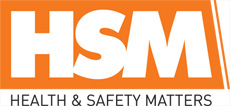
![]() |
Mark Sennett
Managing Editor |
![]() |
Kelly Rose
Editor |
Source sustainable
02 December 2021
Natalie Wilson highlights the importance of sustainability in PPE and technical workwear for 2022 and beyond.
SUSTAINABILITY IS a buzz word for so many, but one that that we are still only truly starting to understand in the context of PPE and workwear. This is partly because what we think we know about sustainable practices one day can quickly become obsolete as new innovative processes are developed.
In the last two years, we have also seen how the pandemic saw the global market for disposable single-use products ‘break’ the supply chain, as the volumes demanded by consumers (commercial and private) was totally unsustainable – both in terms of the environment and in terms of the viability of the supply routes.
This has acted as a catalyst for change, highlighting the need for action and for the whole industry to review current sourcing and manufacturing practices.
While sustainability has been discussed in various forms for a number of years, there is increasing pressure across public and private sectors for organisations to be more focussed on the environmental impact of their operations, as well as focussing on social value, sustainability and issues such as modern slavery.
This is leading to a drive from users for industry to push forward with innovations which can improve the sustainable credentials of their PPE and technical workwear, including offering opportunities for circularity and cradle-to-grave solutions.
To ensure that PPE and technical workwear items are sustainably sourced, there are 5 key considerations that are explored below, with some initiatives having immediate impact and others that can be introduced over time:
-
High quality garments that are built to last – these need replacing less frequently and subsequently have a greatly reduced environmental impact
-
Raw material and trims selection – this can be critical to the sustainable credentials of any product and need to be introduced during the design phase of any new product development
-
Global footprint of the component parts – while the manufacturing source can be in one part of the world, the raw materials and trims are usually sourced from elsewhere, so understanding the total journey of a garment is important
-
End-of-life processing of PPE and technical workwear – security is a key issue and always has been in the end-of-life disposal of garments, particularly for branded items, but transparency of the steps within this process is also important
-
Ethical and sustainable procurement practices – for end user buyers, but also for all Economic Operators within the supply chain, considerations on how and what we define within the scope of ethical and sustainable procurement must ensure the entire supply chain is considered
Garments that are built to last
Designing, manufacturing and procuring garments that are built to last years, rather than months, will have the biggest and most immediate impact on sustainability.
In almost all cases, this will require a change from buyers looking at price per item, to cost over the life of a garment, as well as the environmental impact of each product.
For example, comparing a standard PPE trouser to one which is designed to withstand industrial laundry processes can offer significant cost savings.
Standard PPE trouser: Two issued per person, per year @ £18 each
Over a three-year contract = six pairs of trousers / £108 per wearer
Industrially launderable PPE trouser: Three issued per person, for the duration of the three-year contract @ £25 each
Over a three-year contract = three pairs of trousers / £75 per wearer
While the initial garment price is more expensive, there is a 30% garment cost saving over the life of a three-year contract.
In addition, there are 50% fewer garments being issued which has the additional benefit of saving 50% of water, CO2 emissions, packaging and end-of-life waste materials generated through the production and delivery of the trousers.
Raw material and trims selection
Understanding the raw materials being used in any garment is key to ensuring the durability of the product and fitness for purpose, whether that’s for a high visibility softshell jacket or a flame retardant coverall.
Depending on the required performance or certification of a garment, there are a variety of sustainable raw materials that can be used.
These include everything from organically grown cotton; fibres derived from waste sources such as PET plastic bottles, coconut husks or leftover coffee grounds; sustainable & fast-growing natural resources such as bamboo or birch; through to recovered fibres from garments at end-of-life. These fibres can have reduced environmental footprint of between 30-70% compared to virgin fibres, based on a mix of water usage and CO2 emissions (primarily depending on fibre type). However, in order for these fibres to be successfully used, they must be robust enough to match the longest possible life of a garment constructed from their ‘as new’ equivalents in order to keep the total volume of garments as low as possible.
Global footprint of component parts
This is an area which can be more difficult to track without real transparency across the supply chain. For example, whilst a garment manufactured in a near-shore factory may on the face of it seem absolutely lower carbon impact than an equivalent garment from a factory further afield, if the fabrics and trims have travelled thousands of miles before reaching the near-shore factory, there may not be as much difference as first appears to be the case.
It also requires fairly complex calculations to understanding if there is any difference between carbon emissions if a fabric is travelling from China to Turkey, before being manufactured and shipped as a finished item into the UK; compared to an Indian fabric being sent to Sri Lanka for production and then shipping into the UK.
An easier calculation for example, would involve UK fabric being made into garments in a UK factory, which would be the lowest possible carbon emissions and all aspects of the supply chain’s ethics, modern slavery performance and quality systems are much easier to audit and observe.
End-of-life processing
The complex construction of PPE and technical workwear has historically made these items more difficult to provide effective end-of-life processes but major advancements in processing these items means there are now a variety of providers offering these services.
When considering options for end-of-life processing, once again, it’s important that the design phase of any new product development incorporates the full cradle-to-grave requirements of each item.
The ultimate goal for end-of-life management of any garment is to create a circular economy which would see textiles being recycled back into textiles. In some areas, as an industry we have been able to achieve these goals but these are primarily applicable for single fibre fabrics such as polyester which can be processed back into the textile supply chain.
Ensuring transparency of who is responsible for each part of the process is key to understanding exactly what’s happened to an item and how it’s re-entering the supply chain.
Sustainable procurement processes
Often sitting slightly outside the ‘sustainability’ part of a buying process, the true meaning of sustainable procurement means that each company within the supply chain is able sustain their own businesses financially. Without this, staff can’t be paid, corners could be cut, and the supply chain could collapse.
The importance of commercial aspects such as payment terms from the end user through to the raw material suppliers should be considered in the sustainable procurement of PPE and technical workwear, as well as the ethical and environmental aspects of sustainability.
Natalie Wilson is managing director at Shield 360. For more information, visit www.shield360.co.uk
- Issues with workplace mental health first aid
- Government unveils significant reforms to employment rights
- Underground cables safety alert
- £400k fine after worker trapped by hydraulic ram
- Company fined after worker's hand crushed
- Work fatalities rise 'a sobering reminder' of cost of failure
- Haulage company employee electrocuted
- Man spared jail for unsafe work on his home
- Britain’s overtime culture putting lives at risk
- Company fined after worker injured by forklift