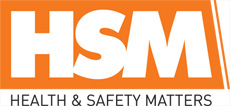
![]() |
Mark Sennett
Managing Editor |
![]() |
Kelly Rose
Editor |
Home> | Training & Development | >Courses | >Looking beyond training |
Looking beyond training
01 March 2017
Too many employers think worker training alone is the answer to reducing health and safety incidents but, as RRC International’s Pat McLoughlin argues, it must go hand in hand with investigation of underlying causes at the company level.
By law, employers are required to take various measures to ensure the health and safety of their employees – for example, supplying suitable and sufficient equipment for the tasks to be carried out, devising safe systems of work, ensuring adequate supervision and providing relevant training. The ongoing effectiveness of these measures should also be monitored but, as any health and safety professional knows, some are easier to evaluate than others, in terms of whether or not they are actually working.
If a particular machine keeps breaking down, it’s either unsuitable for the task, or it is not being properly maintained. Mechanical or system faults are relatively easy to determine – and fix – but when the error is human, the diagnosis and remedy are not so straightforward.
According to research, between 80 and 88% of accidents are caused by someone doing something silly – a fact often borne out by accident investigations. In such cases, companies that have gone to some effort and expense to train their employees bemoan the lack of return on their investment, perhaps blaming the workers for not ‘paying attention in class’, or even the training provider(s), for not doing their job properly.
But if employers went a little further in their investigations and asked, what is it that we as a company have done that has allowed this person to behave in this way, or, worse, encouraged them to do so, they would get closer to the truth.
Even when training has been specified and delivered correctly, and the trainees’ learning was evaluated, problems may still arise because the wrong issue was addressed. Often, employers specify training because they think they need to change the unsafe, or ill-informed behaviour of their workers when, in fact, the root cause of the problem is poor performance by the company.
For example, you can train a warehouse forklift-truck operator to the highest standards but if you don’t provide an equally high-standard working environment, i.e. adequate aisle widths, proper segregation of pedestrians and vehicles, sufficient lighting, good supervision, achievable work-rate targets, etc. then the operator will try to achieve their targets by bending, or even breaking the rules. The problem here is not the operator’s knowledge but their circumstances, and those are dictated by their employer.
Training in a particular subject or area in isolation is almost always ineffectual because it doesn’t take into account the influence other, more fundamental problems can have. Generally, the combined effect of poor practices across the company is greater than the impact of individual incidents of ‘silliness’. So, if you want to ensure training will change individual performance, you must begin by ensuring that all of your equipment, processes, procedures and risk assessments are suitable and sufficient.
Once you have done so, and your workers have undergone the training they need to fill the gaps you identified, you need to evaluate their learning to make sure they got the message. Many employers still do this by looking at the number of incidents and accidents that have (or have not) occurred since the training was received. This is not a meaningful measure of its effectiveness. All it tells you is there was a failure; it doesn’t give you the cause of that failure, which may or may not be linked to the training.
Furthermore, the number of incidents often increases in the post-training period. This is not because more incidents actually occur but because workers now understand that they need to report them, and how to do so.
A much more useful tool for measuring the success, or otherwise, of training is an attitude survey, which can be used to determine worker attitudes before and after training, and other consultative initiatives. They are used and promoted by the Health and Safety Executive and Health and Safety Laboratory, whose ‘Safety Climate Tool’ was employed with great results by the Olympic Delivery Authority during the building of the Olympic Park for London 2012.
Employers could also consider direct consultation with their workers, via face to face meetings with either groups or individuals, or informal ‘walkabouts’ by managers. In large workplaces, or those that are spread out, where such solutions may not be practical, indirect consultation via worker safety representatives and committee meetings can be considered.
- NEBOSH language courses from RRC
- Online HSE study materials
- Raising the bar
- Training partner February 2020
- Health & safety training in Bahrain
- Two NVQs in health and
- Training partner - June 21
- International NEBOSH training course for oil & gas industry
- Training partner - December 2020
- RRC around the world