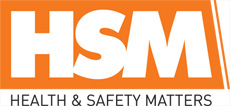
![]() |
Mark Sennett
Managing Editor |
![]() |
Kelly Rose
Editor |
Home> | Handling & Storing | >Forklift Truck Safety | >Bringing a safety strategy into the loading bay |
ARTICLE
Bringing a safety strategy into the loading bay
29 April 2013
The loading bay is fraught with hazards for forklift truck operators. Implementing a robust safety strategy using simple but effective protective equipment can make all the difference, says Mark James

The loading bay is fraught with hazards for forklift truck
operators. Implementing a robust safety strategy using
simple but effective protective equipment can make all
the difference, says Mark James
The loading and unloading area is a focal point for many businesses; as such, it brings together a high concentration of hazards. It's no wonder that, according to the Health & Safety Executive (HSE), 15% of all workplace-related accidents occur while loading or unloading, and it's often the forklift truck operator who bears the brunt.
The frustrating thing is that the majority of these accidents were preventable. All these companies lacked was a sound safety strategy, backed up with equipment and processes designed to protect the workforce. Yet too many in the industry prefer to cross their fingers and hope that nothing will happen in their yard, rather than spending the time or money on getting it right.
Without a robust safety strategy, any loading area is an accident waiting to happen - and as soon as something occurs, the company faces a huge burden in terms of downtime, repairs and possible legislative fines. Doing nothing is a false economy. Nonetheless, it requires only the use of some simple, low-cost and highly effective safety aids to ensure that you are loading and unloading with confidence.
Equipment to minimise risk Falls present a major hazard, as there is huge scope for operators of forklifts to fall where there exists a height variation and/or a horizontal gap during loading and unloading. Obviously, it is imperative that this difference is bridged, and there are various devices such as dock levelers, scissor lift tables or yardramps that can be used to give the forklift smooth and uninterrupted access to trailers. Essential accessories - for example gates and handrails - provide further support.
Movement of vehicles is another area that must be carefully controlled to avoid trapping or crushing operators, or prevent forklifts falling off the back of trailers because the driver moves off before loading has finished. A range of preventative options is available, from wheel chocks to air locks to complex key removal protocols.
Of course, none of these products on their own can fully account for the possibility of human error, so good visual and audible communication systems are a must to let drivers know when it is safe to back up to a loading dock and, perhaps more importantly, when it is safe to drive away.
Another hazard - and possibly one of the most dangerous - is when a vehicle trailer, without its cab, tips forward. This can happen if the standard landing legs fail and when the vehicle has been loaded incorrectly, or when empty it becomes unbalanced. Fortunately, the use of a trailer safety support provides immediate and effective prevention of this type of accident. Weather can also have an adverse effect on safety, from slippage caused by water ingress to health effects suffered by employees from extreme operating temperatures. The strategic use of dock seals and shelters can help warehouse managers to meet many of their 'duty of care' requirements by protecting operators from the worst the elements can throw at them.
Nonetheless, there is no better prevention than putting a robust system in place that integrates many or all of the above possibilities. Investment throughout the loading and unloading area - down to the installation of traffic lights and alarm sirens - can engender an effective and safe operating environment. Don't forget the importance of ensuring that equipment is compliant with appropriate safety standards. There can be just as great a danger in sourcing non-compliant equipment as buying nothing at all. Since market surveillance simply isn't in place currently to prevent potentially unsafe equipment entering the UK market, it's vital that purchasers use only reputable suppliers.
Yet by taking a proactive, practical attitude towards safety - using careful research and common sense - companies will find that it is not difficult to make their loading areas safe. The result is not only an environment in which forklifts can operate with confidence, but a costeffective means of improving efficiency that will add real value to your logistics operation.
Mark James is health & safety manager at Thorworld Industries
The loading and unloading area is a focal point for many businesses; as such, it brings together a high concentration of hazards. It's no wonder that, according to the Health & Safety Executive (HSE), 15% of all workplace-related accidents occur while loading or unloading, and it's often the forklift truck operator who bears the brunt.
The frustrating thing is that the majority of these accidents were preventable. All these companies lacked was a sound safety strategy, backed up with equipment and processes designed to protect the workforce. Yet too many in the industry prefer to cross their fingers and hope that nothing will happen in their yard, rather than spending the time or money on getting it right.
Without a robust safety strategy, any loading area is an accident waiting to happen - and as soon as something occurs, the company faces a huge burden in terms of downtime, repairs and possible legislative fines. Doing nothing is a false economy. Nonetheless, it requires only the use of some simple, low-cost and highly effective safety aids to ensure that you are loading and unloading with confidence.
Equipment to minimise risk Falls present a major hazard, as there is huge scope for operators of forklifts to fall where there exists a height variation and/or a horizontal gap during loading and unloading. Obviously, it is imperative that this difference is bridged, and there are various devices such as dock levelers, scissor lift tables or yardramps that can be used to give the forklift smooth and uninterrupted access to trailers. Essential accessories - for example gates and handrails - provide further support.
Movement of vehicles is another area that must be carefully controlled to avoid trapping or crushing operators, or prevent forklifts falling off the back of trailers because the driver moves off before loading has finished. A range of preventative options is available, from wheel chocks to air locks to complex key removal protocols.
Of course, none of these products on their own can fully account for the possibility of human error, so good visual and audible communication systems are a must to let drivers know when it is safe to back up to a loading dock and, perhaps more importantly, when it is safe to drive away.
Another hazard - and possibly one of the most dangerous - is when a vehicle trailer, without its cab, tips forward. This can happen if the standard landing legs fail and when the vehicle has been loaded incorrectly, or when empty it becomes unbalanced. Fortunately, the use of a trailer safety support provides immediate and effective prevention of this type of accident. Weather can also have an adverse effect on safety, from slippage caused by water ingress to health effects suffered by employees from extreme operating temperatures. The strategic use of dock seals and shelters can help warehouse managers to meet many of their 'duty of care' requirements by protecting operators from the worst the elements can throw at them.
Nonetheless, there is no better prevention than putting a robust system in place that integrates many or all of the above possibilities. Investment throughout the loading and unloading area - down to the installation of traffic lights and alarm sirens - can engender an effective and safe operating environment. Don't forget the importance of ensuring that equipment is compliant with appropriate safety standards. There can be just as great a danger in sourcing non-compliant equipment as buying nothing at all. Since market surveillance simply isn't in place currently to prevent potentially unsafe equipment entering the UK market, it's vital that purchasers use only reputable suppliers.
Yet by taking a proactive, practical attitude towards safety - using careful research and common sense - companies will find that it is not difficult to make their loading areas safe. The result is not only an environment in which forklifts can operate with confidence, but a costeffective means of improving efficiency that will add real value to your logistics operation.
Mark James is health & safety manager at Thorworld Industries
MORE FROM THIS COMPANY
OTHER ARTICLES IN THIS SECTION