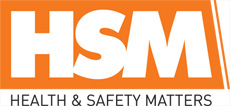
![]() |
Mark Sennett
Managing Editor |
![]() |
Kelly Rose
Editor |
Home> | Handling & Storing | >Safer Manual Handling | >Metal storage guidance updated |
Metal storage guidance updated
01 February 2017
The Health & Safety Executive has published the second version of HSG246 Safety in the storage and handling of steel and other metal stock. The guidance covers storage of metal stock, lifting and handling, as well as transportation of metal on the road. So how does this affect you?
Many accidents, some resulting in death and serious injury, continue to occur during the storage and handling of steel and other metal stock. They cause enormous social and economic cost over and above the human tragedy involved.
It is in everyone’s interest that they are reduced. Accident investigations often show that these injuries could have been avoided.
This revised guidance is aimed at directors, owners, managers and supervisors and pays particular attention to the most common hazards, including (un)loading of delivery vehicles, storage systems, workplace transport, mechanical lifting and injuries from sharp edges.
New sections compare the use of single- versus double-hoist cranes and give additional information on the safe use of pendant and remote controllers, suitable lifting accessories, working at height and providing better access arrangements with stock products. There are now specific requirements which effectively prohibit the stacking of ‘U’ frame racking and ‘barring-off’.
Banding
Banding is used to maintain the integrity of items during handling, storage and both internal and external transportation. Steel banding/wire is normally used, although plastic banding may be used for restricted cases where it has been assessed as suitable. Banding is intended to keep the load intact; it is not a lifting aid. Handling loads by their banding is likely to damage the banding, greatly increasing risk of its failure and collapse of the load.
Failure of banding resulting in collapse of free-standing stack of bundles.
In one instance, an employee was lifting bundles of tube by placing lifting hooks under the banding wire. One of the bandings failed, and the load fell and struck him, causing him serious injury.
It was found there was no provision for containing collapsing stack safely. No protected aisles for operators to work from. The root causes were: failure of banding material resulted from an unsafe lifting operation, ie lifting of a load by its banding. Poor risk assessment and lack of planning. Inadequate instruction and training to the operator in correct lifting procedures.
Barring-off
Barring-off (using levers such as metal bars, to physically lever stock off a delivery vehicle) must not be undertaken under any circumstances as there is a high risk of serious injury to people on delivery vehicles and to others in the vicinity of the vehicle. Barring-off has been carried out historically, but it is not a safe method of off-loading and has led to numerous serious and fatal accidents.
Operators cannot fully control the procedure and are at risk of crushing, particularly when unexpected stock movement occurs on the vehicle. Fatal incidents have also occurred when operators lost balance and fell from the vehicle during the barring-off process. Other people are at risk of fatal injury by being crushed or struck by stock falling from the vehicle. Manual handling injuries were also common.
Common types of supported storage systems
The guide shows the common types of supported storage systems, including different designs within each system. The Guide describe the nature of the design and the types of product commonly stored on them along with the advantages and disadvantages of each system and particular hazards and risks associated with their design, manufacture, installation, use and ongoing inspection/maintenance.
How to ensure lifting operations are safe
Lifting operations in stockholders that have resulted in serious incidents have shown that the following factors should have been identified in the lifting plan, and measures taken to address the risks:
- Lifting equipment and lifting accessories must be suitable for the task
- Adequate information should be obtained from the equipment manufacturer and provided to the user so they know how to use and maintain the equipment safely
- Safe working loads must not be exceeded
- Safe systems of work must be followed, for example to avoid the need for employees to enter danger areas or to reach between unstable or poorly supported materials to attach slings etc
- A safe place of work must be provided. For example, anyone attaching lifting accessories to stock (slinging) must be able to do so in safety and must be in a safe position when the load is lifted
- Banding wire or straps should never be used for lifting stock
- Suitable dunnage/bearers should be used to separate load components and give sufficient clearance for safe attachment of lifting accessories
- Any person using lifting equipment must be suitably trained and instructed
- Cranes should only be used for vertical lifting and not to pull or drag stock out of storage racking, as the excessive loads can damage the crane and/or racking
- The height at which loads are raised should be kept to a minimum
- Loads should never be carried or suspended over personnel
- All persons (operators and other people) should be in a position of safety where they are not at risk of being struck by the lifting equipment, the load being lifted or by falling material in the event of equipment or load failure
- Visiting drivers should also have a designated safe area where they can observe the loading/unloading process as necessary in sight of the lifting equipment operator.
You can read the full guidance here: www.hse.gov.uk/pUbns/priced/hsg246.pdf
- £1million fine for steel company after worker severely burnt
- Influential leaders invited to shape Great Britain’s future health and safety strategy
- London basement projects face safety scrutiny
- London Borough Council fined after HSE investigation
- Contractors in court after leisure centre roof fall
- Heating engineers in court over asbestos
- Hydraulic company sentenced after employee blinded in one eye
- Firm sentenced after worker hit by tractor
- Review of Health and Safety Executive launched
- Company fined £250,000 after crushing leaves worker with brain damage