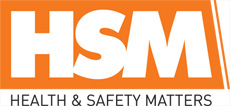
![]() |
Mark Sennett
Managing Editor |
![]() |
Kelly Rose
Editor |
Home> | Slips, Trips & Falls | >Fall Prevention | >Step in the right direction |
Home> | Slips, Trips & Falls | >Fall Protection | >Step in the right direction |
Home> | PPE | >Safety Footwear | >Step in the right direction |
Step in the right direction
11 October 2022
Having the right footwear is one of the measures that can help avoid slips and trips in the workplace. James Abbott explains what you need to know about slip resistant footwear.

The reality is that appropriate footwear and other measures have proven to be able to reduce slips occurring by over 50% in the workplace!
STFs are still the biggest cause of accidents at work, and in 2020/21 alone 441,000 workers sustained a non-fatal injury according to self-reports from the Labour Force Survey in 2020/21 (LFS), resulting in time off work.
At least 33% were as a result of STFs. That’s equivalent to 413 accidents each day, 90% of the slips result in broken bones. This doesn’t include the many accidents such as falls from height which can also be initiated by a slip.
The human costs of these accidents are incalculable and individual fines to businesses in the past have exceeded over £400,000.
A pretty good reason to test footwear I think you’ll agree!.
Slip resistance is a Personal protective Equipment claim made on all but the most specialist safety, protection and occupational footwear. All marked claims of slip resistance on an item of footwear constitute a claim under the PPE regulation (425/2016) and must be covered by category II (Module B) Certification. Footwear must carry the CE mark to be placed on the EU market and from 1/1/23 must carry a UKCA mark to be legally placed on the UK market. The footwear must be covered by a valid EU or UKCA type examination certificate and be supported by a declaration of conformity.
Please be aware of product on the market that claims any type of slip resistance but doesn’t carry the above markings.
Reducing slips and falls
Firstly, it’s important to differentiate slips from falls, the act of slipping increases the likelihood of a fall, however there are various factors which influence whether a slip leads to a fall or not. For example, human factors like balance and strength and mechanical factors like friction, heel angle and sliding distance.
For work footwear we focus on trying to decrease the likelihood of the slip, and this is a vitally important metric to consider when selecting your work footwear.
In the UK and EU we use the EN ISO 13287:2019 test method to measure the coefficient of friction (CoF) between the footwear and selected floor surfaces and lubricants. It’s a mechanical test used to simulate the action of slipping and is based on the biomechanics of normal walking. Each shoe put through the test is given an individual CoF result, the higher the result the better the footwear performed against that surface and contaminant. This test method is used as part of EN ISO 20344, 5, 6 & 7 suite of standards where the requirements can be found. These are used for all PPE footwear items bearing the CE and/or UKCA mark.
To put these results into context it’s generally accepted information that if the CoF is below 0.24 then it is highly likely that a slip will occur during normal walking. A higher figure will reduce the likelihood of slipping accidents. It is also generally accepted that at a CoF value of 0.36 there is a low risk of slip. You will note that the requirements in the EN ISO standards are the test surfaces and lubricants in the standards are designed to challenge the footwear more than a conventional workplace.
Slip testing in footwear has a long history in UK/EU and it only became an industry standard in 2007 when the first testing was implemented, so people could buy Personal protective footwear which met a minimum standard of slip resistance.
Down the years various test methods have been considered, including attempts to include the human element into the testing, however, so far these have been deemed not be able to provide consistent and fair results at scale thus never mass adopted. Therefore, the machine used in the current test is widely considered to be the best available.
Slip Resistance Test Standards & Changes
In EN ISO 20345:2011, EN ISO 20346:2014 and EN ISO 20347:2012 the footwear carries marking of SRA, SRB or SRC to show that it passed the minimum requirements of one or more of the modes of slipping. These are as follows:
Marking |
Test surface and lubricant |
Mode of test |
Minimum CoF requirement |
SRA |
Ceramic tile with Sodium Lauryl sulphate lubricant |
Forward slip on the HEEL |
0.28 (correction -0.03) |
Forward slip FLAT |
0.32 (correction -0.07) |
||
SRB |
Steel with Glycerol lubricant |
Forward slip on the HEEL |
0.13 |
Forward slip FLAT |
0.18 |
||
SRC |
BOTH of the above conditions and requirements have been met |
(The correction factors are applied before the result is quoted)
The EN ISO standards for personal protective equipment footwear category have recently been revised. As part of that revision, a review of the current slip resistance testing was carried out. The revised footwear standards (ENISO 20345:2022, EN ISO 20346:2022 and EN ISO 20347:2022) the SRA, SRB, SRC markings will no longer be used. However, the new standards are not currently harmonised in Europe or designated in the UK so should not be used at this stage for certification. In addition, most labs will not be accredited to test to the new method either. It is likely that the “SRA, SRB & SRC” will remain in use for many years to come.
The main changes are listed below alongside an illustration of the new test method;
-
The test now is performed on the heel and the forepart of the footwear – the flat footwear is no longer assessed.
-
The steel floor type has been replaced by a ceramic tile in the glycerol test.
-
The test requirements found in EN ISO 20345:2022, EN ISO 20346:2022 and EN ISO 20347:2022 now include the “correction factor” so the requirement for Heel slip on tiles with the sodium lauryl sulphate appears higher 0.31 but in fact remains the same. Its considered mandatory to do the sodium laurpl sulphate test so no marking will be required.
-
SR will be the new marking on the shoe when its been put through an additional slip resistant test using glycerol.
Marking |
Test surface and lubricant |
Mode of test |
Minimum CoF requirement |
NO MARKING |
Ceramic tile with Sodium Lauryl sulphate lubricant |
Forward slip on the HEEL |
0.31 |
Backwards slip on the FOREPART |
0.36 |
||
SR |
Must meet the above requirements and in addition: - |
||
Ceramic tile with Glycerol lubricant |
Forward slip on the HEEL |
0.19 |
|
Backwards slip on the FOREPART |
0.22 |
||
Ø |
Specialist product with spikes or similar – the requirements above cannot be met |
The reason the forepart of the shoe is now tested instead of the flat part of shoe is because approximately 70% of accidents occur at the heel and 30% at the forefront of the footwear, so it’s considered more relevant to the risks its looking to reduce. In addition, during normal walking when the shoe is flat, there is little or no momentum either forward or backwards. The slip performance of a flat shoe offers very little information to the user and can hide a poor “toe off” slip performance.
How to consider footwear for your workplace to reduce slips
Most work footwear manufacturers don’t publicise their slip test results; however, this information is freely available on request from the manufacturer, and it could be used to narrow down your selection especially given the plethora of options available on the market. You could even go as far as to commission some specific testing using your surfaces and contaminants.
However, it should be noted that slip testing alone should not be the only factor considered and it has its limitations. For example, current test methods don’t mimic walking on loose ground where tread patterns can be clogged with mud or gravel leading to a decrease in the slip resistant performance of the footwear.
Its strongly recommended that all footwear options are trialled by employees this increases the likelihood of buy in and compliance. I’ve listed some other considerations below.
Durability – Footwear is generally tested when its brand new, it can lose slip resistance over time as the cleated pattern wears away. A combination of durability and slip resistance should be considered and its optimal to monitor it throughout its life which might include periodic inspection and recording of slip-related incidents.
Comfort – If the footwear isn’t comfortable, ensuring compliance can be much more challenging thus increasing the risk of accidents.
Sizing – Incorrectly fitted footwear can increase the likelihood of a slip or trip. ‘Sizing sessions’ can be helpful in ensuring this is done correctly as the fittings from different brands may vary.
Outsole Material – If prioritising for slip resistance in wet conditions rubber is going to give you the best results over all other alternatives. Some manufacturers will offer specific rubber compounds which are optimism for slip resistant performance.
Tripping Hazards – Some footwear has bulky features which could be deemed a tripping hazard.
Sole pattern matches the environment – For example in wet environments (Without any/much solid contaminant) the outsole should have good contact with the ground and be able to disperse liquid disperse liquid quickly and effectively.
Above all it’s about putting the safety of your people and business first.
James Abbott is head of sales at Anvil Traction. For more information, visit www.anviltraction.com