combination with the relevant safety assistance systems, organisations can reduce the risk of forklift truck accidents for the safest possible environment for employees, and the long-term performance of equipment. Preventing accidents also plays an important part in protecting your machines and vice versa. If a truck does experience an impact, warehouse managers need the data fast to assess the damage and future risk, which shouldn’t be the responsibility of the operator alone. Shock sensor technology, for example, can be retrofitted to a truck to record the effect of a shock in the event of an accident. The sensor module reacts to impacts and sets off an acoustic and visual warning. The truck automatically shuts down and the data can be collected for the necessary analysis straight away, preventing any risk of the incident going unnoticed.
-
Securing systems and data
As the warehouse becomes an increasingly connected and digitalised environment, data is the lifesource to generating greater efficiency and productivity gains. A robust and secure software and / or web application to assist in the protection of data should now be a key component of every safety strategy to avoid breaches and protect from unnecessary downtime. It’s imperative that all internal material flows in the warehouse are administered and managed safely, with certified safety solutions, to guarantee secure communication of systems. By harnessing data correctly, the return is a host of invaluable business information such as fleet management tools. This can provide reliable protection of data and equipment, alongside concrete, consolidated information to underpin future decision making.
Safely moving forward
As organisations look at ways to increase throughput and reduce costs in order to meet the demand for just in time delivery, the warehouse is undergoing huge change, which must be achieved without compromising workforce safety. But this is not an either/or situation. A holistic approach on the journey to Warehouse 4.0, considering every aspect of a warehouse and the people, processes, equipment and software within it, will deliver the greatest levels of efficiency and ensure 360-degree protection. Once warehouses are equipped with the right skillset, technology and safety features, organisations will be able to move their business forward and fully embrace the new more efficient, productive and safer warehouse of the future.
Jon Divers is customer service director at Jungheinrich UK. For more information, visit www.jungheinrich.co.uk