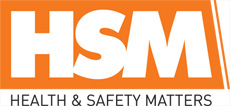
![]() |
Mark Sennett
Managing Editor |
![]() |
Kelly Rose
Editor |
Home >MARTINDALE ELECTRIC OUTLINES ESSENTIAL SOLUTIONS TO HEALTH & SAFETY COMPLIANCE DURING THE MAINTENANCE OF PLANT AND EQUIPMENT
MARTINDALE ELECTRIC OUTLINES ESSENTIAL SOLUTIONS TO HEALTH & SAFETY COMPLIANCE DURING THE MAINTENANCE OF PLANT AND EQUIPMENT
18 July 2017
Steve Dunning, managing director at Martindale Electric outlines essential solutions to health & safety compliance during the maintenance of plant and equipment.
From February 2016 new tougher sentencing guidelines were introduced for health & safety offences, the objective being to drive compliance and reduce the number of accidents in the work place. The guidelines are directly applicable to electricity related accidents and cases where employees are put at risk due to failure to properly comply with the Electricity at Work Regulations.
The consequence of the changes has been that over the last year custodial sentences have increased and both the number of senior managers prosecuted and the average level of fines have trebled for offences. Fines now regularly hit the £1M level for non-fatal offences and even cases where no injury has occurred but a lack of compliance has put employees at risk.
With 16% of all fatalities from accidents at work being electricity related, complying with Electricity at Work Regulations is fundamental to reducing accidents and avoiding heavy penalties. Implementing safe isolation procedures when working on or near electrical systems or equipment and using the right tools for the job are essential to achieve compliance.
With this in mind, Steve Dunning, managing director of Martindale Electric explains the fundamentals of implementing safe isolation procedures during installation and maintenance, and looks at the correct tools which should be used to prove dead. So what do companies need to do to achieve compliance?
The right tools for the job
Ensuring the right tools are available for the job might seem like common sense, but it’s becoming an increasing issue among maintenance staff who may be potentially putting their lives at risk whilst working on electrical plant and equipment. For example using a multimeter to prove a circuit is dead is not permissible when implementing safe isolation procedures as it could easily give a misleading reading if set to the wrong range or the batteries need replacing. A dedicated voltage indicator with no ranges, switches or batteries is essential for reliably proving dead. Having the right locking off device to hand for all types of common circuit breakers or fuse holders is also a must.
The essential test tools and equipment needed to lock off and prove dead before carrying out installation or maintenance is a dedicated voltage indicator, a proving unit to verify the voltage indicator, locking off devices with unique keys and a clear method of labelling the hazard. To ensure the right locking off device is always available, kits are available for contractors and maintenance teams working on all types of sites from residential through to commercial and industrial facilities.
Proving a circuit is dead
Locking off the circuit correctly is just one part of the procedure. Before carrying out any work, it must be verified that a circuit is dead before proceeding and in order to do so, a dedicated voltage indicator and a proving unit is a must!
In terms of the use of voltage indicators to prove dead, guidance from Electrical Safety First addresses some key points: “Following isolation of equipment or circuits and before starting work it should be proved that the parts to work on, and those nearby, are dead. It should never be assumed that equipment is dead because a particular isolation device has been placed in the OFF position.”
With this in mind, it is not enough to simply lock off the breaker and assume that the circuit is dead. A dedicated voltage indicator, a proving unit or a two-pole voltage detector should be used when carrying out this procedure. Whilst a known live source can be used to test a voltage indicator, it is recommended that a dedicated proving unit is used. The reason being is that the known live source will only light some of the LEDS on the tester, whereas a proving unit will ensure that all the LEDS on all ranges are working, again safeguarding against incorrect readings due to a faulty tester. It’s also safer to use a proving unit rather than a live circuit.
Keep up to date with important changes
However, having the correct tools for the job is just one aspect of providing a safe solution. As the person charged with compliance isn’t always a qualified electrician or engineer, understanding what’s required to implement the proper procedures is another factor which needs to be addressed.
With around 1,000 serious accidents per year at work due to contact with electricity and 10 times as many involving electricity as a cause of an accident, it is clear how important it is for companies to follow simple safe isolation procedures to avoid heavy penalties for non-compliance and to make sure staff have the correct equipment to keep safe.
- No related articles listed